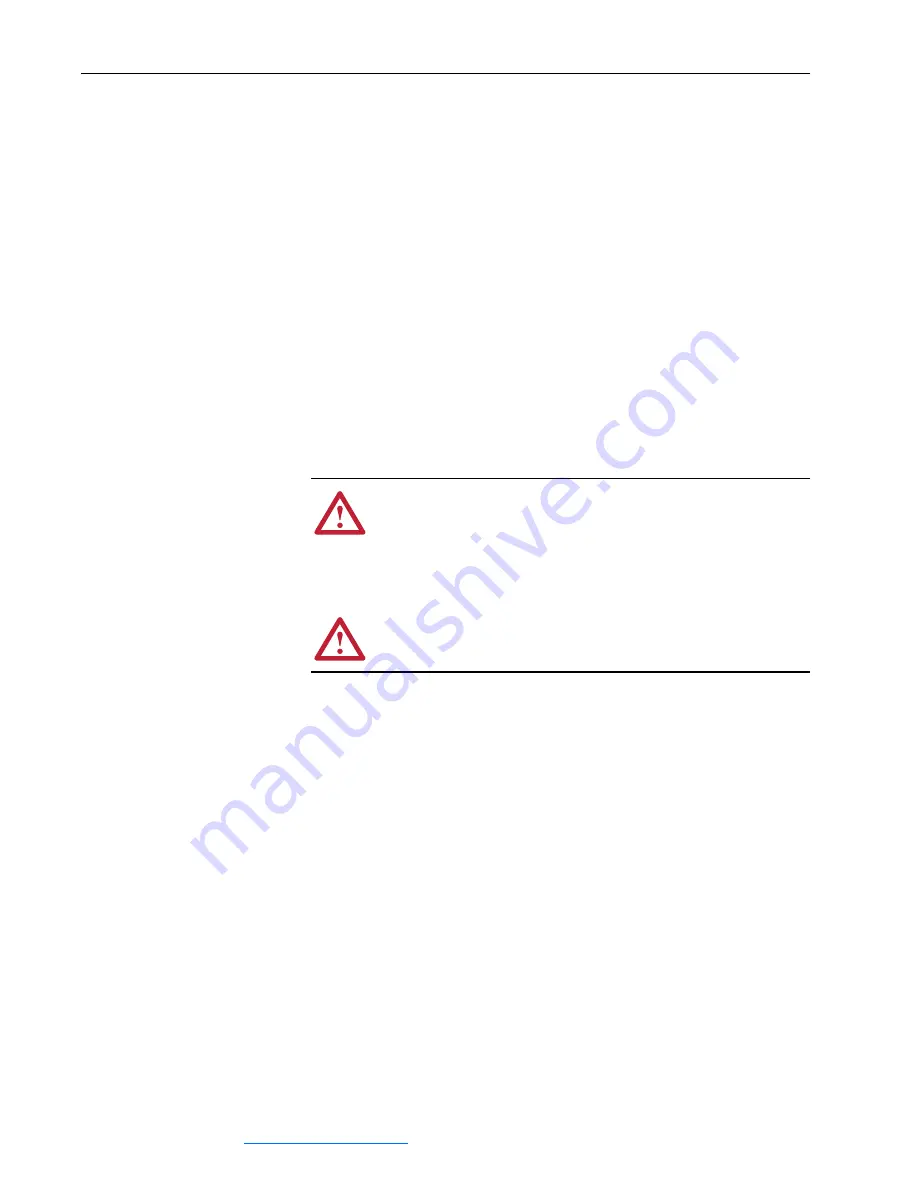
PowerFlex Digital DC Drive User Manual -
Publication 20P-UM001C-EN-P - July 2008
2-10
Drive Start Up
17. Access the “Digital Outputs” group and configure the following
parameters:
❏
If a contactor and a dynamic brake resistor is used:
❍
Par 629 [Relay Out 2 Sel] = 24 “ContactorDB”.
❏
If a neither a contactor and a dynamic brake resistor is used:
❍
Par 629 [Relay Out 2 Sel] = Set to other than 24
“ContactorDB” or 25 “Contactor” (e.g., 0 “Not Used”).
❍
Par 1392 [Relay Out 1 Sel] = Set to other than 24
“ContactorDB” or 25 “Contactor” (e.g., 0 “Not Used”).
18. If you are using the HIM on the drive cover (Port 1) for the speed
reference, access the “DPI Inputs” group and set the appropriate
[DPI Px Select] parameter to 1“Speed Ref A”.
8.
Tune the Current Regulator:
Complete this test before running the drive for the first time. Upon
completing this tuning procedure, the armature resistance value is
stored in Par 453 [Arm Resistance] and the armature inductance value is
stored in Par 454 [Arm Inductance]. If needed, these values can be
manually adjusted.
1. If an external supply is used to power the motor field, disconnect
the wires from the motor field terminals. If the drive supplies power
to the motor field, the internal field circuit will automatically be
disabled during this test.
Important: The drive must be under at least a 40% load in order to
properly tune the current regulator. Verify that the motor
does not start rotating during the Current Regulator tuning
test (due to remnant magnetization, field series, etc.). If
necessary, mechanically block the motor shaft so it does
not turn.
!
ATTENTION: Prior to tuning the current regulator, you must
provide a hard wired maintained external operator accessible
coast/stop push button to disable the machine in case of improper
operation. Uncontrolled machine operation can result if this is
not done. Failure to observe this precaution could result in severe
bodily injury or loss of life.
!
ATTENTION: Prior to tuning the current regulator, uncouple
the motor from equipment or processes that may be damaged by
incorrect rotation of the motor or speed references.