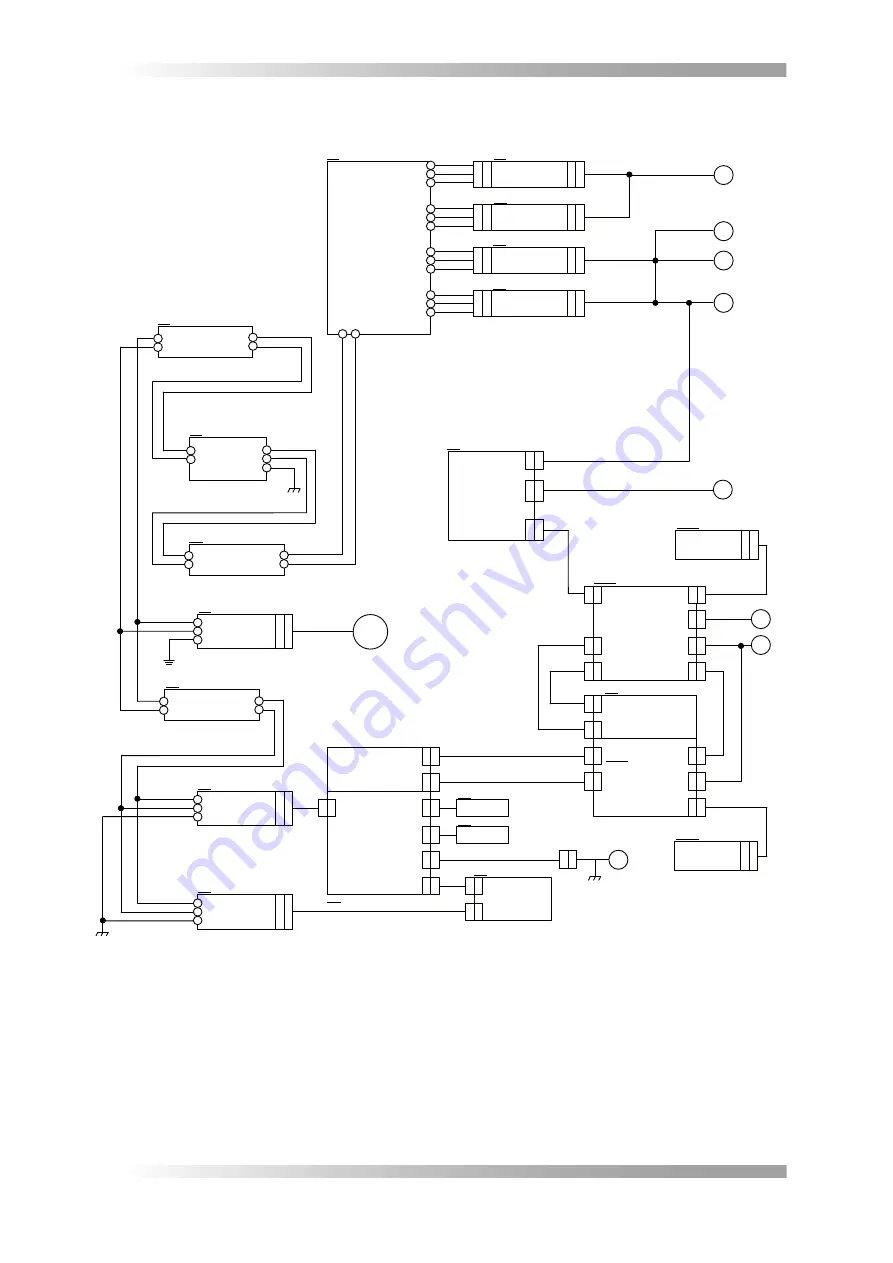
II-
18
BF-Sirius
Maintenance Manual
2.4 Electrical Connection Diagram
IMAGE PROCESSING BOARD
(SLAVE)
SJPB1GA00-04
CN4**
PC
SJPC9P003-02
FRAME GRABBER BOARD
IPM-8580-CL-F
IMAGE PROCESSING BOARD
(MASTER)
SJPB1GA00-04
CN4**
EXTENSION BOARD
SJPB1HA00-03
CN5**
LCD MONITOR
S1921-SH
DC POWER SUPPLY
LEB150F-0524-SN
DC POWER SUPPLY
LEP240F-24-SN
DC POWER SUPPLY
LEA50F-5-SNY
DC POWER SUPPLY
LEA50F-12-SN
TERMINAL BLOCK
BC1S-4Q × 4
BC1S-4QPE × 1
AC OUTLET 2
WTN-1170A
AC OUTLET 1
WTN-1170A
MOUSE
KEYBOARD
NOISE FILTER
RSEN-2020
EARTH LEAKAGE BREAKER
NV30-FAU-2P-10A-240V-30mA
AC INLET
WTN-1171R1A
SJ24EH001
SJ24EH002
SJ24EH065
SJ24EH063
SJ24EH064
SJ24EH066
SJ24EH063
SJ24EH064
SJ24EH066
SJ24EH004
SJ24EH004
SJ24EH005
MAIN BREAKER
TM-1-8291/E/SVB-SW
SJ24EH006
SJ24EH006
SJ24EH007
SJ24EH007
SJ24EH009
SJ24EH010
SJ24EH011
SJ24EH012
SJ24EH013
SJ24EH013
SJ24EH014
SJ24EH014
SJ24EH009
SJ24EH009
SJ24EH010
SJ24EH010
SJ24EH011
SJ24EH011
SJ24EH012
SJ24EH012
SJ00PE005
SJ00PE005
SJ24EH043
SJ24EH044
SJ24EH045
SJ24EH046
SJ24EH045
ACLC-M26-
MOLD-00.23
ACLC-M26-
