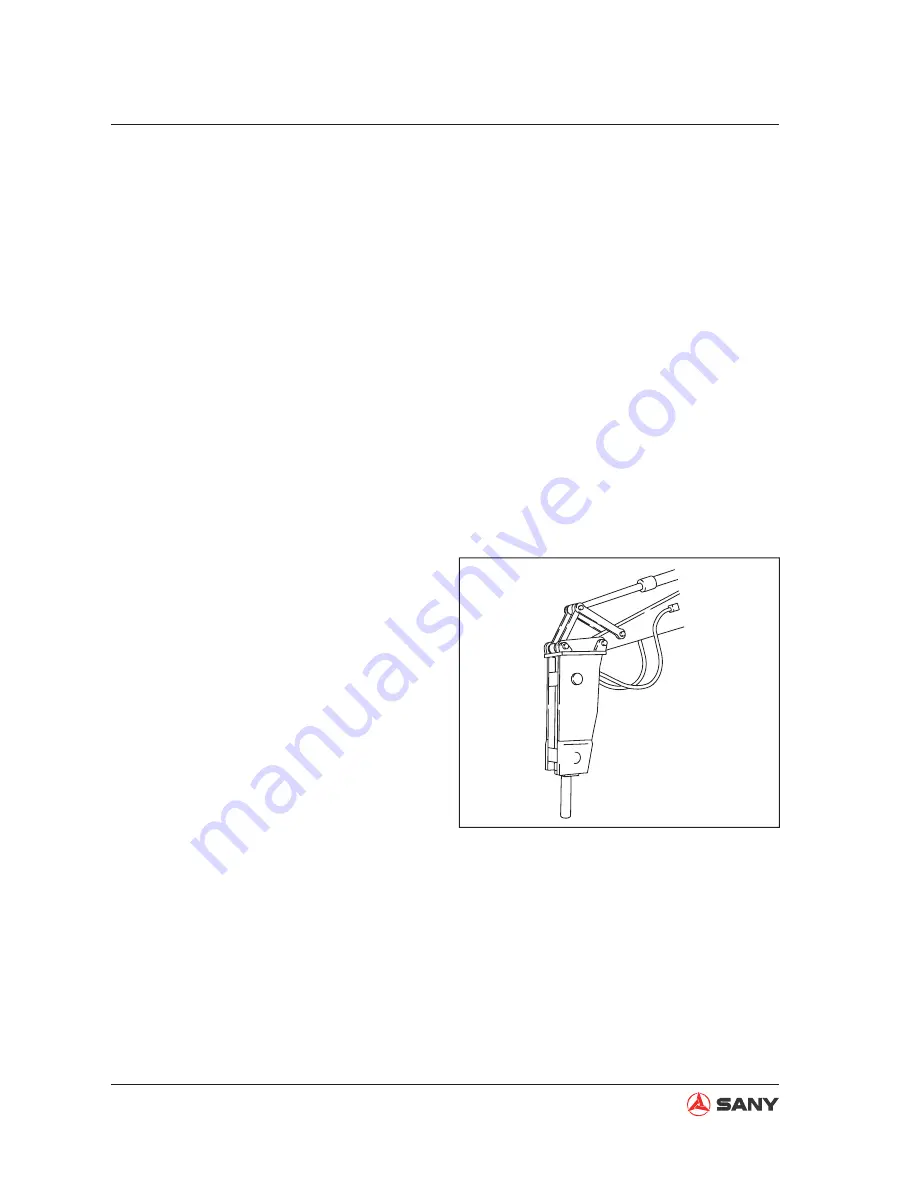
Optional Equipment
Safety, Operation and Maintenance Manual - Aug 2012
8-20
SY115C9/135C/155H Crawler Hydraulic Excavator
8.4 Recommended Operations
The following instruction must be followed
when operating an excavator with optional
equipment.
Note:
Select the optimum model of optional equip-
ment for your hydraulic excavator.
●
The type of optional equipment to be in-
stalled and the model of special optional
equipment may vary according to the mod-
el of your hydraulic cylinder. In this case,
for selecting the optimum optional equip-
ment, please consult Sany distributor.
8.4.1 Hydraulic breaker
Major applications:
●
Crushing rocks
●
Demolition
●
Road Engineering
This optional equipment can be used widely
for, such as demolishing buildings, breaking
road surface or slag, tunneling, crushing rocks,
and breaking operation at quarry.
CZ335-1105016
Fig. 8-22