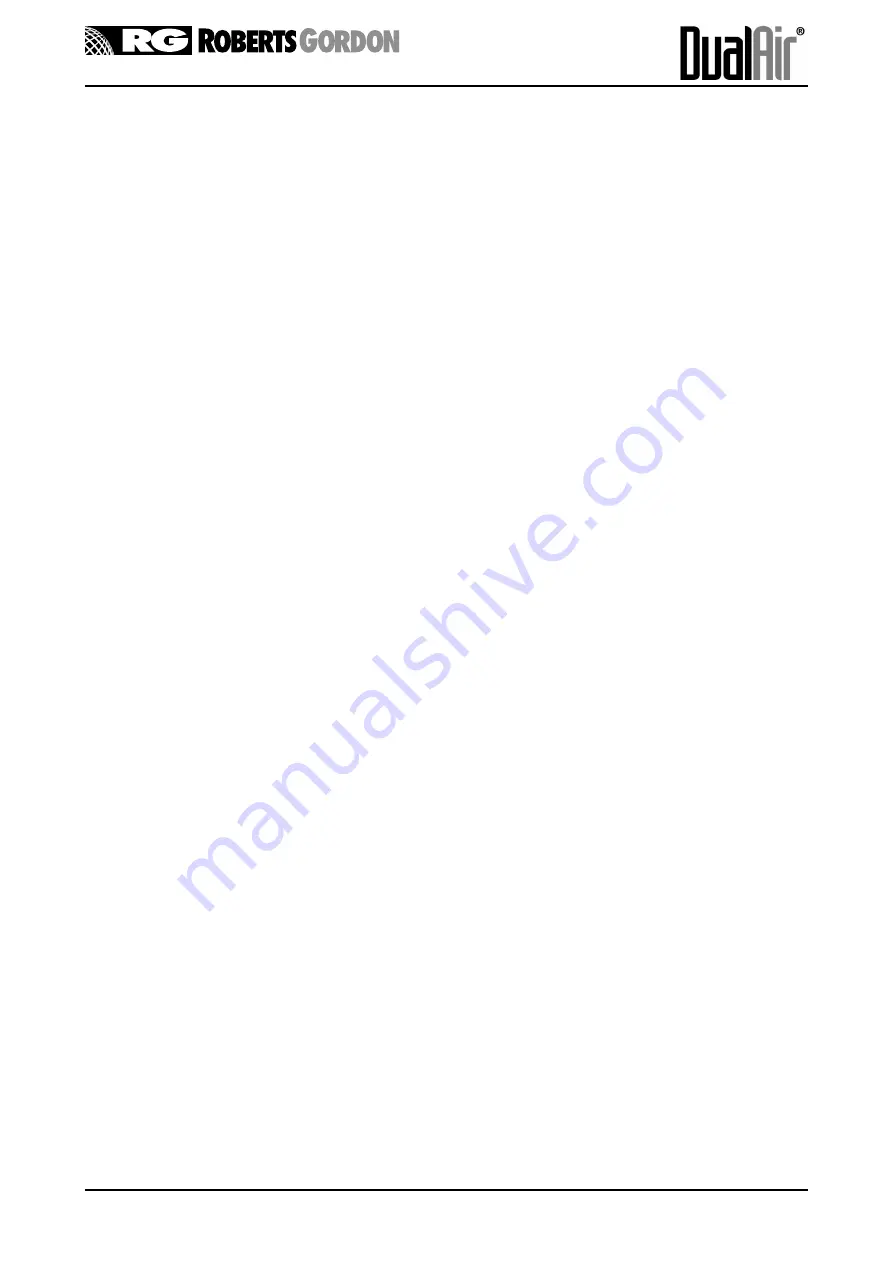
Page 16
2.7
Motor Starter and Thermal Overload
On belt driven fan models the motor is controlled by a direct on line contactor starter fitted with
thermal overload protection. If the thermal overload should operate the main fan will not run. To reset,
press in the reset button on the overload unit (see Fig. 2.4).
The overload should be set to indicate approximately 0.2 amps above the normal running current of
the heater.
Note: Running the fan with the fan compartment access panels removed may cause the thermal
overloads to operate due to the reduced resistance on the fan.
2.8
Frost Thermostat for the Cooling Coil
As part of the built in equipment a frost protection thermostat is fitted to protect the cooling coil from
freezing should the air flow fall to a low level during the cooling cycle.
It is strongly recommended that this control is connected and set (see 4.10) to give the cooling
coil protection from freezing which would cause severe damage.
2.9 Pressure Switch for the Cooling Coil/Filters
As part of the built in equipment a differential pressure switch is fitted to monitor the overall pressure
loss across the cooling coil and filters. The control is designed to turn off the control circuit of the
external condenser units to prevent any damage to the cooling coil due to blocked filters or other
reduced air flow. This should be set on site to reflect the installed conditions and to monitor the
differential pressure across the coil and filter.
The pressure setting on this pressure switch should be set so that the filter pressure switch (2.10)
operates first to give warning of impending problems
2.10
Pressure Switch for Air Filters
As part of the built in equipment a differential pressure switch is fitted to monitor the pressure loss
across the filter section.
The control is designed to turn on the built in amber warning light and also provide a 230v output at
terminals 22 & 23 for remote indication of the filters becoming blocked. This is an indication only and
warns that the filters need attention and should be set on site to reflect the installed conditions and to
monitor the differential pressure across the filter.
The maximum recommended final resistance across a dirty filter is 150 Pa (1.5 mbar).
Summary of Contents for Dualair DA260G Series
Page 2: ...Details of condense drain for cooling coil ...
Page 9: ...Page 7 Fig 2 2 DualAir 380 Module Dimensions FRONT VIEW REAR VIEW SIDE VIEW ...
Page 34: ...Page 32 Fig 5 2 Wiring for DualAir Units On Off Burner 24v Controls ...
Page 35: ...Page 33 Fig 5 3 Wiring for DualAir Units Hi Low Burner 230v Controls ...
Page 36: ...Page 34 Fig 5 4 Wiring for DualAir Units Hi Low Burner 24v Controls ...
Page 37: ...Page 35 Fig 5 6 Wiring for DualAir Units BMS Burner Modulation 230v Controls ...
Page 38: ...Page 36 Fig 5 7 Wiring for DualAir Units BMS Burner Modulation 24v Controls ...
Page 39: ...Page 37 Fig 5 7 Wiring for DualAir Units Full Burner Modulation 230v Controls ...
Page 40: ...Page 38 Fig 5 8 Wiring for DualAir Units Full Burner Modulation 24v Controls ...
Page 41: ......
Page 42: ......
Page 43: ......
Page 44: ......
Page 45: ......
Page 46: ......
Page 47: ......
Page 48: ......
Page 49: ......
Page 50: ......