MOLD-00.23
SJ24EH062
C
N
4
02
C
N
40
4
C
N
40
3
C
N
4
01
C
N
4
07
C
N
4
10
C
N
4
09
C
N
5
02
C
N
5
03
C
N
41
0
C
N
40
9
C
N
40
8
C
N
4
01
C
N
40
2
D
S
U
B
ACLC-M26-MOLD-02.5
ACLC-M26-MOLD-02.5
C06-09M-09F-906
~
100-120V
200-240V
50/60Hz
E
L
N
E
L
N
E
L
N
L
N
L
N
L
N
E
L
N
L
N
L
N
L
N
E
L
N
E
L
N
E
L
N
E
L
N
LED DRIVER
BOARD 5 SIRIUS
SJPB2RA00-01
CN1**
C
N
10
1
C
N
10
2
C
N
1
03
ULJP-C-ULJPSS-2
FG
EC01
EC02
EC04
EC05
EC06
BK01
NF01
FG
SW01
TB01
PS01
PS02
PS03
PS04
PB23
PB19-01
PB19-02
PB20
FG
EC03
PC00
A
B
C
E
D
CCD BOARD N
SJPB2AA00-03
CN6**
C
N
60
1
PB21-02
CCD BOARD N
SJPB2AA00-03
CN6**
C
N
60
1
PB21-01
F
H
G
PE
CIRCUIT PROTECTOR
NC1V-2100-10AA
L
N
L
N
CP03
Electrical Connection Diagram1
FFFure
2-
8
Summary of Contents for BF-Sirius
Page 1: ... SJ241DCM1 02E BF Sirius Manual ...
Page 7: ...I 1 BF Sirius Operation Manual Operation Manual ...
Page 37: ...II 1 BF Sirius Maintenance Manual Maintenance Manual ...
Page 61: ...BF Sirius Installation Manual III 1 Installation Manual ...
Page 65: ...BF Sirius Specification Customer Support IV 1 Specification Customer Support ...