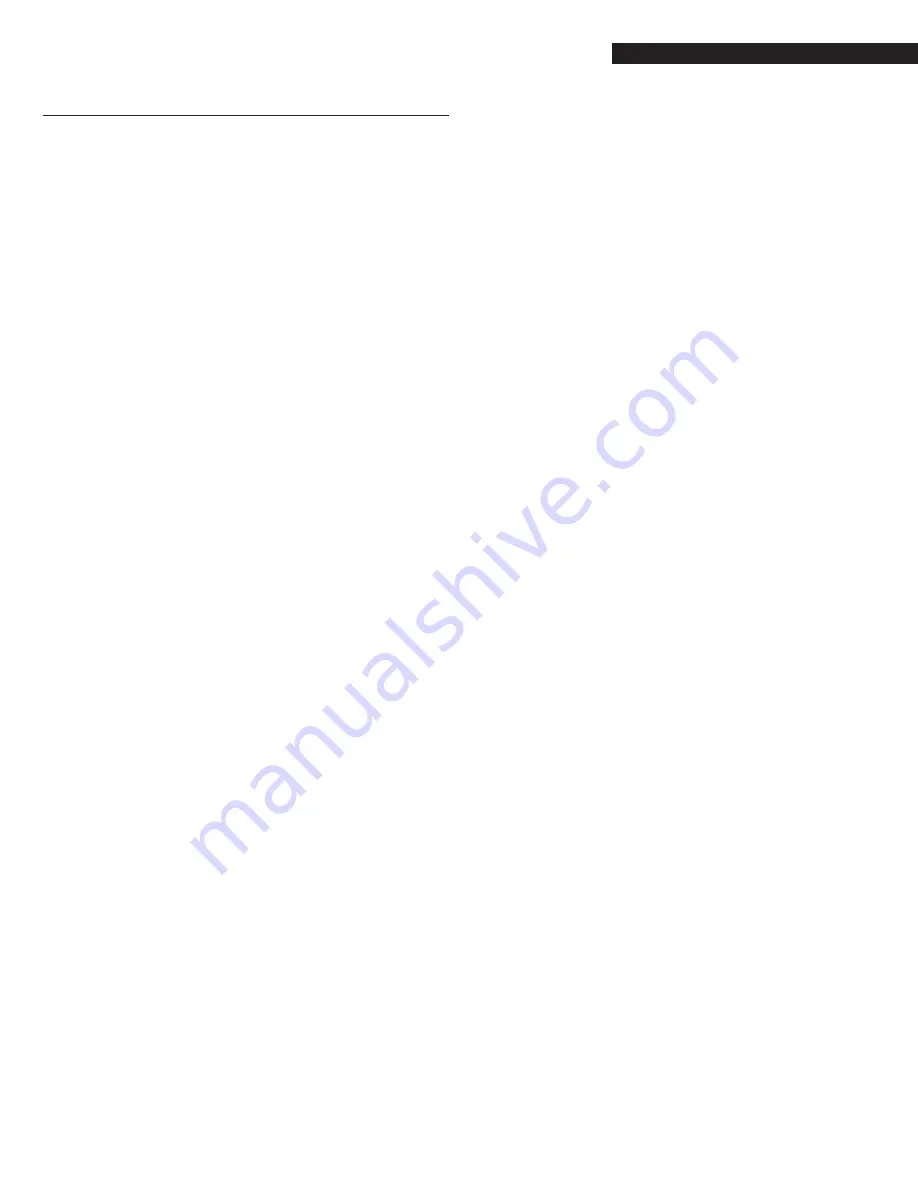
5
INTRODUCTION
4
INTRODUCTION
The Condexa PRO NA it is a condensing, pre-mixed thermal mod-
ule consisting in a modulating thermal element.
It's available in two models of power: 255.900 BTU/hr (75 kW) and
399.000 BTU/hr (117 kW).
Optimal combustion management supports high thermal efficien-
cies (Over 95%) and low polluting emissions.
The boiler is designed for sealed chamber operation.
The appliance in standard configuration is for indoor installation to
guarantee an IPX4D protection level.
9
The
Condexa PRO NA
boilers can be cascaded to reach a maxi-
mum power of 2.388.500 BTU/hr (700 KW).
The appliance's key technical features are
− helicoidal heat exchanger with a double coil smooth stain-
less steel pipe, to guarantee good corrosion resistance and
the option of operating with high
∆
ts (up to 72°F [40°C]), re-
ducing system set-up times;
− maximum exhaust flue exit temperature 212°F [100°C];
− microprocessor management and control with self-diag-
nostics, shown by means of a display, and logging of main
errors;
− Anti-Freeze function;
− pre-settings for room/heat demand thermostat for low and
high temperature ranges;
− option to manage a CH circuit and a DHW circuit with storage
tank;
− high-efficiency and high residual discharge head circulator;
− climate control function (available only when using the out-
door temperature sensor accessory).
All appliance functions are electronically controlled by a dual pro-
cessor technology board.
Any malfunction results in the appliance being shut down and the
automatic closure of the gas valve.
The following is installed on the CH water circuit:
−
Safety high-limit thermostat
.
−
Flow sensor
capable of monitoring the main heating cir-
cuit's flow on an ongoing basis and of stopping the appli-
ance in the event of insufficient flow.
−
Temperature sensors
on supply and return lines that mea-
sure the temperature difference (
∆
t) between input and
output fluid and allow the boiler to fire when a demand is
made.
−
LWCO/Minimum Water Pressure Switch
(set to 7 psi/0.5 bar).
The following is installed on the combustion circuit:
−
Gas solenoid
with pneumatic gas flow compensation de-
pending on the suction line's air flow rate.
−
Ignition/detection electrode
.
−
Flue gas temperature sensor
.
9
WARNING
: The triggering of safety devices indicates the mal-
function of a potentially hazardous situation. Therefore, contact
a service agency immediately. After a brief pause, it is possible
to try and restart the appliance (see section "Initial startup").
9
WARNING
: Safety devices must be replaced a qualified installer,
service agency or gas supplier, using only original parts. Refer
to the spare parts catalogue supplied with the appliance. After
making the repair, check that the appliance is working prop-
erly.
0
WARNING
: The appliance must not be put in service, even tem-
porarily, when tampered safety devices are not in operation or
have been with.
− Use a low water cutoff designed for hydronic installations;
− Follow low water cutoff manufacturer’s instructions.
9
A hot water boiler installed above the radiation level or as re-
quired by the Authority having jurisdiction, must be provided
with a low water cutoff device either as part of the boiler or at
the time of boiler installation.
9
NOTE:
The LWCO/Minimum Water Pressure Switch (set to 7 psi/0.5
bar) located internally in the Condexa PRO 75 and 117 is below
the lowest safe permissible water level established by the boil-
er manufacturer.