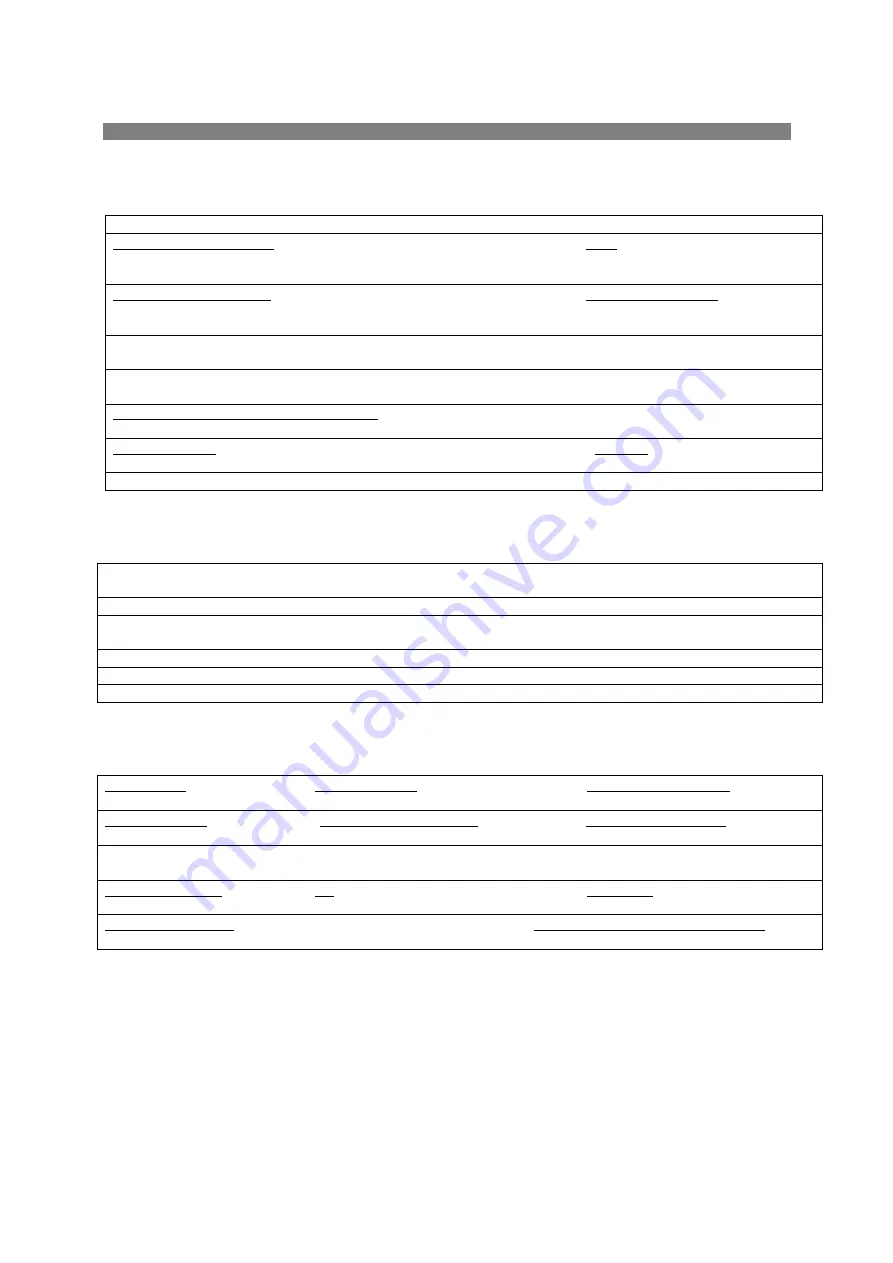
Material Data Safety Sheets
8-6
HP6A Manual
SECTION I
Product name or number (as it appears on label)
Date
ROTTLER Coolant
October, 1999
Manufacturer’s Name
Emergency Phone #
Yuma Industries Incorporated
YUMA 317-398-9862
CHEMTREC
800-424-9300
Address (Number, Street, City, State, & Zip Code
783 W. Mausoleum Road, Shelbyville, IN 46176-9720
Hazardous material description, proper shipping name, haz. class, haz. ID#
None
Additional hazard classes (as applicable)
None
Chemical family
Formula
Water miscible cutting and grinding fluid concentrate
See Section II
SECTION II - INGREDIENTS
CAS Registry #
Wt%
Chemical Name(s)
Listed as a carcinogen in
NTP, IARC, or OSHA1910(z) (specify)
102-71-6
1-9
Triethanolamine
ACGIH(TLV): TWA=5mg/m3,
Not listed
Balance classified as non-hazardous Ingredients
SECTION III – PHYSICAL DATA
Boiling Point
Specific Gravity
Odor Threshold (ppm)
Not available
(H2O=1) @ 20
°
C 1.02
Not available
Vapor Pressure
Percent Volatile (Vol. %)
Percent Solid (Wt. %)
Not available
Not available
Not available
Vapor Density
Evaporation Rate
Freezing Point (
°
C)
Not available
Not available
Not available
Solubility in Water
pH
Material is
100%
(4%) 9.6
Liquid
Appearance & Odor
Volatile Organic Compounds (VOC)
Yellow with mild odor
Not available
Summary of Contents for HP6A
Page 2: ......
