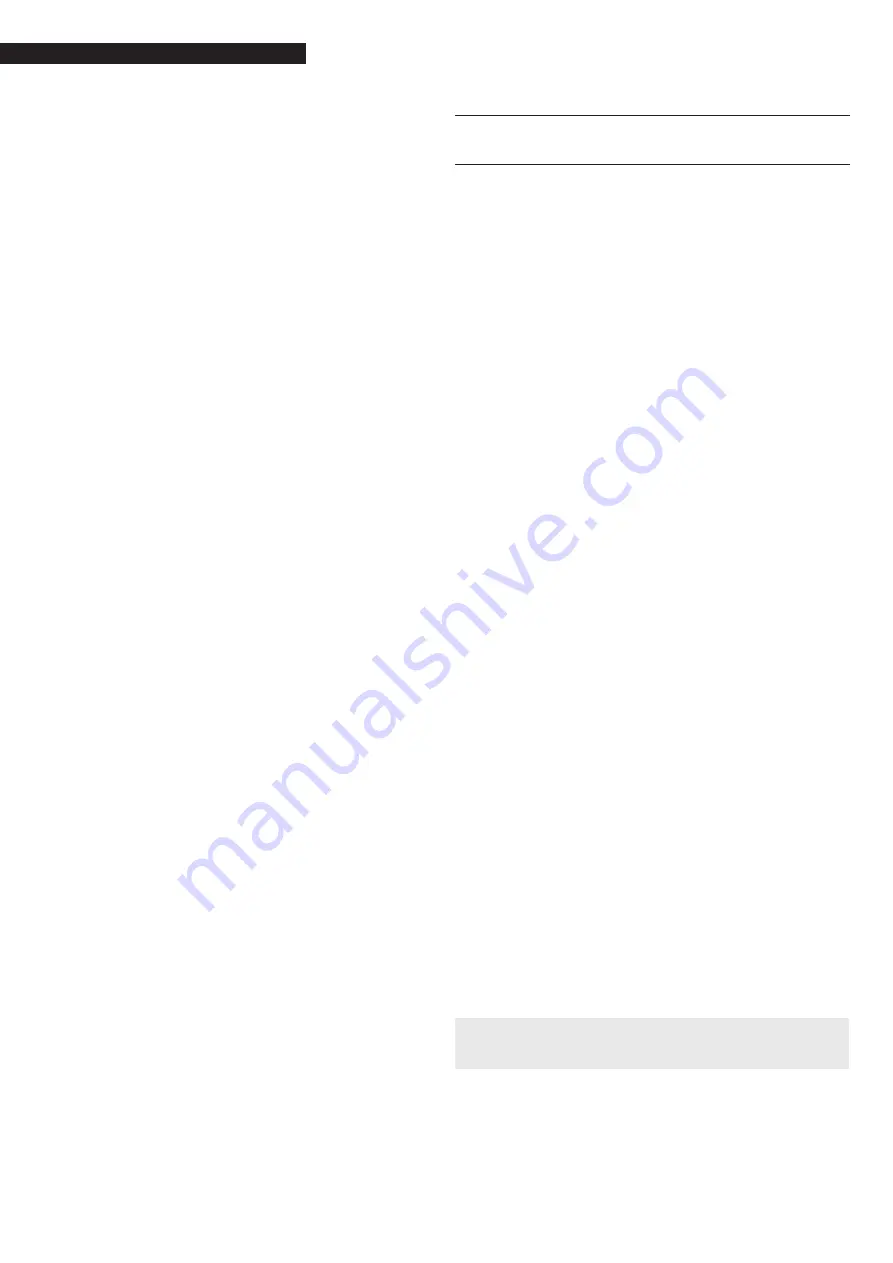
158
COMMISSIONING
INSTALLATION
CONFIGURATION
The user can add a setpoint relative to the minimum condens-
ing temperature (default value = 40°C) to increase the heat ca-
pacity recovered by the desuperheaters, if required.
In fact, the percentage of heat recovery capacity compared to
the overall capacity released by the air exchanger increases ac-
cording to the saturated condensing temperature.
Refer to section "Control panel" to adjust the minimum satu-
rated condensing temperature setpoint.
The other parameters that directly affect the effective capacity
recovered by the desuperheater are mainly:
− unit load factor, that manages the operation at full load
(100%) or at partial load (according to the number of
unit compressors per circuit)
− desuperheater entering water temperature, according to
the unit "Heating or Cooling" operating mode.
5
COMMISSIONING
5.1
Preparation for first commissioning
The equipment first commissioning must be carried out by the
Technical Support Service.
Prior to commissioning, it is necessary to check that:
− all the safety conditions have been met
− the required distances have been respected
− in order to prevent the formation of ice during defrosting
operations, or the continuous modulation of the com-
pressor's frequency, the amount of water in the primary
circuit is greater than the minimum volume indicated in
the chapter "System water content and flow rate"
− the water system's shut-off devices are open
− the water circuit has been deaerated
− the mesh filter has been installed and has been properly
cleaned after charging the system
− the electrical connections have been properly complet-
ed
− the electrical power supply's values are correct
− the earthing has been carried out correctly
− all the connections have been properly tightened
− check that the machine has been charged with refriger-
ant. Check on the data plate that the "conveyed fluid"
is the one recommended for the operation - and not
nitrogen.
− Check for the presence of all documents supplied by
the manufacturer (dimensional drawings, P&I diagram,
declarations, etc.) as required by law. If part of the doc-
umentation is missing, request it.
− Check for the presence of environmental safety devices
and protection devices supplied by the manufacture as
required by law.
− Check for the presence of all declarations of conformity
for pressurised containers, identification plates and the
required documentation in compliance with local reg-
ulations.
− Check the instructions and directives to avoid the inten-
tional removal of refrigerant gases.
− Check welding and other connections quality.
− Check the protection against mechanical damages.
− Check the heat protection.
− Check the protection of the moving parts.
− Check the valve status.
− Check the quality of the thermal insulation.
− Check the insulation status of the 400 V cables.
9
If the compressors are equipped with supports, check
whether they are provided with fastening mechanisms.
If so, the fastening mechanisms must be removed before
starting the system. The fastening mechanisms are identi-
fied with red collars and marked with a label fixed to the
compressor sub-unit.
9
Always wear suitable Personal Protective Equipment.
9
The device must always be powered electrically in order to
allow for the compressor's oil to be properly pre-heated.
9
The device must receive electrical power for at least eight
hours before being started up for the first time.
Summary of Contents for 20120391
Page 93: ...93 PANORAMICA DEI PARAMETRI INSTALLAZIONE ...
Page 169: ...169 ALARM CODES INSTALLATION ...
Page 185: ...185 OVERVIEW OF THE PARAMETERS INSTALLATION ...
Page 186: ......
Page 187: ......