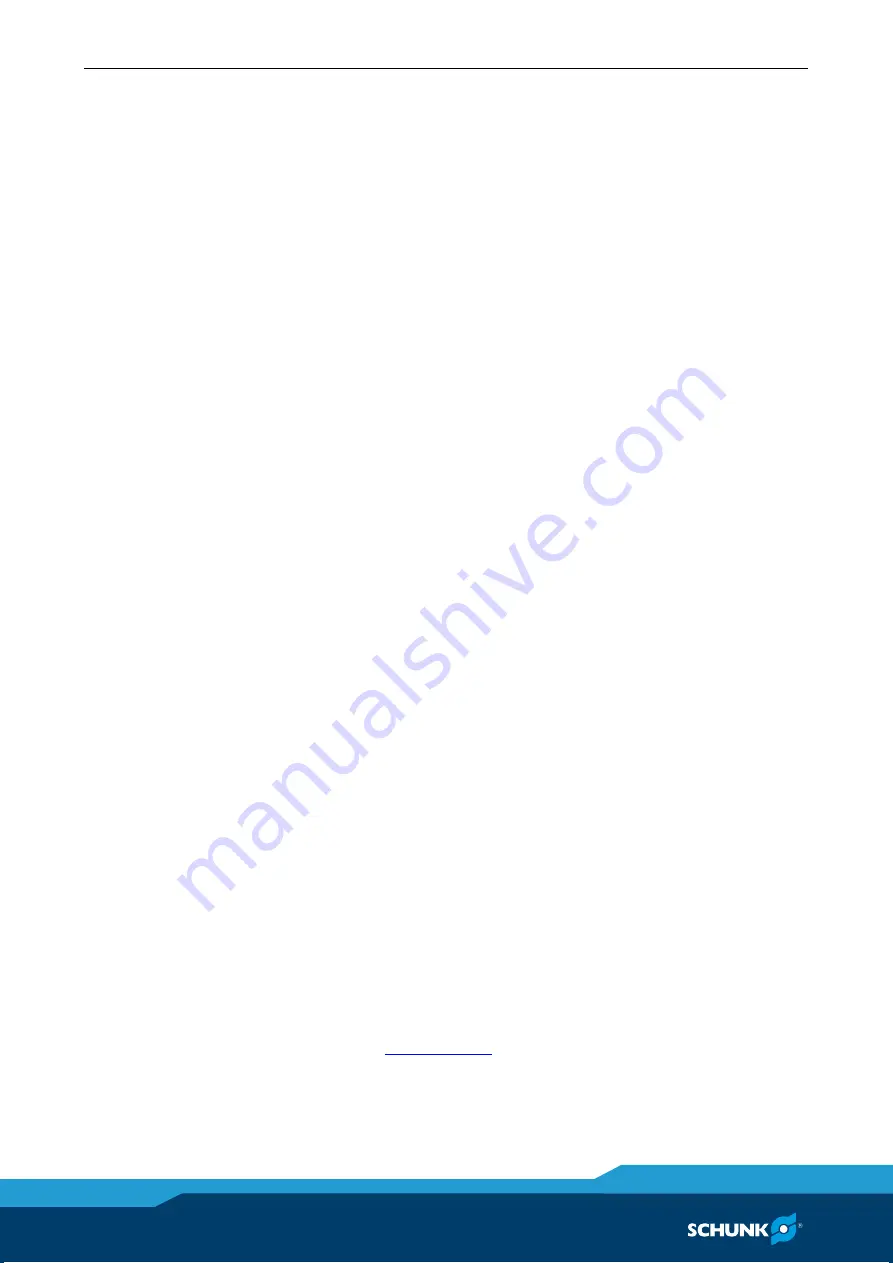
Basic safety notes
8
01.02|SPG 100|en
Product safety
Dangers arise from the product, if:
• the product is not used in accordance with its intended
purpose.
• the product is not installed or maintained properly.
• the safety and installation notes are not observed.
Avoid any manner of working that may interfere with the function
and operational safety of the product.
Wear protective equipment.
NOTE
More information are contained in the relevant chapters.
Protective equipment
Provide protective equipment per EC Machinery Directive.
Demands on the top jaws
Arrange the top jaws such that when the product is depressurized
it can reach one of the end positions either open or closed and
therefore no residual energy can be released when changing the
top jaws.
Constructional changes, attachments, or modifications
Additional drill holes, threads, or attachments that are not offered
as accessories by SCHUNK may be attached only with permission
of SCHUNK.
Personnel qualification
The assembly, initial commissioning, maintenance, and repair of
the product may be performed only by trained specialist
personnel. Every person called upon by the operator to work on
the product must have read and understood the complete
assembly and operating manual, especially the chapter "Basic
safety notes"
. This applies particularly to personnel
only used occasionally, such as maintenance personnel.
2.4
2.4.1
2.4.2
2.4.3
2.5
www.comoso.com