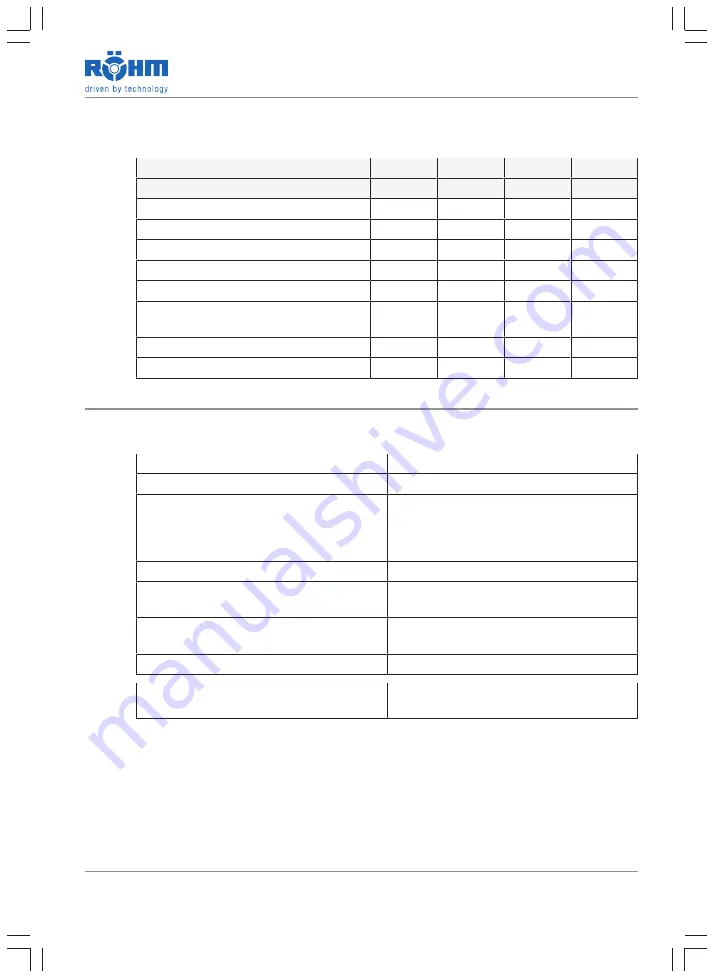
Product Description | 3
KZS-H_KZS-HG
19 / 44
KZS-HG, large jaw stroke, base jaws with serration 1.5 x 60° and
cross tenon
ID no.
181485
181489
181493
181497
ID no. with inductive sensors
181585
181589
181593
181597
Size
100
160
200
250
Jaw stroke [mm]
7.0
9.6
12.1
17.6
Max. actuation pressure [bar]
120
120
60
60
Max. total clamping force [kN]
16
40
50
50
Weight [kg]
4.65
13.5
22.9
35.2
Cylinder volume (double stroke)
[cm]
3
30
100
300
420
Closing time [s]
1.1
1.6
2.1
3.0
Repetitive clamping accuracy [mm] 0.01
0.02
0.03
0.03
3.2.2
Conditions of Use and Environmental Conditions
The centric clamp is designed for the following environmental and operating
conditions:
Ambient medium
Air and non-aggressive gases
Place of use
Interior
Relative humidity (at + 50 °C)
< 100 %
Use in very humid conditions leads to
faster corrosion and may reduce the
useful life
Potentially explosive environments
No
Ambient temperature at place of oper-
ation
+ 10 °C to + 60 °C
Ambient temperature for storage
- 15 °C to + 60 °C
For 24 hours also at + 70 °C
Dry and wet machining
Wet machining permissible
Quality of the hydraulic oil
ISO 4406:2017,
Number key 20:18:15
Pollution of the environment caused by the machine itself is permitted. How-
ever, perfect operation of the centric clamp must be ensured and checked
regularly. The centric clamp must also be cleaned of coarse dirt with a broom
or brush. Cleaning with compressed air is not permitted.
Summary of Contents for KZS-H
Page 2: ......