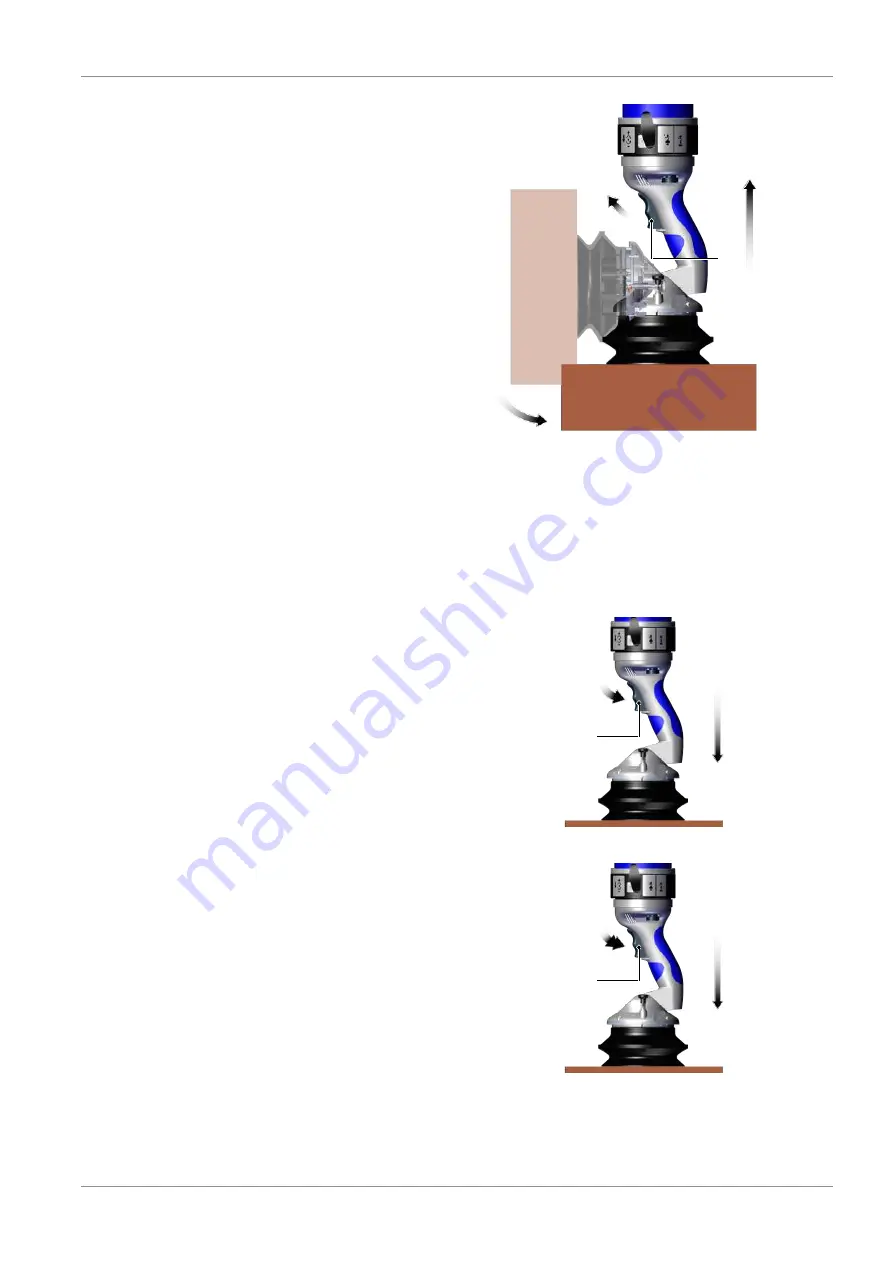
Operation
EN-US · 30.30.01.02553 · 00 · 09/20
41 / 52
3. Release the pushbutton (6.3) slowly.
6.3
ð
The tube lifter raises the load.
ð
The load slowly swivels into a horizontal position due to gravity.
7.8 Setting Down the Load
1. Position the load over the desired depositing
location.
2. Slowly press the pushbutton (6.3) to the first
pressure point.
6.3
ð
The tube lifter lowers itself.
3. Once the load has been set down safely, press
the pushbutton (6.3) past the first pressure
point up to the limit stop.
6.3