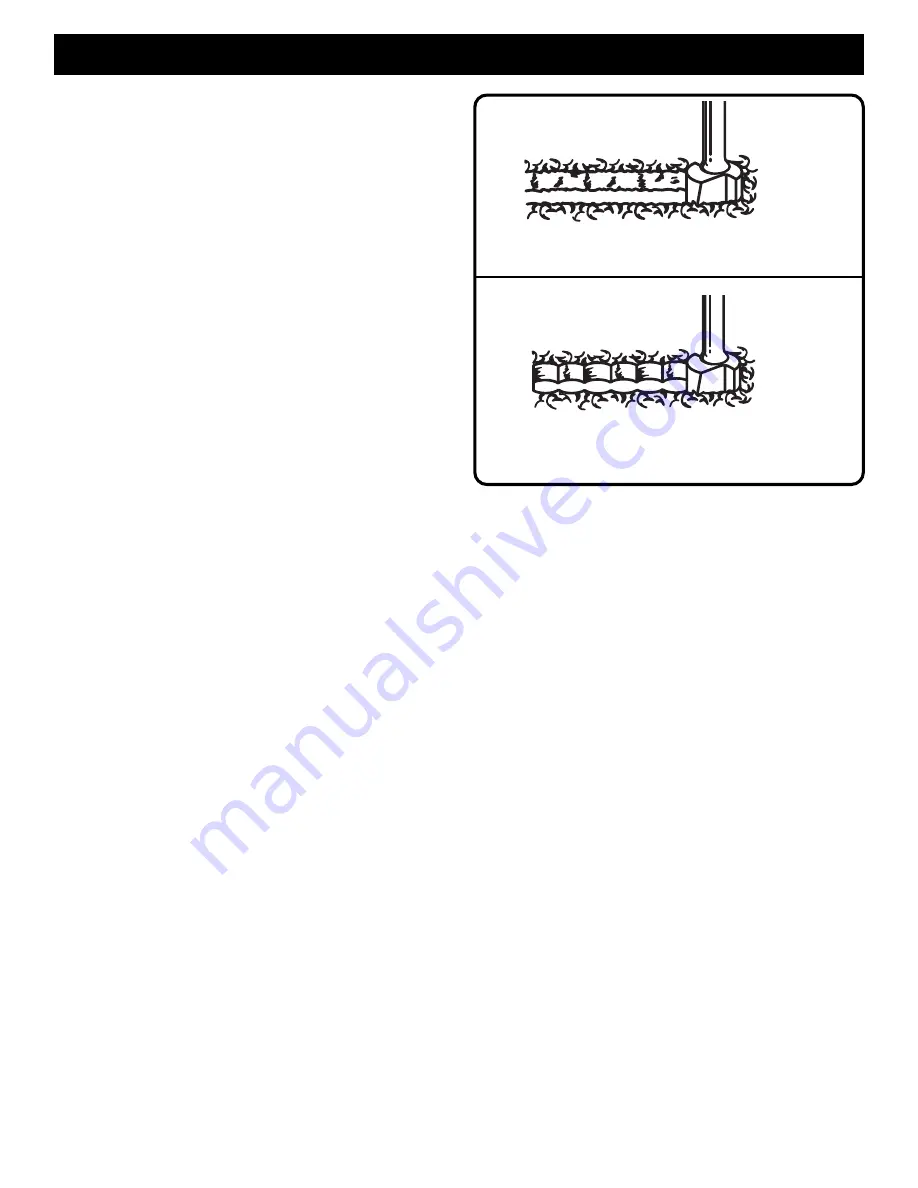
16
OPERATION
RATE OF FEED
The proper rate of feed depends on several factors: the
hardness and moisture content of the wood, the depth of
cut, and the cutting diameter of the bit. When cutting
shallow grooves in soft woods such as pine, a faster rate
of feed can be used. When making deep cuts in
hardwoods such as oak, a slower rate of feed should be
used.
The best rate of feed is one that does not slow down the
router motor more than one-third of its no-load speed. If
the router is fed too fast, it will take large chips out of the
wood and leave gouge marks. If the router is fed too slow,
it will scorch or burn the wood.
Feeding Too Fast
See Figure 17.
Clean, smooth routing and edge shaping can be done
only when the bit is revolving at a relatively high speed
and is taking very small bites to produce tiny, cleanly
severed chips. If your router is forced to move forward too
fast, the RPM of the bit becomes slower than normal in
relation to its forward movement. As a result, the bit must
take bigger bites as it revolves. “Bigger bites” mean
bigger chips, and a rougher finish. Bigger chips also
require more power, which could result in the router
motor becoming overloaded.
Under extreme force-feeding conditions the relative RPM
of the bit can become so slow—and the bites it has to
take so large — that chips will be partially knocked off
(rather than fully cut off), resulting in splintering and
gouging of the workpiece.
Your router is an extremely high-speed tool (15,000 -
25,000 RPM no-load speed), and will make clean,
smooth cuts if allowed to run freely without the overload
of a forced (too fast) feed. Three things that cause “force
feeding” are bit size, depth-of-cut, and workpiece
characteristics. The larger the bit or the deeper the cut,
the more slowly the router should be advanced. If the
wood is very hard, knotty, gummy or damp, the operation
must be slowed still more.
You can always detect “force feeding” by the sound of the
motor. Its high-pitched whine will sound lower and
stronger as it loses speed. Also, the strain of holding the
tool will be noticeably increased.
Fig. 18
TOO FAST
TOO SLOW
Feeding Too Slow
See Figure 18.
It is also possible to spoil a cut by moving the router
forward too slowly. When it is advanced into the work too
slowly, a revolving bit does not dig into new wood fast
enough to take a bite; instead, it simply scrapes away
sawdust-like particles. Scraping produces heat, which can
glaze, burn, or mar the cut and in extreme cases, can
even overheat the bit so as to destroy its hardness.
In addition, it is more difficult to control a router when the
bit is scraping instead of cutting. With practically no load
on the motor the bit will be revolving at close to top RPM,
and will have a much greater than normal tendency to
bounce off the sides of the cut (especially if the wood has
a pronounced grain with hard and soft areas). As a result,
the cut produced may have rippled, instead of straight
sides.
“Too-slow feeding” can also cause your router to take off
in a wrong direction from the intended line of cut.
Always
grasp and hold your router firmly with both hands
when routing.
You can detect “too-slow feeding” by the runaway, high-
pitched sound of the motor; or by feeling the “wiggle” of
the bit in the cut.
Fig. 17
Summary of Contents for R181D
Page 23: ...23 NOTES...