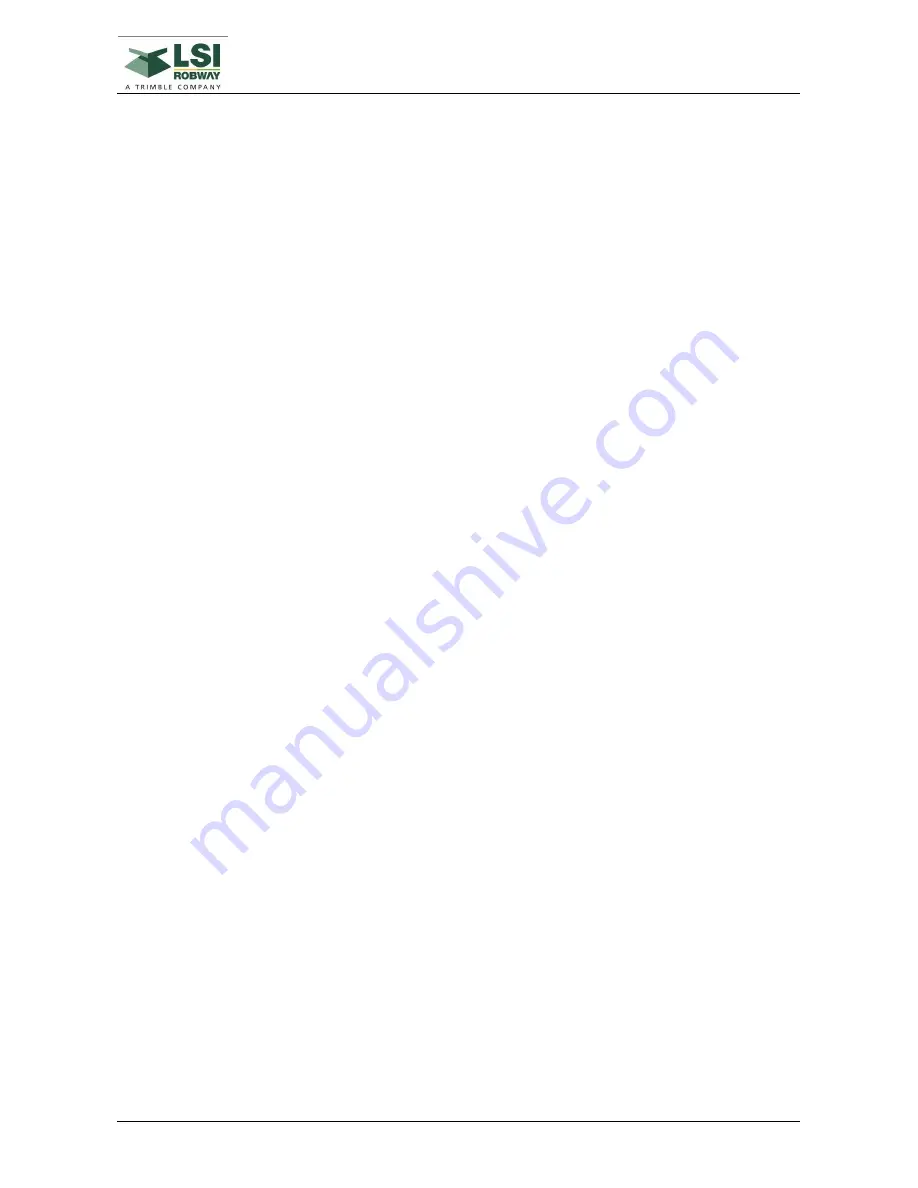
OPERATION AND INSTALLATION
RCI-4100 SYSTEM
MAN-1111 Rev H
©Copyright 2015 LSI-Robway Pty Ltd
Page 46
Similar to the above, select the “Alter Calibration Data” function, and then scroll to the required sensor
and then the calibration data (Lo_r, Lo_c, Hi_r, Hi_c) for this function. But this time, press the ENTER
key again to access the EDIT MODE (i.e. the screen will show “Edit”).
Once “Edit” is displayed on the screen, use the Up/Down arrow keys to change the current value of
the particular calibration code with the recorded values previously copied using the procedure above.
Press the ENTER key to save this new value.
Repeat this procedure for all calibration data values to be restored.
Repeat this procedure for other sensors as required.
6.18. Clear All Calibration Data – USE EXTREME CAUTION!
Activating this function will clear all the calibration data. This must only be used by LSI-Robway-trained
personnel for troubleshooting purposes.
