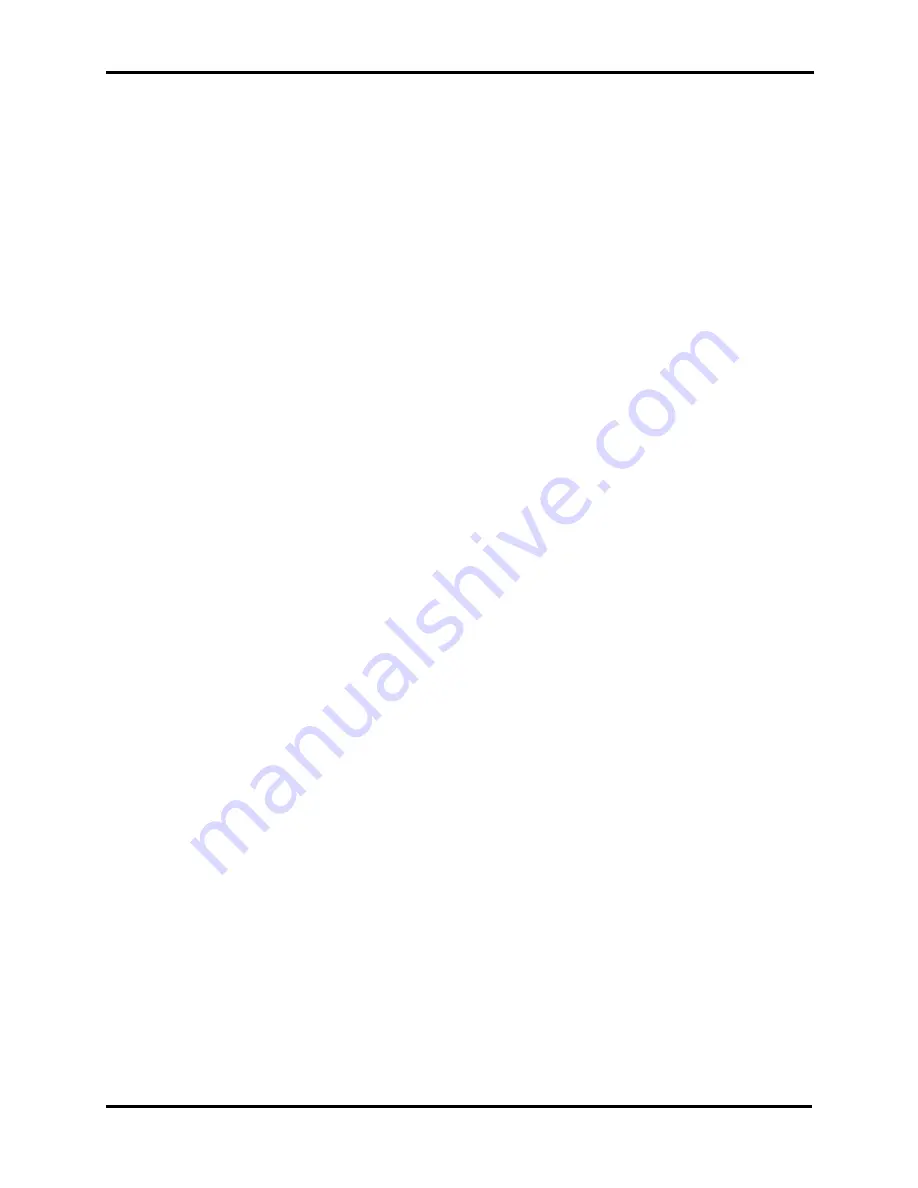
Rev 37
Operator’s Manual
OM-610-1002-1
page 16
SECTION 5 OPERATION
PDS-2010
be the case. Outgassing, the slow release of trapped gases and vapors from the interior surfaces and materials
of the vacuum system and the substrate, will act to lengthen the actual pump down time.
Many gas molecules are attached to surfaces and are gradually released as the system pressure lowers. Other
molecules may be imbedded in certain substrate materials (such as rubber, plastics, and fibrous materials)
which, under vacuum, diffuse through the material toward its surface and are eventually released to the
vacuum chamber. Minute cracks and spaces can trap molecules which will not release until lower pressures
are achieved within the chamber. Extremely small leaks will also provide a steady stream of molecules into
the vacuum vessel, which can be difficult to discern from true outgassing. Regardless of the cause, severe
outgassing will result in longer pump down times, and can have detrimental effects on coating quality.
