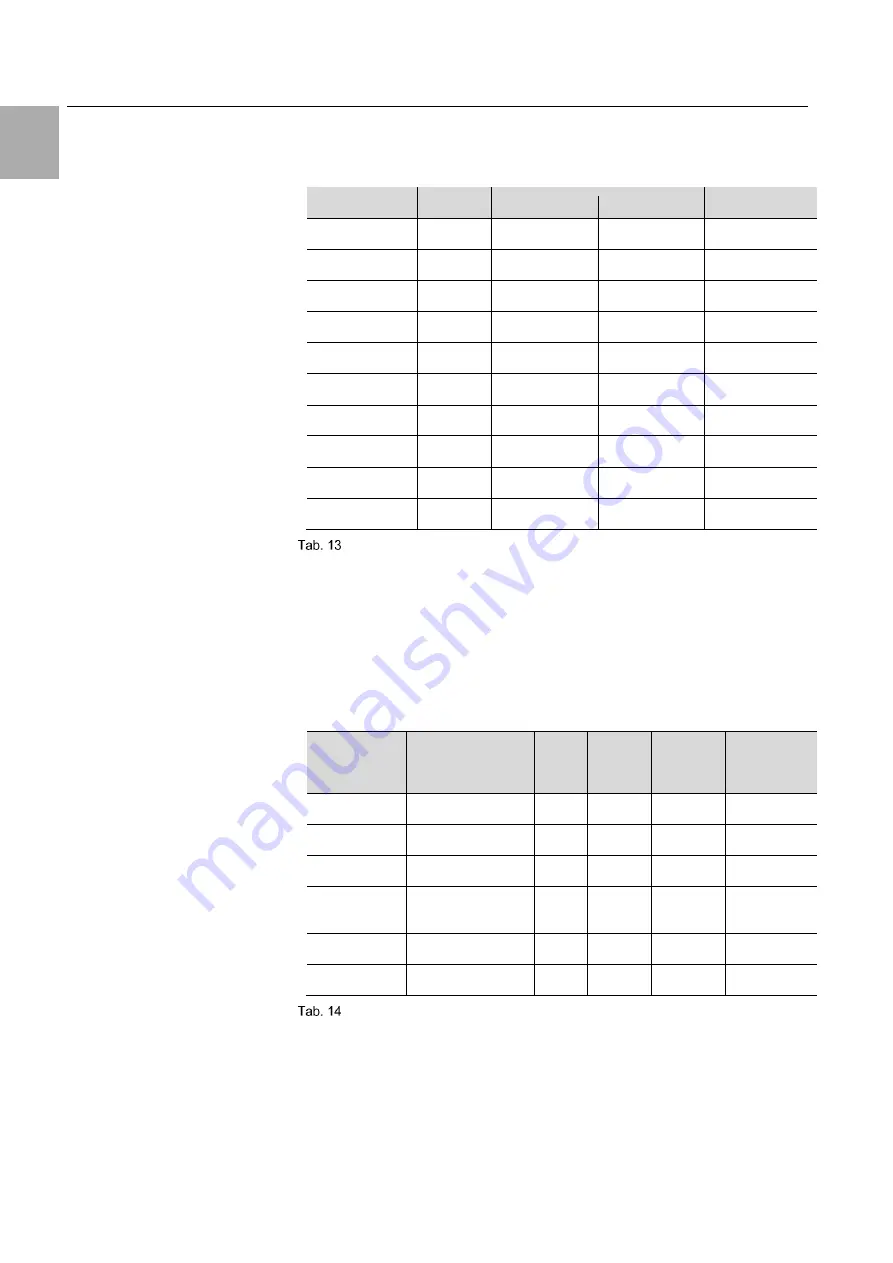
9 Appendixes
46
Rittal Perforex BC machining centre
EN
9.2 Drill
Drill in OEM quality for Perforex BC machining centres. Suitable for all Per-
forex types.
Suitable for BC
Type
Ø [mm]
Packs of
Model No.
All
S
2.6
10
4050.801
All
S
3.3
10
4050.802
All
S
4.2
10
4050.803
All
S
5.0
10
4050.804
All
S
6.0
10
4050.805
All
S
6.8
10
4050.806
All
S
8.5
10
4050.807
All
S-k
8.5
5
4050.808
All
S
10.5
5
4050.809
All
S-k
10.5
5
4050.810
: Drill
Identification type:
S
= Twist drill
S-k = Short twist drill
9.3 Milling cutter
Milling cutter in OEM quality for your Perforex BC machining centre. Recom-
mendation: Milling cutter types in accordance with recommended material
that should be milled.
Suitable for
BC
Workpiece
material
Type
Ø [mm]
Packs of
Model No.
All
Steel
S
6.0
10
4050.818
All
Steel
P
6.0
5
4050.891
All
Stainless steel
PM
4.0
5
4050.885
All
Steel / stainless
steel
P+
6.0
5
4050.620
All
Aluminium/plastic
A
6.0
5
4050.819
All
Aluminium/plastic
A
4.0
5
4050.820
: Milling cutter
Identification type:
S
= Standard milling cutter
P
= Performance milling cutter
PM = PM milling cutter
P+ = Perf milling cutter
A
= Airline