The display will prompt the operator to press ENTER if he wishes to erase the calibration data.
Pressing ENTER here will clean out the memory system and default back to hard coded software. Any
on-site changes made will be lost.
6.19. Main Winch Slack Rope Threshold
This function code is used to set the required load limit or threshold of the main winch for activating a
digital output in the RCI Control Unit. This function may be used to control the crane’s main hoist by
activating “hoist up” when the load on the block is equal to or less than the limit set in this function
code. The factory default setting is normally -0.4t and can be changed to suit specific application.
Please see also Section 7.4.14. “Testing the Slack Rope Function” for details.
6.20. Aux Winch Slack Rope Threshold
This function code is used to set the required load limit or threshold of the aux winch for activating a
digital output in the RCI Control Unit. This function may be used to control the crane’s main hoist by
activating “hoist up” when the load on the block is equal to or less than the limit set in this function
code. The factory default setting is -0.2t and can be changed to suit specific application.
Please see also Section 7.4.14. “Testing the Slack Rope Function” for details.
6.21. User Variables (SWL % Alarms, Motion Cut)
Function codes are used to set the Safe Working Load (SWL) percentages for activating Visual and
Audible Alarms as well as the Motion Cut output function. The factory default values can be changed
to suit specific requirements.
6.22. User Variables (Crane Geometry)
Function codes are used to set the actual physical dimensions (geometry) of the crane.
The factory default values are based on details and information received at the time of order and
supply of system. Any changes to geometry will also require changing of these values on these
function codes.
6.23. User Variables (Data Logging Setup Parameters)
Function codes are user variables relating to the setup parameters of the internal data logger. Please
see APPENDIX F, Data Logging.
6.24. Load / Angle Correction
Load/Angle correction function is designed for use in cases where the displayed load is seen to
increase by a reasonable amount as the boom is luffed down through its operating range. This
phenomenon is particularly apparent when a single sheave dynamometer is used at the boom tip.
Please see Section 7.4.10. “Using Load/Angle Correction Function” for details and procedure.
Summary of Contents for RCI-4100
Page 2: ......
Page 6: ......
Page 8: ......
Page 28: ......
Page 36: ......
Page 58: ......
Page 70: ......
Page 82: ......
Page 88: ......
Page 92: ......
Page 94: ......
Page 100: ......
Page 102: ......
Page 104: ......
Page 106: ......
Page 108: ......
Page 110: ......
Page 112: ......
Page 114: ......
Page 126: ......
Page 128: ......
Page 130: ......
Page 132: ......
Page 140: ......
Page 142: ...WIND SPEED MONITORING OPTION MAN 1111 Rev H Copyright 2015 LSI Robway Pty Ltd Page 142 ...
Page 144: ......
Page 147: ...WIND DIRECTION MONITORING MAN 1111 Rev H Copyright 2015 LSI Robway Pty Ltd Page 147 ...
Page 148: ......
Page 150: ......
Page 156: ......
Page 158: ......
Page 162: ...TILT SENSING OPTION MAN 1111 Rev H Copyright 2015 LSI Robway Pty Ltd Page 162 ...
Page 164: ......
Page 170: ......
Page 171: ...SYSTEM DRAWINGS MAN 1111 Rev H Copyright 2015 LSI Robway Pty Ltd Page 171 ...
Page 172: ...SYSTEM DRAWINGS MAN 1111 Rev H Copyright 2015 LSI Robway Pty Ltd Page 172 ...
Page 173: ...SYSTEM DRAWINGS MAN 1111 Rev H Copyright 2015 LSI Robway Pty Ltd Page 173 ...
Page 174: ...SYSTEM DRAWINGS MAN 1111 Rev H Copyright 2015 LSI Robway Pty Ltd Page 174 ...
Page 175: ...SYSTEM DRAWINGS MAN 1111 Rev H Copyright 2015 LSI Robway Pty Ltd Page 175 ...
Page 176: ...SYSTEM DRAWINGS MAN 1111 Rev H Copyright 2015 LSI Robway Pty Ltd Page 176 ...
Page 177: ...SYSTEM DRAWINGS MAN 1111 Rev H Copyright 2015 LSI Robway Pty Ltd Page 177 ...
Page 178: ...SYSTEM DRAWINGS MAN 1111 Rev H Copyright 2015 LSI Robway Pty Ltd Page 178 ...
Page 179: ...SYSTEM DRAWINGS MAN 1111 Rev H Copyright 2015 LSI Robway Pty Ltd Page 179 ...
Page 180: ......
Page 182: ......