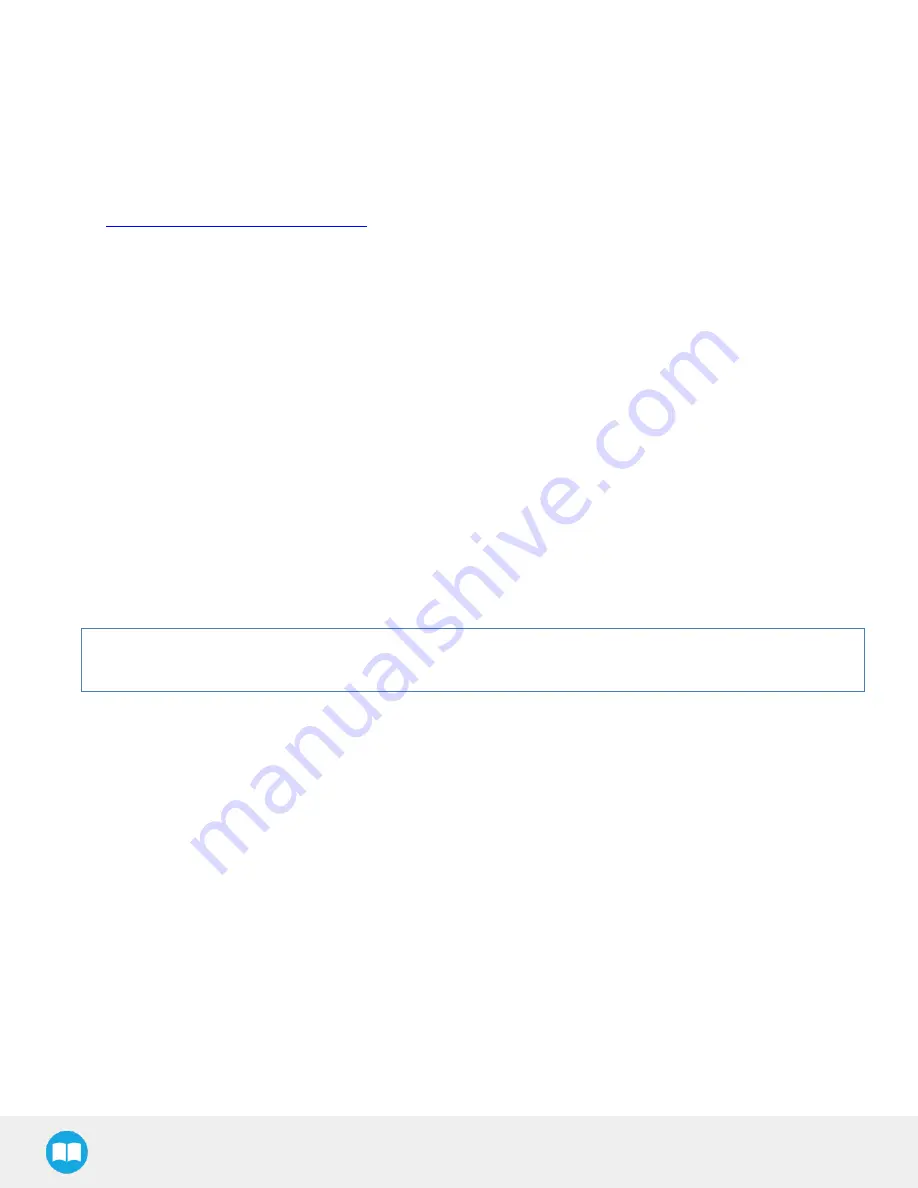
FT 300-SForce Torque Sensor - Instruction Manual
48
8.2. Troubleshooting on other platforms
8.2.1. USBconverter detected as a mouse by Windows
l
In Windows, the USB converter is sometimes detected as a mouse, making the cursor move. This a well know problem in Win-
dows:
http:/ / support.microsoft.com/ kb/ 819036
l
A simple workaround is to plug in the USB converter before powering the Sensor. Once the USB driver is initialized in Windows,
the Sensor can be powered and used without a problem.
8.2.2. Data frequency under 100 Hz in Windows
l
By default, the USB to RS485 converter has a latency setting of 16 ms in Windows (1 ms in Linux), which will prevent the applic-
ation software from receiving new messages at 100 Hz (it will often read two sensor messages in the buffer at the same time).
l
In the Windows Device Manager, right click on the virtual COM port for the Sensor and select Properties. In the Port settings tab,
click on Advanced. Adjust the latency timer to 9 ms (it is not recommended to lower it too much in Windows since other con-
nectivity issues may arise), then click OK.
8.2.3. In Linux, the serial port cannot be opened
l
By default, a user does not have access to the serial ports.
l
It is possible to provide this access by adding the user to the dialout group with the following command:
rd@debian:~/$ sudo usermod -a -G dialout username