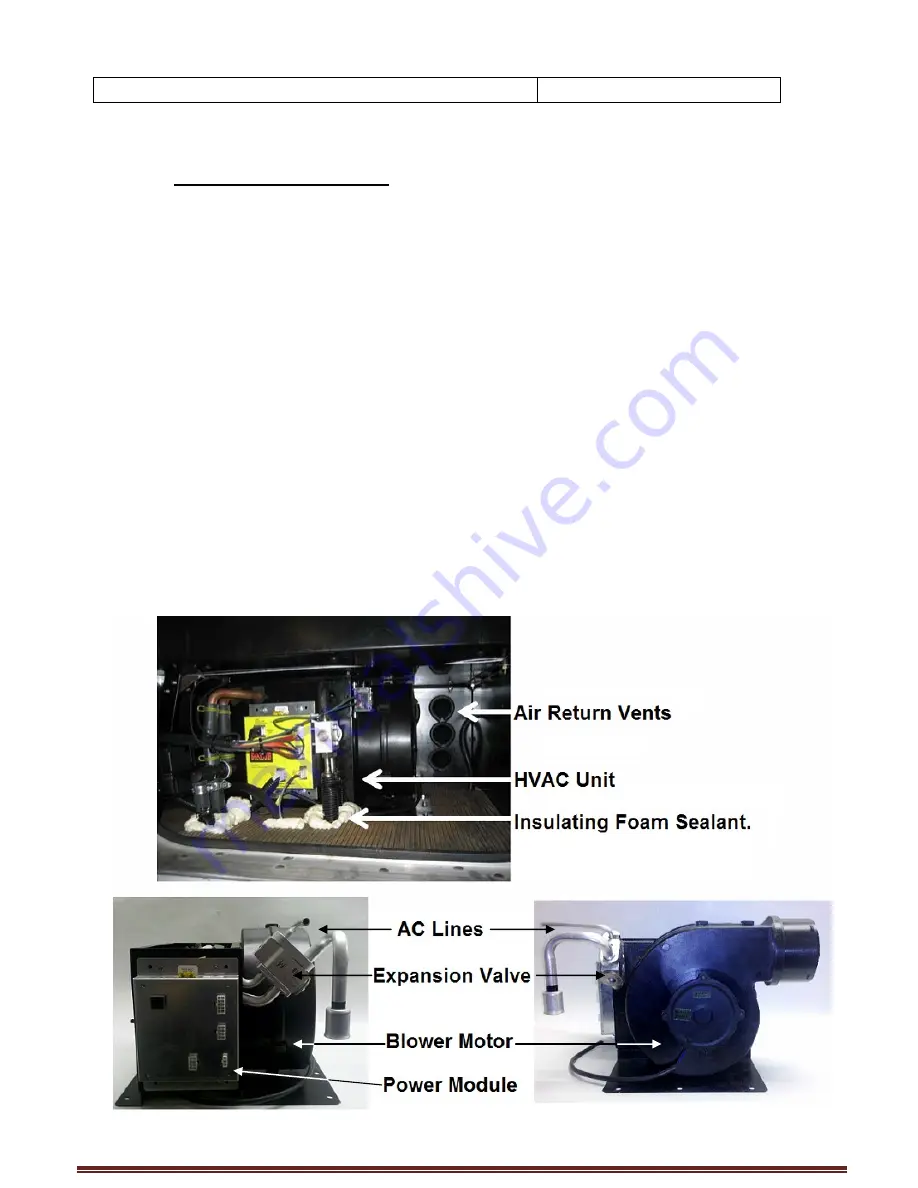
RigMaster LG200 Installation Manual
Section 3
August 2010 RigMaster Power International Ltd LG200 Service Manual
3:1:1
Mounting the HVAC Unit
The HVAC unit has a flush mount filter secured by two thumb nuts. Before
installation, see that there is enough room to remove the filter. Leave sufficient
clearance on all sides for proper air flow.
1. Drill holes for the air conditioning hoses, coolant hoses, condensation drain
tube and wiring. It is recommended that the holes be piloted with a 3/16” drill
bit prior to drilling the 1 1/4” holes with the hole-saw. After drilling use a file to
remove any sheet metal burrs that remain and protect edges with grommets
or slit hose. All holes can be drilled individual or grouped together for less
holes in sleeper cab. It is also very important to seal the holes with silicon to
prevent and fumes from entering the sleeper cab.
2. Attach the condensation drain tube to the bottom of the HVAC box using the
supplied hose clamp, usually found inside the owner’s envelope.
3. Lower the HVAC box into the cab of the truck and ensure that the drain
hose went through the corresponding hole.
4. Do not secure the HVAC unit to the floor of the vehicle until you are sure that
all connections are correct and fully secured.