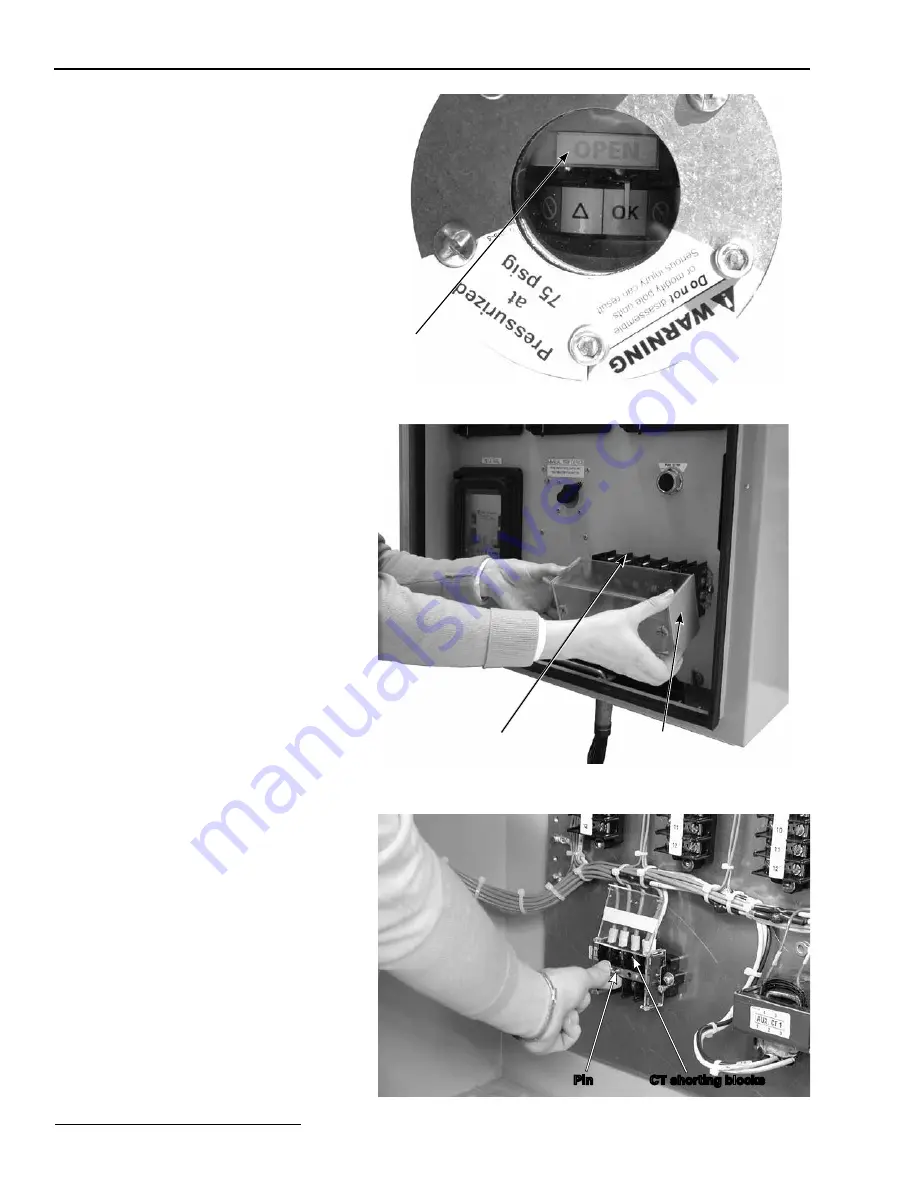
“OPEN” and
discharged
Figure 57. Check that each pole-unit position indicator shows “OPEN”
and discharged.
Step 50
To initiate a trip operation, inject secondary
current into the relay. Refer to the relay manu-
facturer’s instructions.
Step 51
Verify that the pole-units operated properly.
Check that each pole-unit position indicator
shows “OPEN” and discharged. See Figure 57.
Step 52
To initiate a trip operation, inject secondary
current into the relay. Refer to the relay manu-
facturer’s instructions.
To check operation of the trip-energy supply,
inject single-phase secondary current above
600 mA, but
below
the pick-up setting of
the relays, into the trip-energy supply, with
600 mA input current the trip-energy supply
will charge in approximately 3 seconds. Use a
user-furnished secondary current-injection kit
as follows:
a.
If an optional test switch is furnished,
remove the test-switch cover and inject sec-
ondary current in accordance with stan dard
operating procedure. See Figure 58.
b.
If the optional test switch is not fur-
nished,
use the CT shorting blocks in the
control cabinet to inject secondary current.
Use the furnished pins to short the CTs, then
inject secondary current, in accor dance
with standard operating procedures. See
Figure 59.
Control Cabinet Set-Up
Figure 58. Remove the test-switch cover and inject secondary current, in
accordance with standard procedure.
Test switch
Cover
Figure 59. If optional test switch is not furnished, place pins in the CT
shorting blocks.
Pin
CT shorting blocks
30
S&C Instruction Sheet 731-502