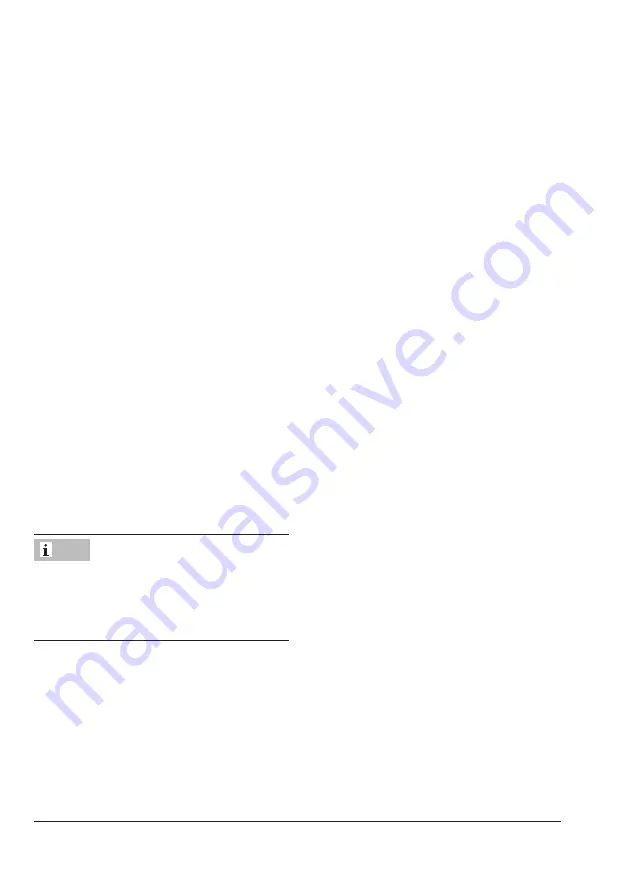
5-2
EB 8048-2 EN
Installation
SAMSON if the valve conditions or states
of the medium process deviate.
Î
Install the valve free of stress and with the
least amount of vibrations as possible.
Read information under “Mounting posi-
tion” and “Versions with V-port plug” in
this section.
Î
Install the valve allowing sufficient space
to remove the actuator and valve or to
perform service and repair work on
them.
Mounting position
Generally, we recommend installing the
valve with the actuator upright and on top of
the valve.
For valves that are intended to be free of
cavities, the control valve
must
be installed
with the actuator on top:
Î
Contact SAMSON if the mounting posi-
tion is not as specified above.
Support or suspension
The plant engineering company is responsi-
ble for selecting and implementing a suitable
support or suspension of the installed control
valve and the pipeline.
Depending on the valve version and mount-
ing position, the valve, actuator and pipeline
must be supported or suspended.
Valves, which are not installed in the pipe-
line in the upright position with the actuator
on top, must be supported or suspended.
Valve accessories
Î
During connection of valve accessories,
make sure that they are easily accessible
and can be operated safely from the
work position.
Vent plugs
Vent plugs are screwed into the exhaust air
ports of pneumatic and electropneumatic de-
vices. They ensure that any exhaust air that
forms can be vented to the atmosphere (to
avoid excess pressure in the device). Further-
more, the vent plugs allow air intake to pre-
vent a vacuum from forming in the device.
Î
Locate the vent plug on the opposite side
to the work position of operating person-
nel.
5.2
Preparation for installation
Before installation, make sure the following
conditions are met:
− The valve is clean.
− The valve and all valve accessories (in-
cluding piping) are not damaged.
− The valve data on the nameplate (type
designation, valve size, material, pres-
sure rating and temperature range)
match the plant conditions (size and
pressure rating of the pipeline, medium
temperature etc.). See the 'Markings on
the device' section for nameplate details.
− The requested or required additional
pipe fittings (see 'Additional fittings' in
the 'Design and principle of operation'
section) have been installed or prepared
as necessary before installing the valve.
Note
Summary of Contents for 3349
Page 6: ...6 EB 8048 2 EN...
Page 15: ...EB 8048 2 EN 1 9 Safety instructions and measures...
Page 16: ...1 10 EB 8048 2 EN...
Page 34: ...4 6 EB 8048 2 EN...
Page 44: ...5 10 EB 8048 2 EN Installation...
Page 52: ...8 4 EB 8048 2 EN...
Page 66: ...9 14 EB 8048 2 EN...
Page 72: ...12 2 EB 8048 2 EN...
Page 74: ...13 2 EB 8048 2 EN...
Page 92: ...14 18 EB 8048 2 EN...
Page 100: ...15 8 EB 8048 2 EN...
Page 101: ......
Page 102: ......
Page 103: ......