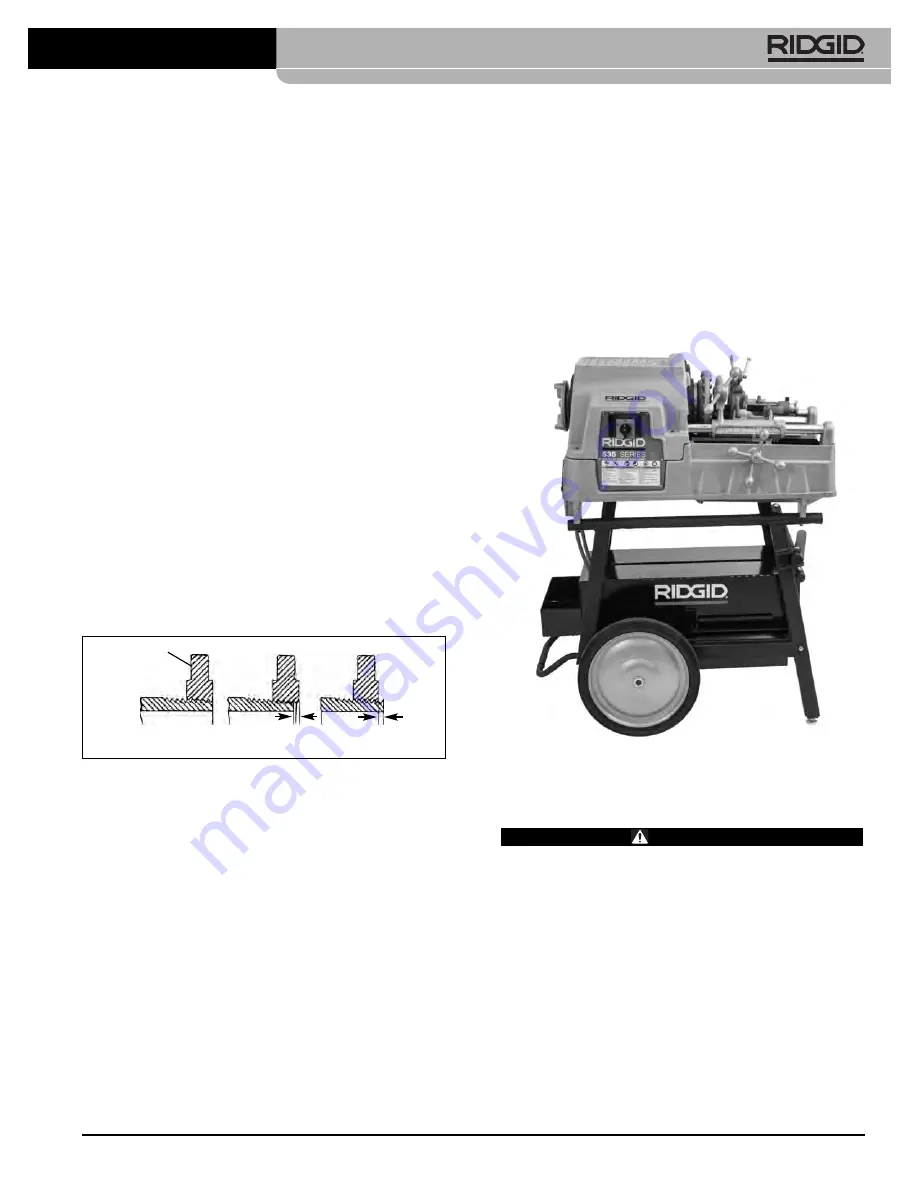
2. Clean the chips and other debris from the chip tray.
Remove or secure all loose equipment and material
from the machine and stand prior to moving to prevent
falling or tipping. Clean up any oil or debris on the floor.
3. Place the cutter, reamer and die head in the operating
position.
4. Coil up the power cord and foot switch cord. If need-
ed, remove the machine from the stand.
5. Use care in lifting and moving, follow stand instruc-
tions. Be aware of the machine weight.
Figure 28 – Machine prepared for Transport
Maintenance Instructions
WARNING
Make sure that the ReV/oFF/FoR Switch is in the
oFF position and the machine is unplugged before
performing any maintenance or making any adjust-
ments.
Maintain threading machine according to these
procedures to reduce the risk of injury from elec-
trical shock, entanglement and other causes.
Cleaning
After each use, empty the threading chips from the chip
tray and wipe out any oil residue. Wipe oil off exposed sur-
faces, especially areas of relative motion like the car-
riage rails.
2. Firmly grip the pipe and remove from the machine.
Carefully handle the pipe as the thread may still be hot
and there may be burrs or sharp edges.
Inspecting Threads
1. After removing the pipe from the machine, clean the
thread.
2. Visually inspect thread. Threads should be smooth
and complete, with good form. If issues such as
thread tearing, waviness, thin threads, or pipe out-of
roundness are found, the thread may not seal.
Refer
to the Troubleshooting Chart
for help in diagnosing
these issues.
3. Inspect the size of the thread.
• The preferred method of checking thread size is with
a ring gauge. There are various styles of ring
gauges, and their usage may differ from that shown
here.
• Screw ring gauge onto the thread hand tight.
• Look at how far the pipe end extends through the
ring gage. The end of the pipe should be flush with
the side of the gauge plus or minus one turn. If
thread does not gauge properly, cut off the thread,
adjust the die head and cut another thread. Using a
thread that does not gauge properly can cause
leaks.
Figure 27 – Checking Thread Size
• If a ring gauge is not available to inspect thread size,
it is possible to use a new clean fitting representa-
tive of those used on the job to gauge thread size.
For 2" and under NPT threads, the threads should
be cut to obtain 4 to 5 turns to hand tight engage-
ment with the fitting and for BSPT it should be 3
turns.
4. See
Adjusting Thread Size
under
Die Head Set-Up
and Use
heading to adjust thread size.
5. Test the piping system in accordance with local codes
and normal practice.
Preparing Machine for Transport
1. Make sure that the REV/OFF/FOR switch is in the
OFF position and the cord is unplugged from the
outlet.
999-998-086.10_REV. C
17
535 Manual Chuck/535 Auto Chuck Threading Machines
Flush
(Basic Size)
One Turn Large
(Maximum Size)
One Turn Small
(Minimum Size)
Ring
Gauge