5.2.7 Base Pressure
Base pressure is defined as the lowest attainable steady state pressure of a given vacuum system. There is a
practical limit to its value. Due to variations in vacuum components, monitoring equipment, and substrate
composition, the base pressure of a particular vacuum system can vary over time and from machine to
machine. Refer to Section 5.10 of this manual for the procedures to determine the base pressure.
Pressure Location:
The one location in the system where pressure is monitored is the chamber. The
chamber pressure is the pressure that is most critical to the process description. Unless otherwise
specified, any references to pressure by SCS will mean the chamber pressure.
Hot or Cold Base Pressure:
The chamber pressure sensor (simply called “gauge tube” here) is heated
during processing so that Parylene does not deposit on it. A thermocouple in it senses the temperature.
This heating
does
change the tube’s response, but in a small, repeatable, and predictable way. Hot base
pressure of a system is the base pressure read when the gauge tube is heated to its normal processing
temperature. Cold base pressure means that NO component in the system is heated during the
measurement; this does not normally occur except when special testing is being done.
The SCS convention is that whenever base pressure is used, it is understood to be hot base pressure. If
other components in the system are heated, these conditions must be clearly explained and understood.
5.2.8 Coating Pressure
Coating pressure is generally defined as the desired chamber pressure to be maintained during a vacuum
process. With Parylene deposition systems, coating pressure is the most important factor affecting substrate
coating quality. In general, a higher coating pressure will result in a shorter coating cycle, but excessive
coating pressures will result in unacceptable coating quality- such as cloudiness, frosting, or formation of
coating nodules. The process goal is to identify the highest coating pressure that results in an acceptable
coating quality for each application.
5.3
PARYLENE DEPOSITION TECHNOLOGY
5.3.1 Parylene Types
Parylene is the generic name of members of a unique polymer series developed by Union Carbide
Corporation. As the Parylene deposition process matured, a group eventually separated from the parent
company, and SCS was formed.
Parylene is applied in the vacuum chamber at room temperature. Deposition takes place at the molecular
level as the chemical is converted under vacuum and heat from the powdered dimer form to a clear
Summary of Contents for LABCOTER 2
Page 3: ...OM 610 1002 1 Operator s Manual Rev 37...
Page 4: ...Rev 37 Operator s Manual OM 610 1002 1...
Page 14: ...Rev 37 Operator s Manual OM 610 1002 1 page 6 SECTION 2 OVERVIEW PDS 2010...
Page 44: ......
Page 66: ...Rev 37 Operator s Manual OM 610 1002 1 page 58 SECTION 6 MAINTENANCE PDS 2010...
Page 68: ...Rev 37 Operator s Manual OM 610 1002 1 page 60 SECTION 7 COMPONENT LOCATION PDS 2010...
Page 70: ...Rev 37 Operator s Manual OM 610 1002 1 page 62 SECTION 7 COMPONENT LOCATION PDS 2010...
Page 72: ...Rev 37 Operator s Manual OM 610 1002 1 page 64 SECTION 7 COMPONENT LOCATION PDS 2010...
Page 74: ...Rev 37 Operator s Manual OM 610 1002 1 page 66 SECTION 7 COMPONENT LOCATION PDS 2010...
Page 76: ...Rev 37 Operator s Manual OM 610 1002 1 page 68 SECTION 7 COMPONENT LOCATION PDS 2010...
Page 78: ...Rev 37 Operator s Manual OM 610 1002 1 page 70 SECTION 7 COMPONENT LOCATION PDS 2010...
Page 80: ...Rev 37 Operator s Manual OM 610 1002 1 page 72 SECTION 7 COMPONENT LOCATION PDS 2010...
Page 82: ...Rev 37 Operator s Manual OM 610 1002 1 page 74 SECTION 7 COMPONENT LOCATION PDS 2010...
Page 84: ...Rev 37 Operator s Manual OM 610 1002 1 page 76 SECTION 7 COMPONENT LOCATION PDS 2010...
Page 86: ...Rev 37 Operator s Manual OM 610 1002 1 page 78 SECTION 7 COMPONENT LOCATION PDS 2010...
Page 88: ...Rev 37 Operator s Manual OM 610 1002 1 page 80 SECTION 7 COMPONENT LOCATION PDS 2010...
Page 90: ...Rev 37 Operator s Manual OM 610 1002 1 page 82 SECTION 7 COMPONENT LOCATION PDS 2010...
Page 92: ...Rev 37 Operator s Manual OM 610 1002 1 page 84 SECTION 7 COMPONENT LOCATION PDS 2010...
