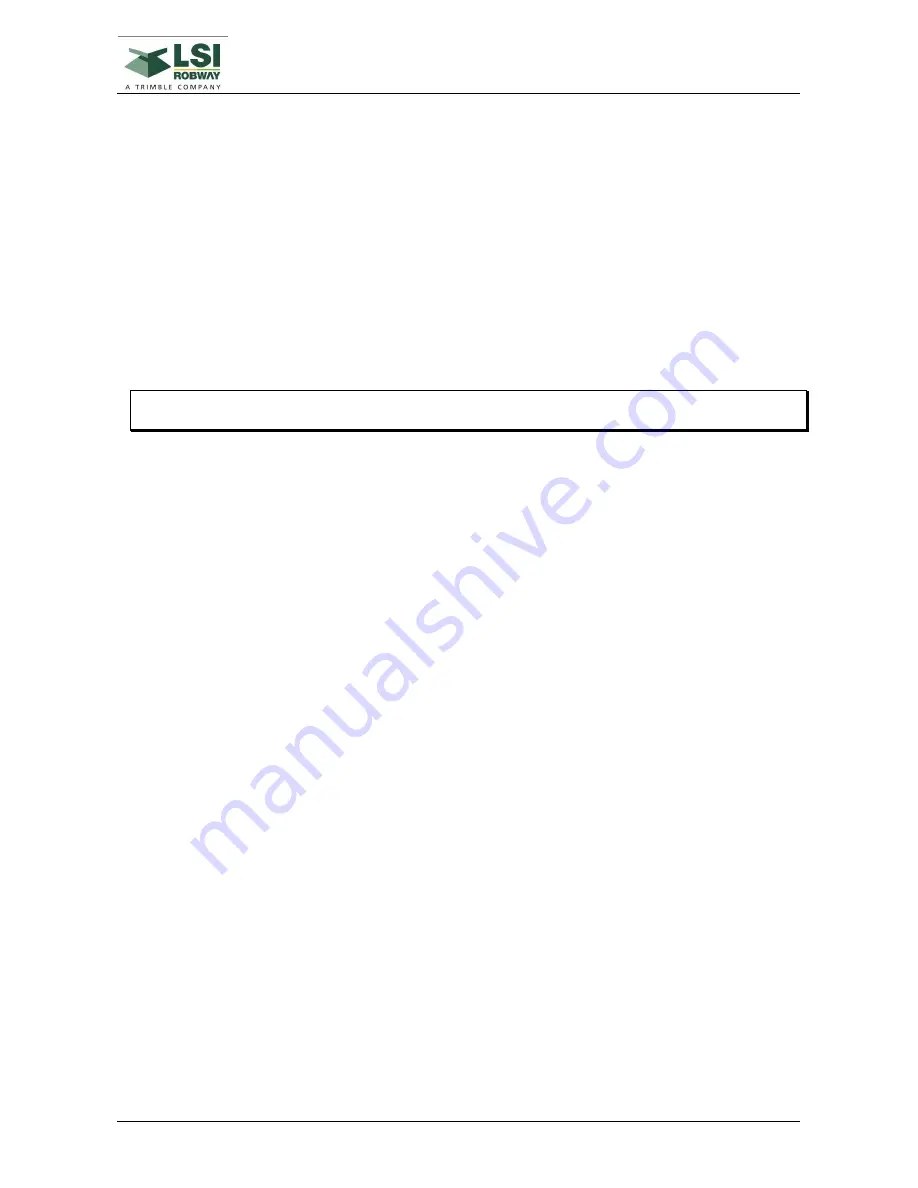
OPERATION AND INSTALLATION
RCI-4100 SYSTEM
MAN-1111 Rev H
©Copyright 2015 LSI-Robway Pty Ltd
Page 50
•
To exit calibration mode either select F-00 or press the CANCEL key until the F-xx code is
cleared from the screen.
Note:
This procedure is used to change any settings in the function code menu including user
variables such as geometry and alarm settings.
7.2. Tools/Items Required for Calibration:
•
An accurate angle finder for calibrating boom angle sensor,
•
An accurate tape meter (at least 100 ft. long) for verifying radius,
•
Known test weights for calibrating loads,
Software configuration sheets and function codes list can be found in the Attachments.
7.3. Map of Calibration (Suggested Order):
Suggested Order of Calibration
NOTE: Ensure that the function code numbers are checked against the RCI System
Configuration Documents in Attachments
•
Set year, day/month and time.
