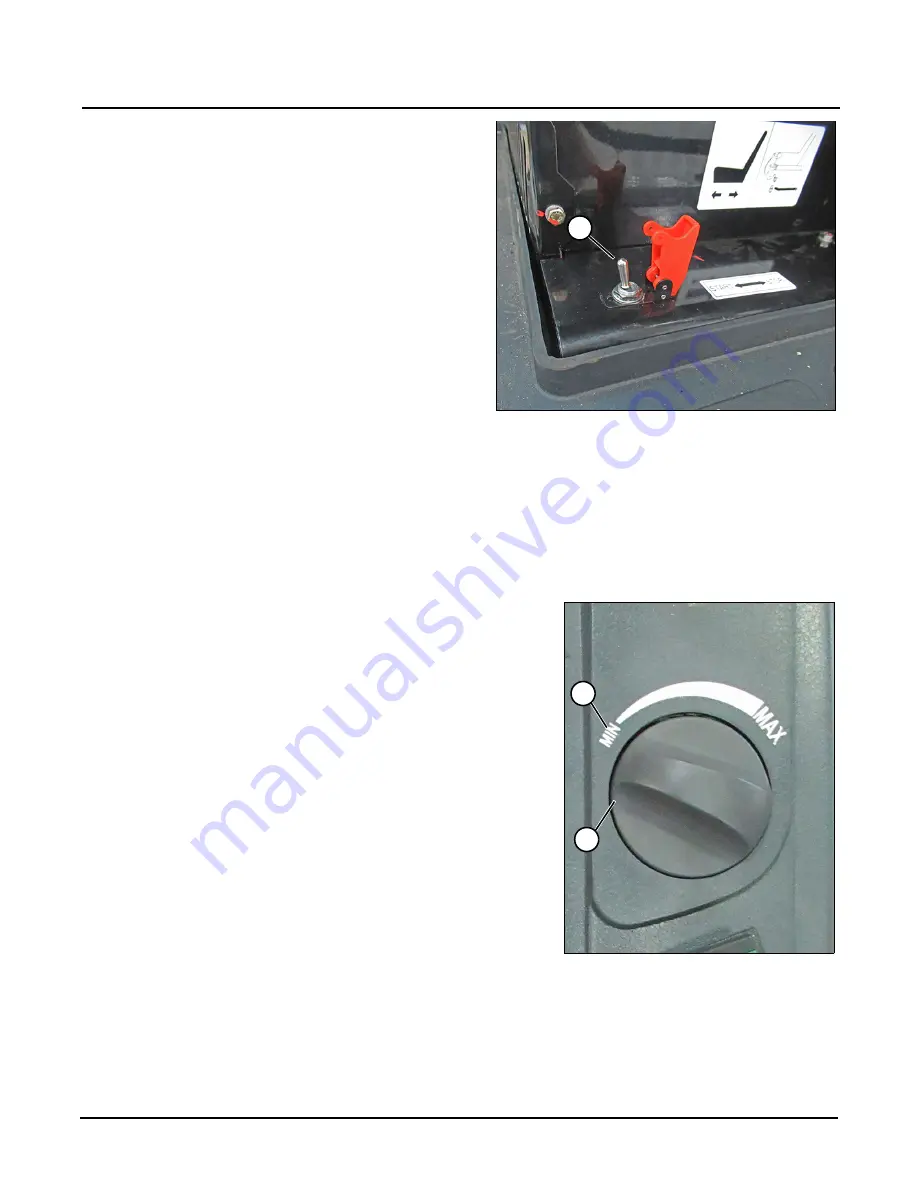
Machine Operation
SY215C LC/SY225C LC Excavator OMM
4-10
Operation and Maintenance Manual — 1219
SANY
5. Make sure the emergency stop switch is set to its forward
position with the red cover (2) over it.
6. Turn the throttle control dial (4) counterclockwise to the MIN (3)
position.
NOTICE!
Before starting the engine, make sure that the throttle control dial is at MIN (low idle). Starting
with the throttle control dial at MAX (high idle) will accelerate the engine and cause damage it.
Fig. 4-3
2
0004651
Fig. 4-4
3
4
0004591