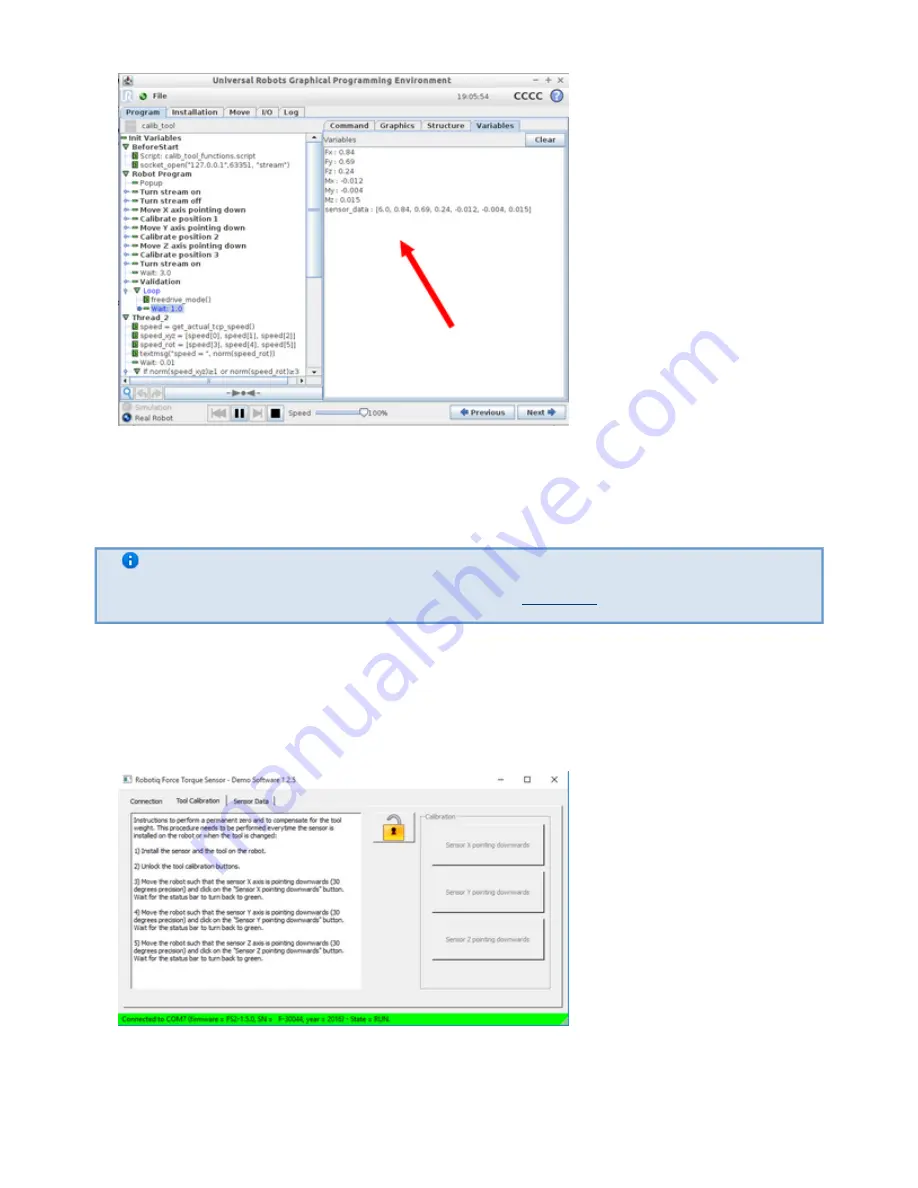
Robotiq FT-150/300 Sensor
Instruction Manual
Robotiq inc. © 2016
21
3.
1.
2.
3.6.2 Calibration procedure for the Visual Demo Software (PC)
Info
You need the Visual Demo Software installed first, see
for download and installation.
To calibrate your FT Sensor :
Go to the "Tool Calibration" tab and follow the instructions.
Once completed, go to the "Sensor Data" tab.