•
Check / Set the following functions:
o
Amplifier gains and offsets for all sensors.
o
Number of sensor samples to average
o
Metric/Imperial units switching
•
Verify that raw counts stay stable and responding, and remain within 50-4050 for full working
range of all sensors.
•
If Restricted Slew Zone encoder is installed, verify that its raw counts are
incrementing/decrementing when the boom slews right/left.
•
If a wind speed sensor is installed ensure that the anemometer is free to rotate and that a
measurement is present in the display.
•
Review all crane geometry against the supplied Crane Configuration settings for accuracy;
refer to APPENDIX O, for factory default settings. Check each setting and change if required.
•
Review all SWL % parameters against actual requirements and change if required – refer to
APPENDIX O, for factory default settings.
•
Review the data logger recording points against actual requirements and change if required –
refer to APPENDIX O, for factory default settings. Check each setting and change if required.
•
Calibrate low and high boom angle.
•
Calibrate light and heavy main winch load.
•
Calibrate light and heavy aux. winch load.
•
Perform functional and operational checks and load tests to ensure accuracy of system.
•
If the load readout decreases as the boom is luffed up, apply load/angle correction factor.
•
If required by specific requirement, apply a “winch rigging safe working load” for the main hook
and aux hook.
•
Set the slack rope limits and test the slack rope function.
•
Verify calibration results.
•
Once satisfied with the calibration results, manually record (pen and paper) the calibration
data and all the settings mentioned above.
7.4. Calibration Procedure
Note:
that while in view mode, that is using either "VIEW UNCALIBRATED ..." or "VIEW
CALIBRATED ..." functions, the ENTER key works as a toggle switch to turn that channel ON or OFF.
This function allows the user to temporarily turn a sensor off if it is not needed, e.g. if you want to use
the main winch only on a twin winch system; normally, if you have not connected the auxiliary sensor
up, the RCI-4100 will report an error and activate motion cut. To prevent this you can press the
ENTER key, while in "VIEW UNCALIBRATED TRANSDUCER 2 function", to turn the auxiliary channel
off.
To turn a channel back on, you have to re-enter the same VIEW UNCALIBRATED... function and
press the ENTER key again.
Summary of Contents for RCI-4100
Page 2: ......
Page 6: ......
Page 8: ......
Page 28: ......
Page 36: ......
Page 58: ......
Page 70: ......
Page 82: ......
Page 88: ......
Page 92: ......
Page 94: ......
Page 100: ......
Page 102: ......
Page 104: ......
Page 106: ......
Page 108: ......
Page 110: ......
Page 112: ......
Page 114: ......
Page 126: ......
Page 128: ......
Page 130: ......
Page 132: ......
Page 140: ......
Page 142: ...WIND SPEED MONITORING OPTION MAN 1111 Rev H Copyright 2015 LSI Robway Pty Ltd Page 142 ...
Page 144: ......
Page 147: ...WIND DIRECTION MONITORING MAN 1111 Rev H Copyright 2015 LSI Robway Pty Ltd Page 147 ...
Page 148: ......
Page 150: ......
Page 156: ......
Page 158: ......
Page 162: ...TILT SENSING OPTION MAN 1111 Rev H Copyright 2015 LSI Robway Pty Ltd Page 162 ...
Page 164: ......
Page 170: ......
Page 171: ...SYSTEM DRAWINGS MAN 1111 Rev H Copyright 2015 LSI Robway Pty Ltd Page 171 ...
Page 172: ...SYSTEM DRAWINGS MAN 1111 Rev H Copyright 2015 LSI Robway Pty Ltd Page 172 ...
Page 173: ...SYSTEM DRAWINGS MAN 1111 Rev H Copyright 2015 LSI Robway Pty Ltd Page 173 ...
Page 174: ...SYSTEM DRAWINGS MAN 1111 Rev H Copyright 2015 LSI Robway Pty Ltd Page 174 ...
Page 175: ...SYSTEM DRAWINGS MAN 1111 Rev H Copyright 2015 LSI Robway Pty Ltd Page 175 ...
Page 176: ...SYSTEM DRAWINGS MAN 1111 Rev H Copyright 2015 LSI Robway Pty Ltd Page 176 ...
Page 177: ...SYSTEM DRAWINGS MAN 1111 Rev H Copyright 2015 LSI Robway Pty Ltd Page 177 ...
Page 178: ...SYSTEM DRAWINGS MAN 1111 Rev H Copyright 2015 LSI Robway Pty Ltd Page 178 ...
Page 179: ...SYSTEM DRAWINGS MAN 1111 Rev H Copyright 2015 LSI Robway Pty Ltd Page 179 ...
Page 180: ......
Page 182: ......