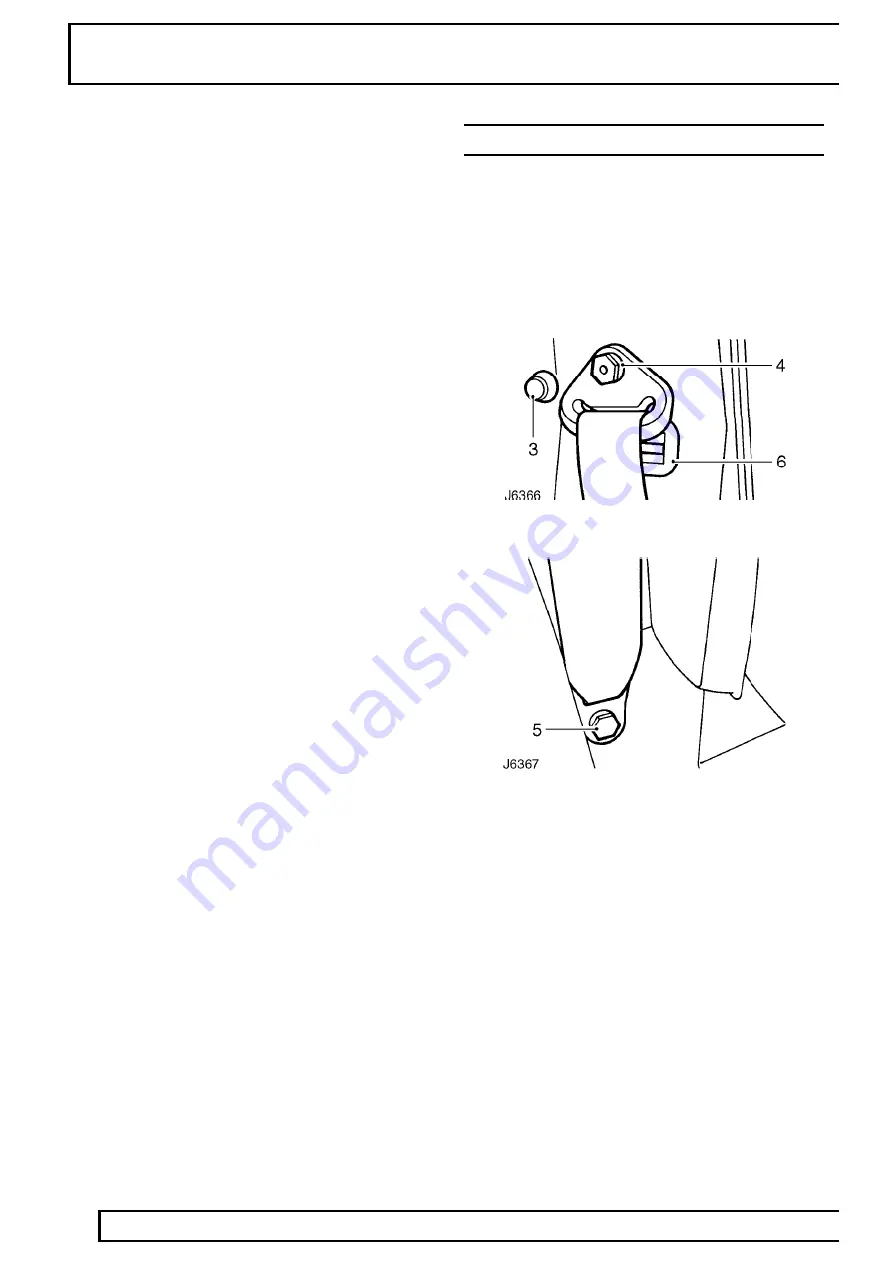
76
CHASSIS AND BODY
22
REPAIR
Refit
9. Fit new spring clips to the 3 brackets on top
edge of side trim panel.
10. Align trim panel, ensuring it is correctly
positioned around side window.
11. Locate trim panel spring clips on inner cant rail
and press firmly down to secure top edge of trim
panel.
12. Align bosses of trim panel with body side fixing
holes and secure with 4 bolts and washers. Do
not fully tighten at this stage.
13. Fit trim stud to secure bottom edge of trim panel
to ’B’ post.
14. Secure seat belt guide to ’B’ post, tighten bolt to
32 Nm (24 lbf/ft) and fit cap.
15. Fit rear end trim panel
See Rear end trim
panel .
16. Fit rear seat squab
See Rear seat squab .
SIDE TRIM PANEL - 110 STATION WAGON
Service repair no - 76.13.70
Remove
1. Remove rear inward facing seats
See Rear
seat squab - 90 , or See Rear bench seat .
2. Remove rear end trim panel
See Rear end
trim panel .
3. Prise finisher cap from rear seat belt upper guide
bracket retaining bolt.
4. Unscrew bolt and remove guide bracket from ’C’
post.
5. Remove bolt securing seat belt to wheel arch
mounting.
6. Prise trim panel cap fastener from ’C’ post.
7. Remove seat belt aperture finisher from side trim
panel.
8. Remove screw and release seat belt clip from ’C’
post.
Summary of Contents for DEFENDER 300Tdi
Page 310: ...76 CHASSIS AND BODY 2 DESCRIPTION AND OPERATION LAND ROVER 90...
Page 312: ...76 CHASSIS AND BODY 4 DESCRIPTION AND OPERATION LAND ROVER 110...
Page 314: ...76 CHASSIS AND BODY 6 DESCRIPTION AND OPERATION LAND ROVER 130...
Page 317: ...CHASSIS AND BODY 1 REPAIR DOORS RH rear door lock mechanism RH front door lock mechanism...
Page 415: ...86 ELECTRICAL 8 DESCRIPTION AND OPERATION...