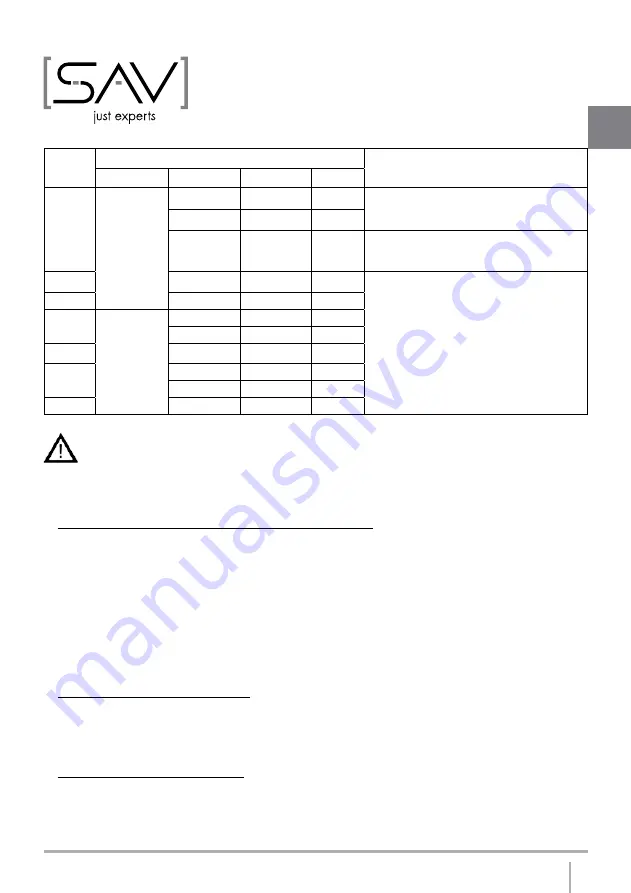
Technical Data subject to change without prior notice
31
EN
BAL 876.10 / .02
OPERATING INSTRUCTIONS
For Electronic Polarity Reversing Control Units
WORKHOLDING AND AUTOMATION
The setting of magnet type must be done according to the named procedure because of
safety. Please note, that a wrong setting for Electro-Permanent-Magnets at controllers for
electro-magnets can destroy the chuck!
For setting of magnet type, there are the listed parameters available:
display /
value
description magnetic chuck
remark
magnet type chuck voltage mains voltage frequency
EL
electro-
magnetic
chucks
24 V DC
230 V AC
50 Hz
Transformer with 32 V at second side needed to be
connected before mains voltage terminals. Change of
chuck type is not possible by sluffing switches! In case
of needed change, hard ware must be changed.
24 V DC
400 V AC
50 Hz
110 V DC
400 V AC
50 Hz
Transformer with 230 V at second side needed to be
connected before mains voltage terminals. Change of
chuck type is not possible by sluffing switches! In case
of needed change, hard ware must be changed.
EL-SO
110 V DC
230 V AC
50 Hz
no transformer needed
ELS 60
110 V DC
230 V AC
60 Hz
EP
electro-
permanent
magnetic
chucks
210 V DC
230 V AC
50 Hz
360 V DC
400 V AC
50 Hz
EP-SO
210 V DC
400 V AC
50 Hz
EP 60
210 V DC
230 V AC
60 Hz
360 V DC
400 V AC
60 Hz
EPS 60
210 V DC
400 V AC
60 Hz
After connection of the electro or electro-permanent magnetic chuck (see operation instruction
of the chuck), the release relay (terminal 7 and 8) with the machine control and the power
supply, the magnetic installation is ready to work. Stand-by is indicated by the repeated
blinking of the red lamp.
The magnetic force will be provided after pressing the green button or when the corresponding
24 V DC start signal from an external controller is available (see terminal 5 to 18). For
control-units with a yellow button for two hand operation, press both together at the same
time. Terminal 11 is connected with 13. The available holding force corresponds with the
preset amount of the force regulator.
The positioning of the work piece under reduced holding force is possible with the lower
steps of the regulator (see terminals 15 to 18 and BCD-coding).
To work under full holding force, the step regulator must be at its highest position (step 8 or 16
respectively). Please note, that for electro-permanent chucks a reliable and repetitive change
of holding-force is not possible while the chuck is on. So you have to demagnetize before
changing the level of holding force. After checking the holding force, machining can start.
After machining, one can unload and demagnetize the work piece by pressing the red button
or providing the corresponding 24 V DC signals from an external controller. The button starts
the demagnetization cycle with a short contact between terminal 11 and 14. The blinking red
lamp shows the decreasing cycles. When the demagnetization is finished, the work piece
can be removed and the red light remains on.
3. Operation:
a) Positioning of work piece under reduced holding force:
b) Machining with full holding force:
c) Unloading and demagnetisation: