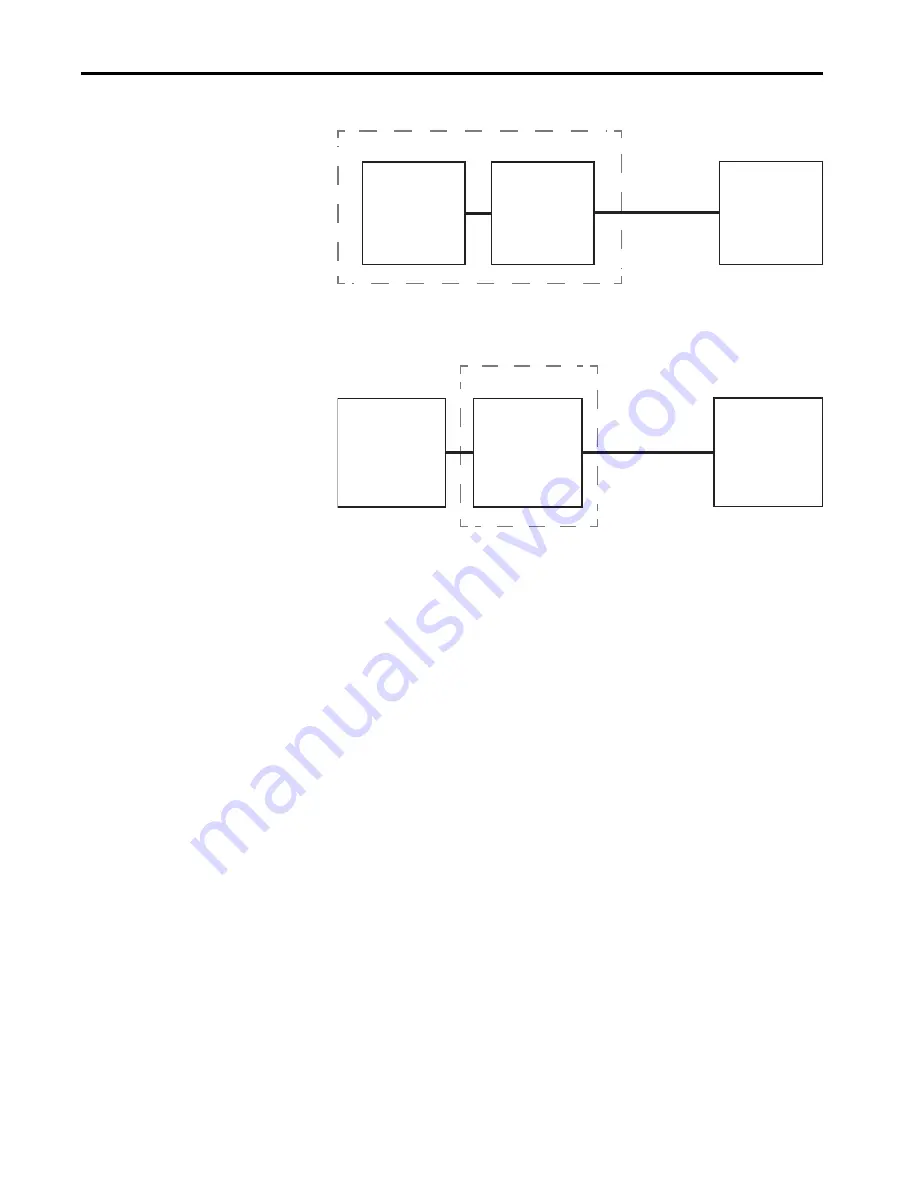
20
Rockwell Automation Publication 442G-UM002A-EN-P - December 2016
Chapter 2
Safety Concept
Figure 14 - Emergency Stop Function
The following applies to modules with a connection for an enabling switch.
Figure 15 - Enabling Switch Function
The access box must be installed in accordance with the applicable regulation
and standards.
While the access box can be used for PLe and Category 4 applications, the
installer must comply with guard requirements (for example, EN/ISO
13854
and EN/ISO 13857) and in some cases also minimum (safe) distance
requirements (for example, EN/ISO 13855).
The installed system, including the safety control system and the means by
which the machine stops, must achieve the needed safety performance. The
access box is one element in the safety system.
Before safety components are used, a risk assessment must be performed on the
machine in accordance with:
• EN ISO 12100, Safety of machinery – Basic concepts - General
principles for design - Risk assessment and risk reduction.
• EN ISO 13849-1, Safety of machinery. Safety related parts of control
systems. General principles for design, Annex B
• IEC 62061, Safety of Machinery – Functional safety of safety-related
electrical, electronic, and programmable electronic control systems.
Correct use includes compliance with the relevant requirements for
installation and operation, in particular:
• EN ISO 13849-1, Safety of machinery. Safety related parts of control
systems. General principles for design
• EN ISO 14119, Safety of machinery. Interlocking modules that are
associated with guards. Principles for design and selection
Access Box
B10d
(Emergency stop)
PFHd
(internal evaluation
of the emergency
stop)
PFHd
(Safety controller)
Input Signal
(EStop)
Guard Locking Module
B10d
(Enabling switch)
PFHd
(internal evaluation
of the emergency
stop)
PFHd
(Safety controller)
Input signal
(EnablingSwitch)