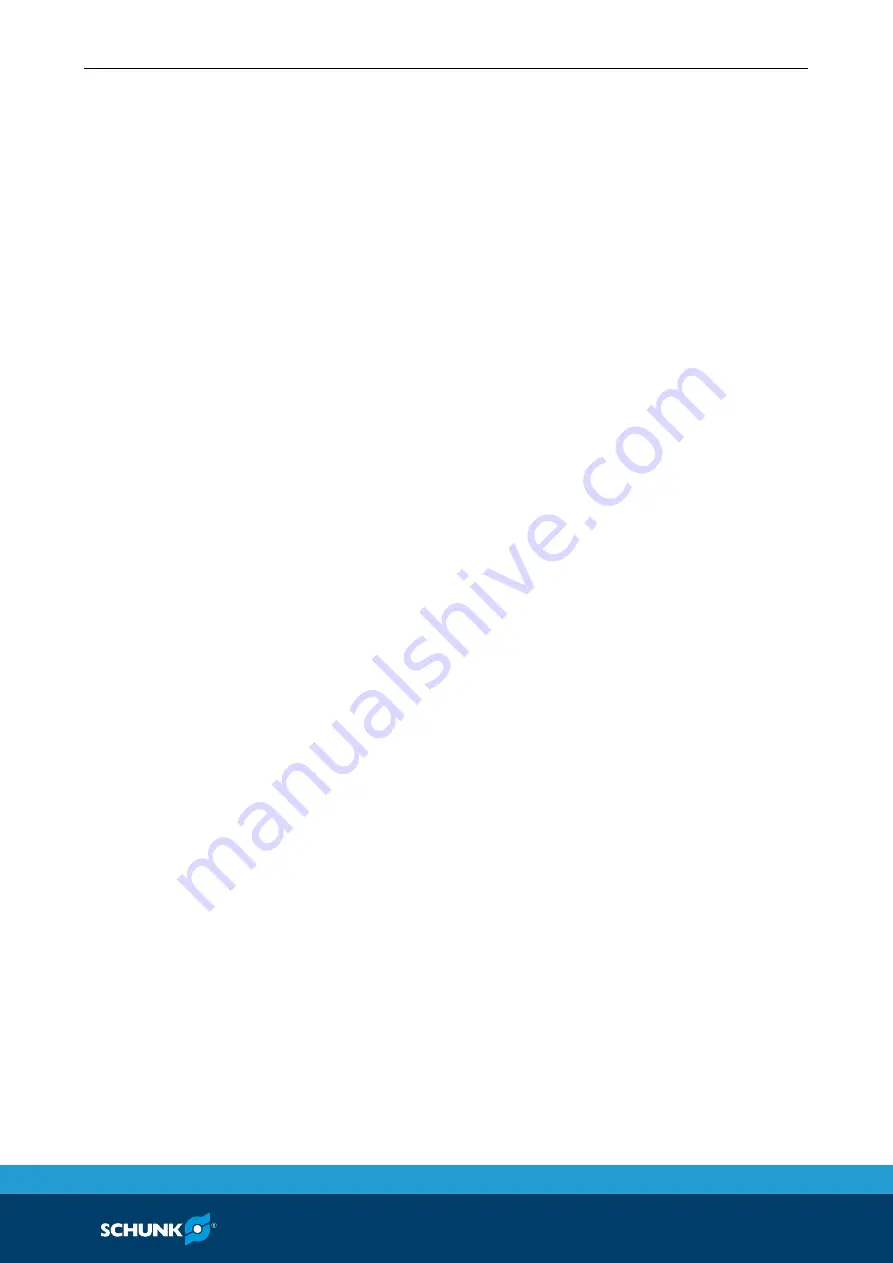
Basic safety notes
01.00|KSP3-IM, KSP3-LH-IM |en
15
Protection against dangerous movements
Unexpected movements
Residual energy in the system may cause serious injuries while
working with the product.
• Switch off the energy supply, ensure that no residual energy
remains and secure against inadvertent reactivation.
• Never rely solely on the response of the monitoring function to
avert danger. Until the installed monitors become effective, it
must be assumed that the drive movement is faulty, with its
action being dependent on the control unit and the current
operating condition of the drive. Perform maintenance work,
modifications, and attachments outside the danger zone
defined by the movement range.
• To avoid accidents and/or material damage, human access to
the movement range of the machine must be restricted.
Limit/prevent accidental access for people in this area due
through technical safety measures. The protective cover and
protective fence must be rigid enough to withstand the
maximum possible movement energy. EMERGENCY STOP
switches must be easily and quickly accessible. Before starting
up the machine or automated system, check that the
EMERGENCY STOP system is working. Prevent operation of the
machine if this protective equipment does not function
correctly.
2.13.3