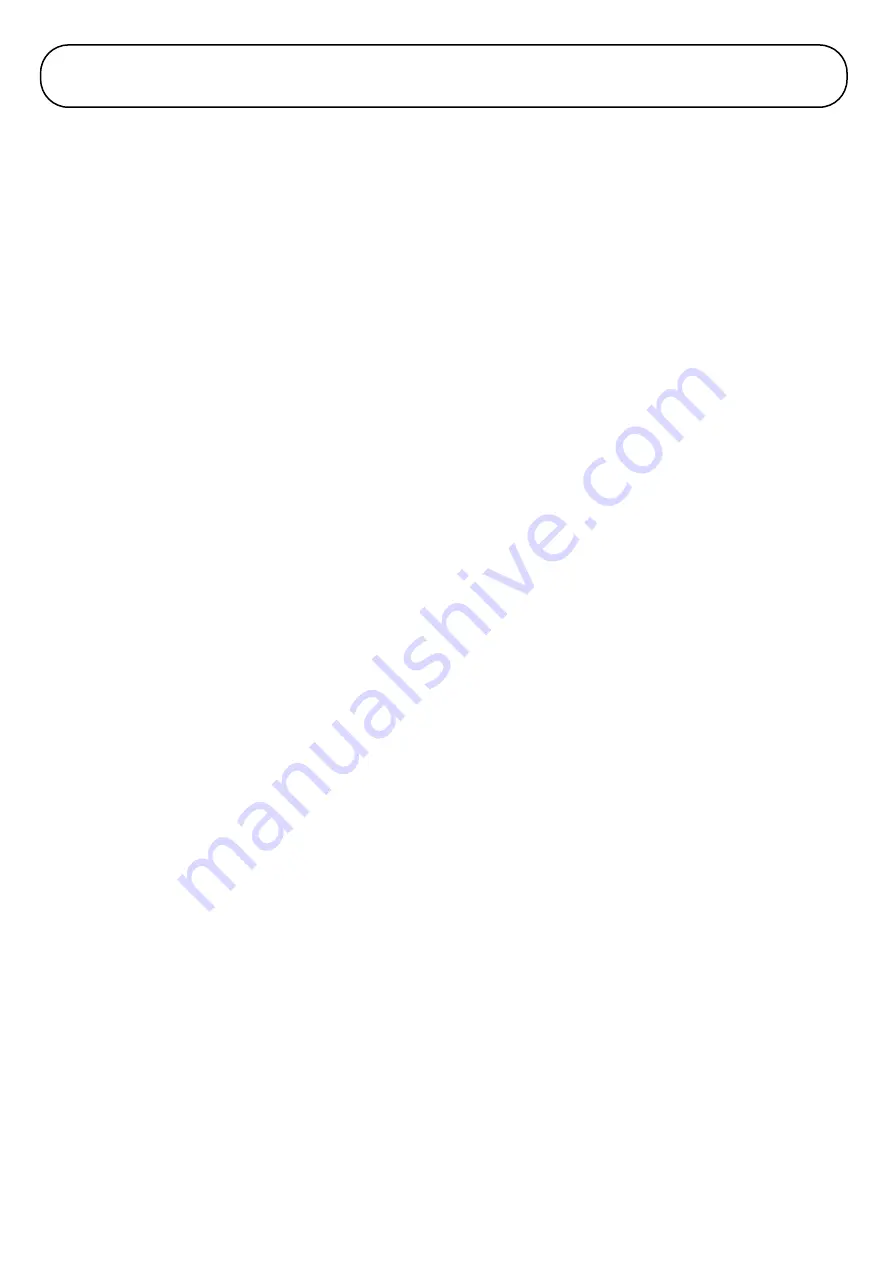
6
Taurus 50
-
Don’t kink the cables.
-
Install the RC system switch as shown in the drawing.
Stage 7: the canopy
-
Cut out the glazed areas of the canopy.
-
Cut the clear canopy glazing material to size, cutting along
the marked lines.
-
Place the glazing panel on the canopy, drill the fixing holes
and secure with six 2.3 Ø x 8 mm self-tapping screws.
-
Apply the coloured decals to the cabin.
-
Rotate the main rotor to check the relative direction of
rotation of the main and tail rotors.
Stage 8: the main rotor blades
-
Fit a single screw through the pivot holes of both main
rotor blades and tighten a nut on the other end to hold
them together.
-
Support the assembled rotors in the exact centre.
-
The lighter blade will now rise; apply coloured tape to the
lighter tip until the blades balance exactly level.
-
Fix the rotor blades to the blade holders using the screws
SFH3013 and self-locking nuts SFH3022.
-
Tighten the screws just to the point where the rotor blades
are still free to swivel in the blade holders.
-
The kit is supplied with optional trim weights (3.5 Ø x 70
mm) which can be fitted to the flybar paddles to provide
added stability.
-
If you wish to use the weights, push them into the front
holes in the control paddles and secure them using the M4
x 6 grubscrews supplied.
Setting up the radio control system
Basic requirement:
You need a radio control system designed for helicopter use,
with an HR 3 swashplate mixer.
Connect the servos to the receiver in the sequence described
in the operating instructions.
Procedure:
-
Switch on the transmitter
-
Select a vacant model memory
-
Program the model memory to the „Heli“ mixer type
-
Set the swashplate mode to „HR 3“
-
Activate the tail rotor mixer (Revo-Mix) if required by the
gyro you are using
-
Program the system for a right-hand rotation main rotor
-
Set all transmitter sticks and trims to centre
-
Do not activate any trim memories or freely programmable
mixers
-
Program throttle trim to idle trim (ATL - throttle trim active
only at idle end of range)
-
Switch on the receiving system
Setting up the servos for collective pitch
-
Check the travels and directions of the servos.
-
Move the collective pitch stick in the direction of collective
pitch maximum: all three servos mounted below the
swashplate should now move in the same direction and
through the same distance, thereby raising the swashplate
evenly, without tilting it at all.
Setting up the servos for roll and pitch-axis movements
-
Check the direction of servo rotation.
-
Apply a roll command to the right: the swashplate should
tilt to the right as seen from the tail of the model.
-
Use the servo reverse facility on your transmitter if any of
the servos moves in the wrong direction.
-
Apply a forward pitch (forward cyclic) command: the
swashplate should tilt forward.
-
Use the servo reverse facility on your transmitter if any of
the servos moves in the wrong direction.
Setting up the tail rotor servo
-
Note:
When you move the tail rotor stick to the right, the
pitch angle of the tail rotor blades should increase (control
bridge moves towards the tail boom).
-
Reverse the tail rotor servo if necessary.
Checking the direction of gyro effect (sketch 1)
Set the gyro to maximum gain.
Swing the tail boom briskly to the right (i.e. the helicopter’s
nose moves to the left).
The pitch angle of the tail rotor blades should now increase -
direction „+“.
Reverse the gyro direction if necessary. If your gyro is a simple
type without a reversing switch (e.g. G 200), invert the gyro
element.
The throttle servo
Move the transmitter throttle control to the „full throttle“
position, and the carburettor barrel should open fully. At the
„motor stopped“ position the barrel opening should be
completely closed.
You may need to adjust servo travel to achieve this; use the
servo travel adjustment facility on your transmitter. It is
essential that the servo is not mechanically obstructed (stalled)
at either end-point. Listen for unusual servo noises which
indicate stress. We recommend that you achieve the correct
adjustment using servo travel in the range 90 to 110%. If your
transmitter does not feature servo travel adjustment, re-