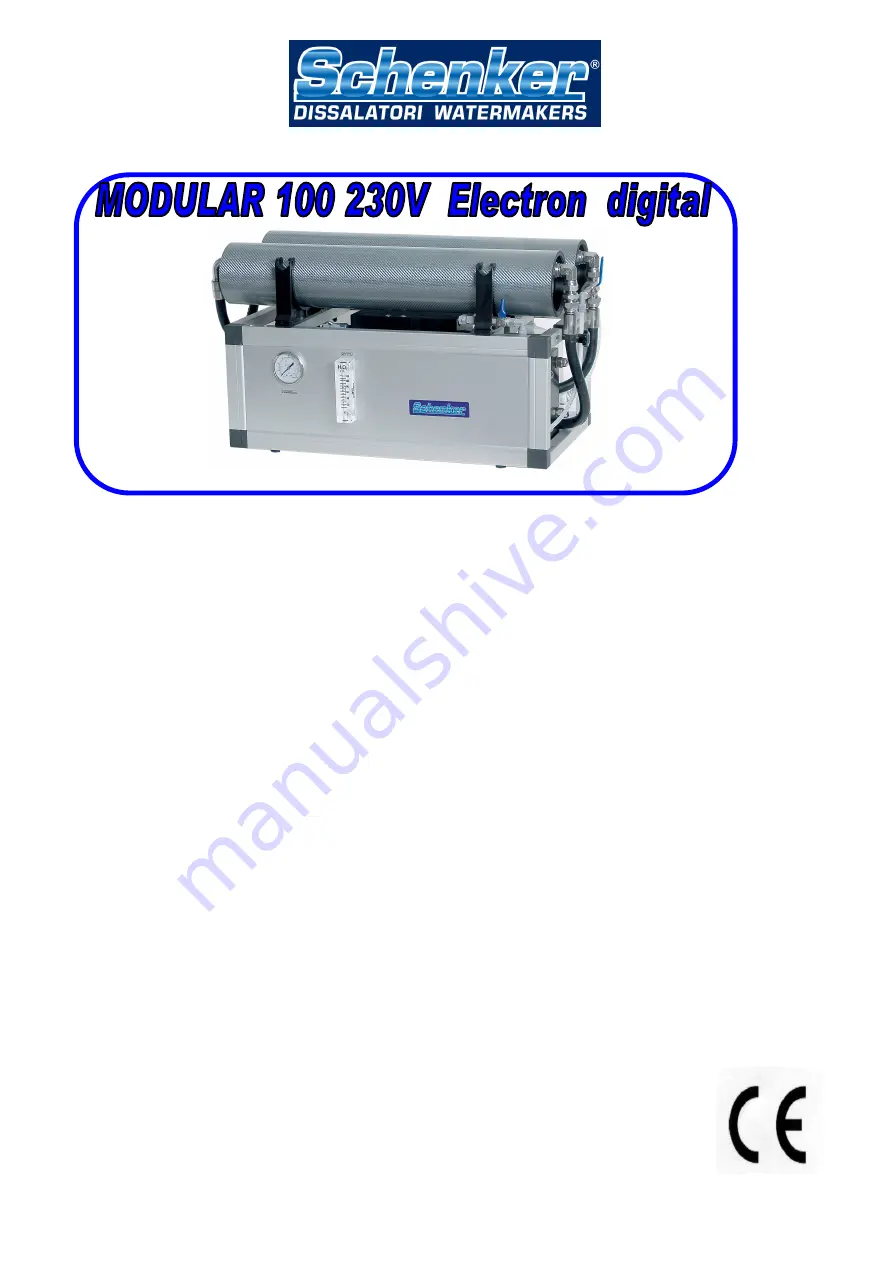
1
OPERATION AND MAINTENANCE MANUAL
1.
Introduction
1.1.
General
1.2.
Technical data
1.3.
System description
2.
Installation
2.1.
General criteria and material required
2.2.
Components mounting
2.3.
Water intake
2.4.
Hydraulic connections
2.5.
Electric connections
3.
Operating procedures
3.1. Remote panel commands
3.2.
First start-up procedure
3.3.
Normal operations
4.
Maintenance
4.1.
Shutdown procedure
4.2.
Maintenance and recurrent inspections
4.3.
Troubleshooting
5. Safety cautions
6. Warranty
Rev. 2011