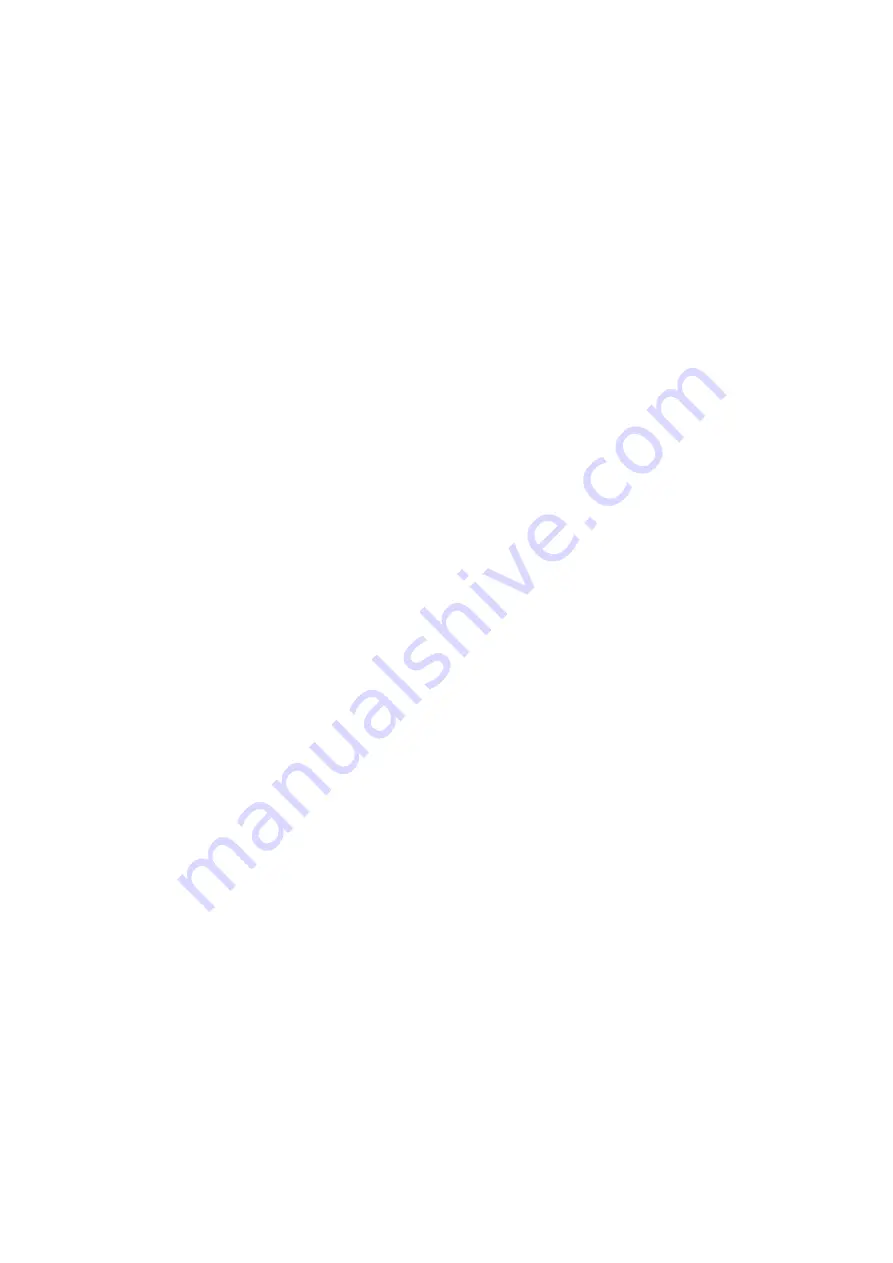
- 50 -
- 51 -
Service and maintenance
Safety
Installations and adjustments may be carried out only by a person with the required skills and
qualifications and the necessary knowledge of the machine in question.
Installations and adjustments as well as repairs must be carried out when the engine
is stopped and the key removed from the ignition. Moving parts must be in balance and
stopped,and when necessary, locked.
For example, the crane and harvester head may move or slide on their own over time.
Make sure that there is no stored pressure in the fluid systems before you open mechani-
cal or hydraulic joints (pressurized oil tank, harvester head pressure battery, AC equipment,
radiator etc.)
Make sure there is no danger of injuries if you need to start the engine while performing main-
tenance and also after maintenance work.
Ensure that all periodic maintenance work and cleaning are performed on schedule in accor-
dance with the instructions. This reduces the risk of danger caused by malfunctions.
Proper maintenance and service guarantee a long working life and the validity of the warranty.
General instructions:
·
Make sure you are sufficiently qualified before you perform maintenance tasks. If you are
not sure, have the work performed by a qualified individual.
·
Familiarize yourself with the structure of the harvester and the maintenance instructions
before you start the maintenance work.
· Wear protective clothing suitable for the work
· Use appropriate tools and other equipment.
·
Handle the machine to be maintained and the substances used as instructed so that there is
no danger to yourself, other people or the environment.
Summary of Contents for HR46
Page 2: ......
Page 14: ... 14 Certificate on conformity to the EU directives ...
Page 29: ... 29 13a ...
Page 71: ... 71 Electric diagram ...
Page 72: ... 72 ...
Page 73: ... 73 ...
Page 74: ... 74 ...
Page 75: ... 75 ...
Page 76: ... 76 ...
Page 77: ... 77 ...
Page 78: ... 78 ...
Page 79: ... 79 ...
Page 80: ... 80 ...
Page 81: ... 81 ...
Page 82: ... 82 ...
Page 83: ... 83 ...
Page 84: ... 84 ...
Page 85: ... 85 ...
Page 86: ... 86 ...
Page 87: ... 87 ...
Page 88: ... 88 ...
Page 89: ... 89 ...
Page 90: ... 90 ...
Page 91: ... 91 ...
Page 92: ... 92 ...
Page 93: ... 93 ...
Page 94: ... 94 ...