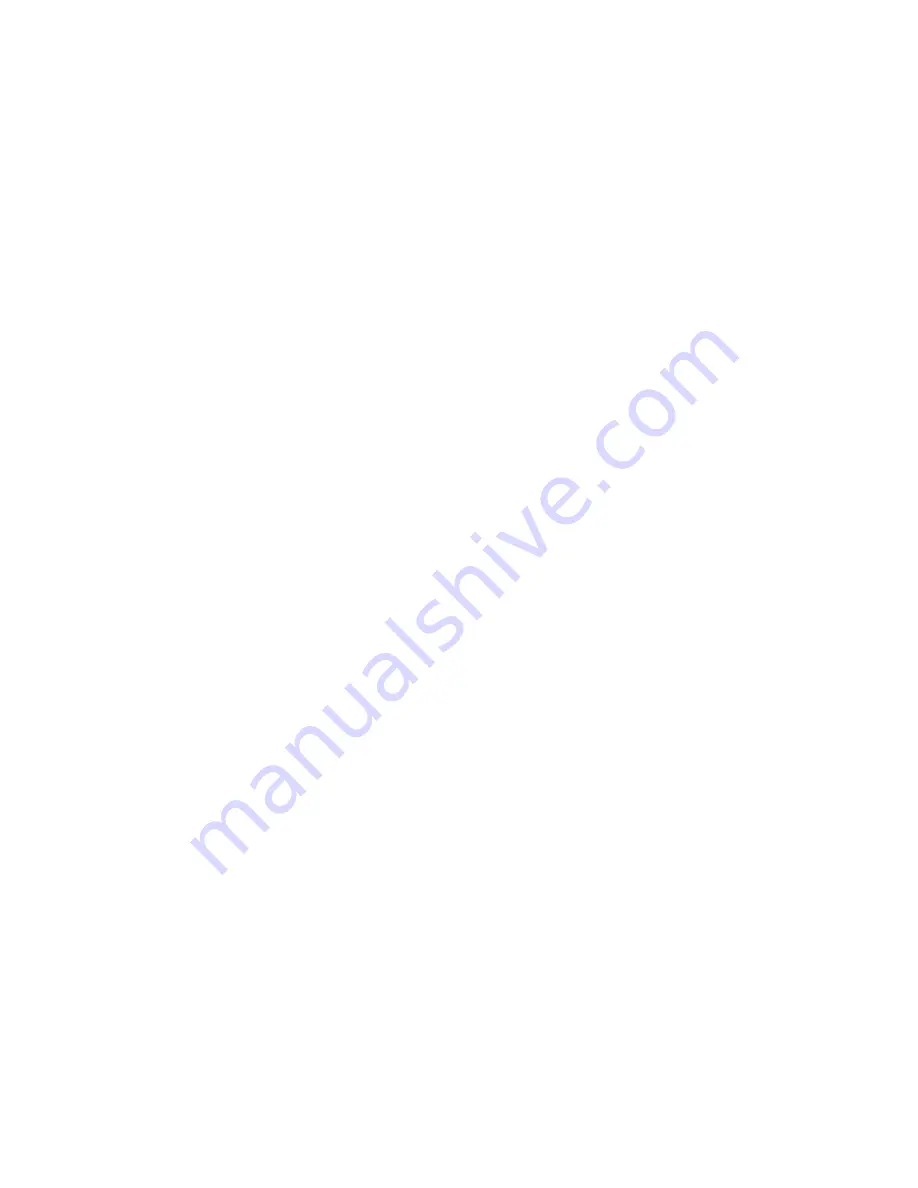
– 80 –
12-4 ENGINE STORAGE
(1) Change the engine oil and perform the daily maintenance items above mentioned.
(2) Drain fuel from carburetor float chamber.
(3) To prevent rust in the cylinder bore, apply oil through the spark plug hole and turn the crankshaft several
turns by hand. Reinstall the plug.
(4) Turn the crankshaft by hand and leave it where the resistance is the heaviest.
(5) Clean outside of the engine with oiled cloth.
(6) Put a plastic cover or the like over the engine and store the engine in dry place.
Summary of Contents for EH63
Page 1: ...SERVICE MANUAL EH63 64 65 and EH72 ENGINES Models PUB ES2158 Rev 08 09 ...
Page 84: ......
Page 85: ...PRINTED IN THE USA ...