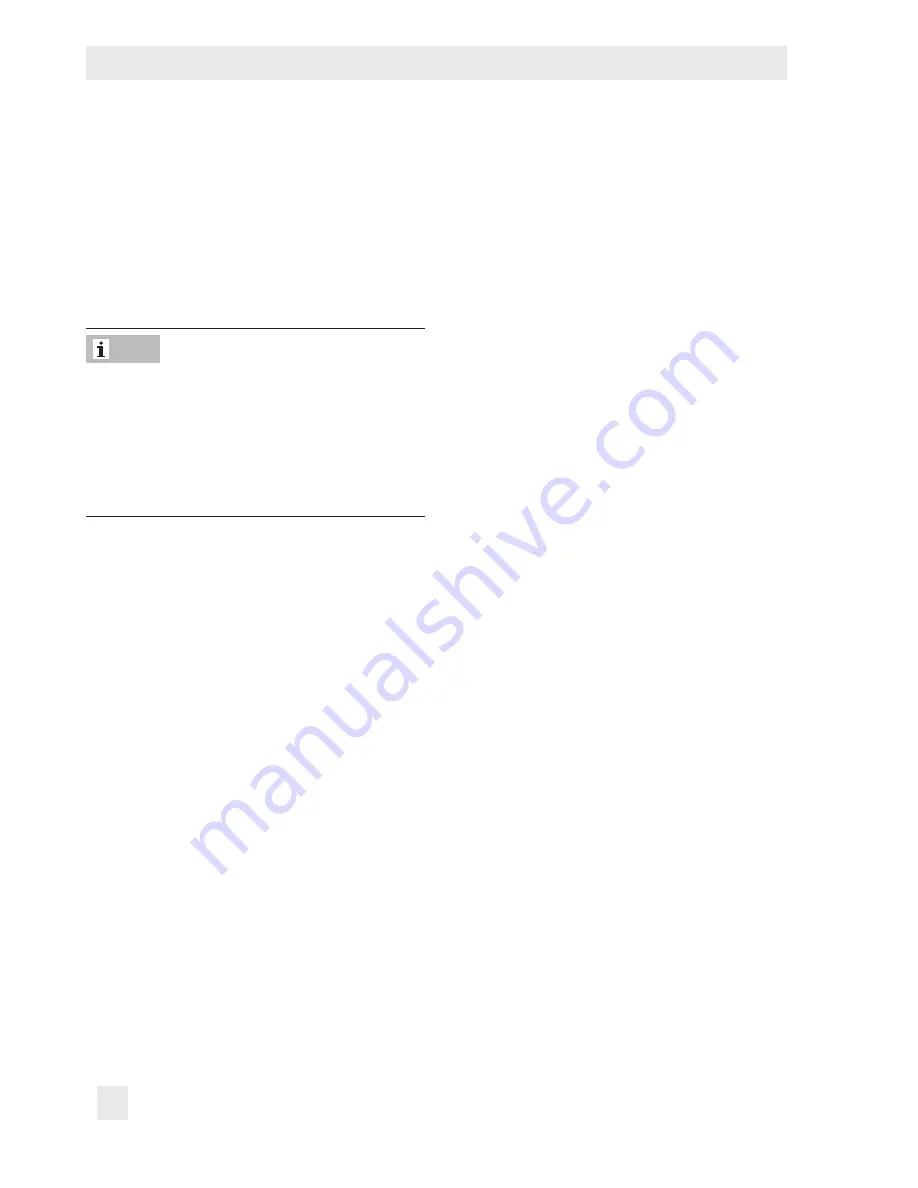
32
EB 8384-2 EN
Attachment to the control valve – Mounting parts and accessories
6.
Insert the formed seal (17.1) into the
turnboard (17) and mount the turnboard
to the adapter block (13) using the
screws (17.2).
7. Mount the blank plate (18) to the turn
-
board using the screws (18.1). Make
sure that the seals are correctly seated.
A solenoid valve can also be mounted in
place of the blank plate (18). The orientation
of the turnboard (17) determines the mount-
ing position of the solenoid valve. Alterna
-
tively, a restrictor plate can be mounted
(
u
AB 11).
8.
Fasten the adapter block (13) to the
NAMUR connection block using the
screws (13.1).
9. Insert the vent plug into the Exh. connec
-
tion.
10. Place the positioner on the adapter block
(13) in such a manner that the follower
pin (2) rests on the top of the follower
plate (3, 3.1). Adjust the lever (1) corre
-
spondingly.
Fasten the positioner to the adapter block
(13) using the two fastening screws (6.3).
Make sure the formed seal (6.2) is prop-
erly seated.
11. For
single-acting actuators without air
purging
, connect the Y1 port of the
adapter block to the signal pressure con-
nection of the actuator. Seal the Y2 port
with a blanking plug.
For
double-acting actuators and actua-
tors with air purging
, connect the Y2
port of the adapter block to the signal
pressure connection of the second actua-
tor chamber or spring chamber of the
actuator.
6.2 6.1
6
4
6.3
5
1
2
16
3
3.1
11
18
18.1
13.1
13
17.2
17
17.1
10
3
Exh.
19
20
14
14.1
1.1
1.2
15
1
Lever
1.1 Nut
1.2 Disk spring
2
Follower pin
3
Follower plate
3.1 Follower plate
4
Blanking plug
5
Sealing plug
6
Adapter bracket
6.1 Screws
6.2 Formed seal
6.3 Screws
10
NAMUR con
-
nection block
11
Screw with toothed
lock washer
13
Adapter block
13.1 Screws
14
Bolt
14.1 Screws
15
Formed plate
16
Bracket
17
Turnboard
17.1
Formed seal
17.2
Screws
18
Blank plate
18.1
Screws
19
Air blocker
20
Retaining screw
Fig. 8:
Attachment according to VDI/VDE 3847 to a NAMUR rib
Note
Summary of Contents for 3730-2
Page 19: ...EB 8384 2 EN 19 Design and principle of operation...
Page 109: ...EB 8384 2 EN 109...
Page 110: ...110 EB 8384 2 EN...
Page 111: ...EB 8384 2 EN 111...
Page 112: ...112 EB 8384 2 EN...
Page 113: ...EB 8384 2 EN 113...
Page 114: ...114 EB 8384 2 EN...
Page 115: ...EB 8384 2 EN 115...
Page 116: ...116 EB 8384 2 EN...
Page 117: ...EB 8384 2 EN 117...
Page 118: ...118 EB 8384 2 EN...
Page 119: ...EB 8384 2 EN 119...
Page 120: ...120 EB 8384 2 EN...
Page 121: ...EB 8384 2 EN 121...
Page 122: ...122 EB 8384 2 EN...
Page 123: ...EB 8384 2 EN 123...
Page 124: ...124 EB 8384 2 EN...
Page 125: ...EB 8384 2 EN 125...