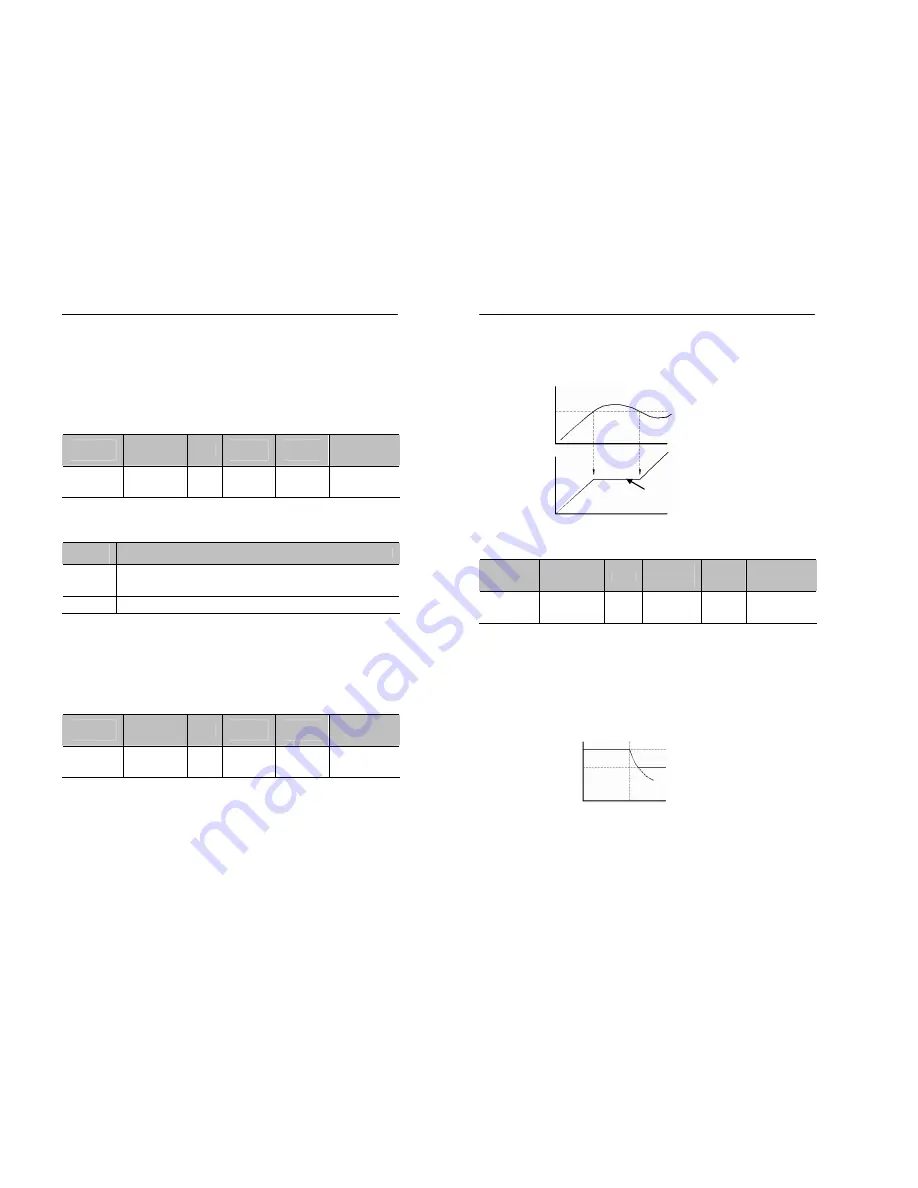
5. Parameters
5-65
5.8.3 Stall prevention
• Stall occurs when the rotor cannot keep up with the rotating magnetic
field on the motor start side.
e.g. a large load is applied to the motor and sudden acceleration or
deceleration is performed, etc.
5.8.3.1 Stall prevention at start : P2.01
Parameter
No.
Name
Unit
Setting
range
Factory
Setting
Changeable
during
operation
P2.01
Stall
Prevention
at Start
- 0~1 1
X
• P2.01 can be used to set the stall prevention function at start.
• Setting
Setting
constant
Function
0
Disabled
(The motor with excessive load is possibly stalled. Then a longer
acceleration time and reduced load is required.)
1 Enabled
• When setting 1 is selected, acceleration is stopped if the motor current
exceeds the acceleration stall prevention level(P2.02). Acceleration is
started again when the current falls below this level. The actual
acceleration time can be longer than the set value (at F2.01) depending
on the load.
5.8.3.2 Stall prevention level at start : P2.02
Parameter
No.
Name
Unit
Setting
range
Factory
Setting
Changeable
during
operation
P2.02
Stall
Prevention
Level at Start
1% 0~200 170
O
• P2.02 can be used to set the output current limit level as a percentage of
rated current of the inverter at start.
(i.e. 100% corresponds to the rated current of the inverter)
• This setting is valid when P2.01 is let to 1.
• Normally it isn’t necessary to change this setting.
5-66
MOSCON-E7 User’s Manual
• Decrease this setting when:
- The motor capacity is small compared to the inverter capacity
- Stall occurs when the motor is operated with the factory setting
Figure 5.25 Acceleration Stall Prevention function : P2.01=1
5.8.3.3 Stall prevention limit during acceleration : P2.03
Parameter
No.
Name
Unit
Setting
range
Factory
Setting
Changeable
during
operation
P2.03
Stall
Prevention at
Acc. Limit
1% 0~100 50
O
• P2.03 can be used to set the stall prevention limit when high-speed
motor is being used in the high-speed range
(the high frequency range above the base frequency)
• Normally it isn’t necessary to change this setting.
• The standard target setting is the motor’s rated current.
• Set P2.03 as a percentage of the inverter’s rated current.
(i.e. 100% corresponds to the inverter’s rated current)
Figure 5.26 Stall prevention limit during acceleration
Acceleration stall
prevention level
C0.01
P2.02
P2.03
Base frequency (FA)
(Acceleration stall
prevention level)
(Acceleration stall
prevention limit)
Output frequency
Time
Time
Output
current
Output
frequency
P2.02
(Acceleration stall prevention level)
The output frequency is
controlled to prevent stall