Page 14: ...Introduction Safety Installation 1 7 HP6A Manual Single Phase Electrical Hook up...
Page 23: ...Control Definition 2 9 HP6A Manual Control Illustration...
Page 24: ...Control Definition 2 10 HP6A Manual Control Panel Illustration...
Page 38: ...Maintenance 4 3 HP6A Manual Lubrication Illustration...
Page 41: ...Maintenance 4 6 HP6A Manual Bleeding Illustration...
Page 75: ...Machine Parts 6 1 P6A Manual Chapter 6 Machine Parts Front Right Side View HP6A...
Page 76: ...Machine Parts 6 2 P6A Manual Electrical Wiring Diagram Part 1 Wiring Diagram 514 2 97K...
Page 77: ...Machine Parts 6 3 P6A Manual Electrical Wiring Diagram Part 2...
Page 78: ...Machine Parts 6 4 P6A Manual Electrical Wiring Diagram Part 3...
Page 79: ...Machine Parts 6 5 P6A Manual Air Logic Diagram...
Page 80: ...Machine Parts 6 6 P6A Manual Air System Connections...
Page 81: ...Machine Parts 6 7 P6A Manual Hydraulic Logic Diagram...
Page 82: ...Machine Parts 6 8 P6A Manual Hydraulic System Connections...
Page 83: ...Machine Parts 6 9 P6A Manual Injection Oiler...
Page 84: ...Machine Parts 6 10 P6A Manual Electrical Power Supply Enclosure...
Page 85: ...Machine Parts 6 11 P6A Manual Control Panel...
Page 86: ...Machine Parts 6 12 P6A Manual Carriage...
Page 87: ...Machine Parts 6 13 P6A Manual Front Section Rocker Arm...
Page 88: ...Machine Parts 6 14 P6A Manual Drive Pinion Assembly...
Page 89: ...Machine Parts 6 15 P6A Manual Gear Housing Section...
Page 90: ...Machine Parts 6 16 P6A Manual Carriage Float Clamp...
Page 91: ...Machine Parts 6 17 P6A Manual Stroking Control Air...
Page 92: ...Machine Parts 6 18 P6A Manual Ratchet Actuator Assembly...
Page 93: ...Machine Parts 6 19 P6A Manual Stroking Cylinder...
Page 94: ...Machine Parts 6 20 P6A Manual Upper Limit Assembly...
Page 95: ...Machine Parts 6 21 P6A Manual Hydraulic Cylinder...
Page 96: ...Machine Parts 6 22 P6A Manual Motor Safety Switch...
Page 97: ...Machine Parts 6 23 P6A Manual Pneumatic Power Supply...
Page 98: ...Machine Parts 6 24 P6A Manual Splash Tank Coolant System...
Page 99: ...Machine Parts 6 25 P6A Manual Block Hold Down Fixture Assembly...
Page 101: ...Optional Tooling 7 2 HP6A Manual Precision Hone Head...
Page 102: ...Optional Tooling 7 3 HP6A Manual Stone Holder Sleeve Sets...
Page 108: ...Optional Tooling 7 9 HP6A Manual Disassembly Instructions...
Page 109: ...Optional Tooling 7 10 HP6A Manual Junior Precision Hone Head...
Page 110: ...Optional Tooling 7 11 HP6A Manual 514 9D Extra Large HD Hone Head Assembly...
Page 111: ...Optional Tooling 7 12 HP6A Manual 514 9D Extra Large HD Hone Head Assembly Parts List...
Page 112: ...Optional Tooling 7 13 HP6A Manual 514 9 4D Sleeve Assembly...
Page 113: ...Optional Tooling 7 14 HP6A Manual 514 9 5T Stone Holder Set...
Page 114: ...Optional Tooling 7 15 HP6A Manual Auxiliary Sump Tank...
Page 115: ...Optional Tooling 7 16 HP6A Manual V 71 Fixture...
Page 116: ...Optional Tooling 7 17 HP6A Manual Stone Depth Assembly...
Page 118: ...Optional Tooling 7 19 HP6A Manual Block Hold Down Clamp Assembly...
Page 119: ...Optional Tooling 7 20 HP6A Manual 514 7B CYLINDER SLEEVE FIXTURE...
Page 120: ...Optional Tooling 7 21 HP6A Manual 514 2 39S Optional Filter System...
Page 136: ...Material Data Safety Sheets 8 16 HP6A Manual MOBIL DTE OIL LIGHT...
Page 137: ...Material Data Safety Sheets 8 17 HP6A Manual...
Page 138: ...Material Data Safety Sheets 8 18 HP6A Manual...
Page 139: ...Material Data Safety Sheets 8 19 HP6A Manual...
Page 140: ...Material Data Safety Sheets 8 20 HP6A Manual...
Page 146: ...Material Data Safety Sheets 8 26 HP6A Manual Unoba EP Grease...
Page 147: ...Material Data Safety Sheets 8 27 HP6A Manual...
Page 148: ...Material Data Safety Sheets 8 28 HP6A Manual...
Page 149: ...Material Data Safety Sheets 8 29 HP6A Manual...
Page 150: ...Material Data Safety Sheets 8 30 HP6A Manual...