Page 94: ...Rev 37 Operator s Manual OM 610 1002 1 page 86 SECTION 7 COMPONENT LOCATION PDS 2010...
Page 96: ...Rev 37 Operator s Manual OM 610 1002 1 page 88 SECTION 7 COMPONENT LOCATION PDS 2010...
Page 98: ...Rev 37 Operator s Manual OM 610 1002 1 page 90 SECTION 7 COMPONENT LOCATION PDS 2010...
Page 100: ...Rev 37 Operator s Manual OM 610 1002 1 page 92 SECTION 7 COMPONENT LOCATION PDS 2010...
Page 102: ...Rev 37 Operator s Manual OM 610 1002 1 page 94 SECTION 7 COMPONENT LOCATION PDS 2010...
Page 104: ...Rev 37 Operator s Manual OM 610 1002 1 page 96 SECTION 7 COMPONENT LOCATION PDS 2010...
Page 106: ...Rev 37 Operator s Manual OM 610 1002 1 page 98 SECTION 7 COMPONENT LOCATION PDS 2010...
Page 108: ...Rev 37 Operator s Manual OM 610 1002 1 page 100 SECTION 7 COMPONENT LOCATION PDS 2010...
Page 110: ...Rev 37 Operator s Manual OM 610 1002 1 page 102 SECTION 7 COMPONENT LOCATION PDS 2010...
Page 112: ...Rev 37 Operator s Manual OM 610 1002 1 page 104 SECTION 7 COMPONENT LOCATION PDS 2010...
Page 114: ...Rev 37 Operator s Manual OM 610 1002 1 page 106 SECTION 7 COMPONENT LOCATION PDS 2010...
Page 116: ...Rev 37 Operator s Manual OM 610 1002 1 page 108 SECTION 7 COMPONENT LOCATION PDS 2010...
Page 128: ...Rev 37 Operator s Manual OM 610 1002 1 page 120 SECTION 10 WARRANTY PDS 2010...
Page 130: ...Rev 37 Operator s Manual OM 610 1002 1 page 122 SECTION 10 WARRANTY PDS 2010...
Page 131: ...PDS 2010 SCHEMATICS page 123 ES 610 1001 2 CE ELECTRICAL SCHEMATIC 1 OF 2...
Page 132: ...page 124 SCHEMATICS PDS 2010...
Page 133: ...PDS 2010 SCHEMATICS page 125 ES 610 1001 2 CE ELECTRICAL SCHEMATIC 2 OF 2...
Page 134: ...page 126 SCHEMATICS PDS 2010...
Page 135: ...PDS 2010 SCHEMATICS page 127 ES 610 1068 1 DOMESTIC ELECTRICAL SCHEMATIC 1 OF 3...
Page 136: ...page 128 SCHEMATICS PDS 2010...
Page 137: ...PDS 2010 SCHEMATICS page 129 ES 610 1068 1 DOMESTIC ELECTRICAL SCHEMATIC 2 OF 3...
Page 138: ...page 130 SCHEMATICS PDS 2010...
Page 139: ...PDS 2010 SCHEMATICS page 131 ES 610 1068 1 DOMESTIC ELECTRICAL SCHEMATIC 3 OF 3...
Page 140: ...page 132 SCHEMATICS PDS 2010...
Page 141: ...PDS 2010 SCHEMATICS page 133 ES 610 1001 5 220V ELECTRICAL SCHEMATIC 1 OF 3...
Page 142: ...page 134 SCHEMATICS PDS 2010...
Page 143: ...PDS 2010 SCHEMATICS page 135 ES 610 1001 5 220V ELECTRICAL SCHEMATIC 2 OF 3...
Page 144: ...page 136 SCHEMATICS PDS 2010...
Page 145: ...PDS 2010 SCHEMATICS page 137 ES 610 1001 5 220V ELECTRICAL SCHEMATIC 3 OF 3...
Page 146: ...page 138 SCHEMATICS PDS 2010...
Page 147: ...PDS 2010 SCHEMATICS page 139 ES 610 1065 1 200V ELECTRICAL SCHEMATIC 1 OF 3...
Page 148: ...page 140 SCHEMATICS PDS 2010...
Page 149: ...PDS 2010 SCHEMATICS page 141 ES 610 1065 1 200V ELECTRICAL SCHEMATIC 2 OF 3...
Page 150: ...page 142 SCHEMATICS PDS 2010...
Page 151: ...PDS 2010 SCHEMATICS page 143 ES 610 1065 1 200V ELECTRICAL SCHEMATIC 3 OF 3...
Page 152: ...page 144 SCHEMATICS PDS 2010...