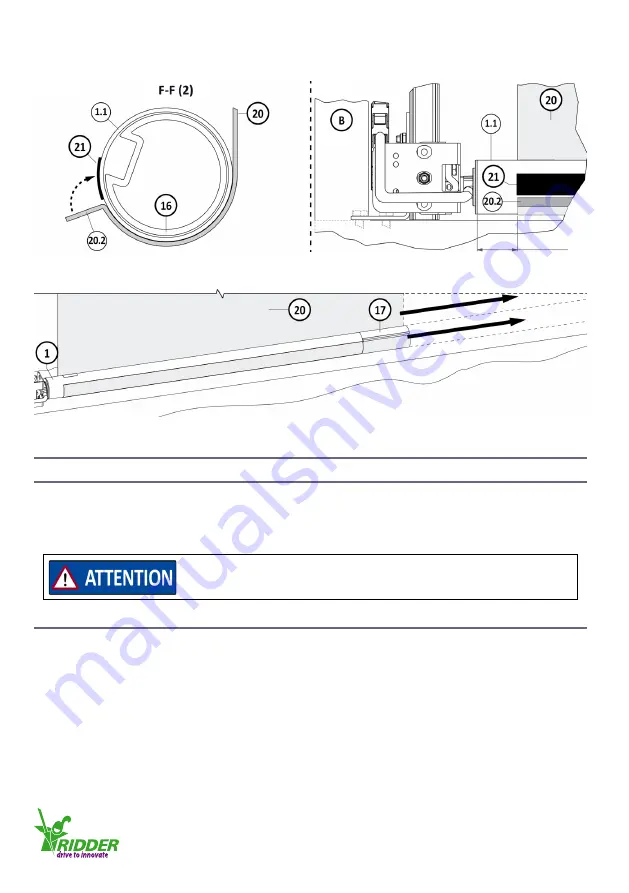
10. Attach the screen cloth (20.2) onto the tube (1.1) with double-sided adhesive tape (21). Refer to
illustrations 4.7.1/4.7.6/4.7.7.
11.
Pull the screen cloth (20) tight along the full length. Make sure that it does not fold!
5. CONNECT INSTRUCTIONS
5.1 Electrical material
•
A minimum conductor diameter of
1.5 mm²
is applicable to the cables in the wiring diagrams. For
the used components, electrical material and cable lengths the necessary conductor diameter can
be different.
5.2 Protection - Conditions and starting points
The conditions that follow are applicable to the wiring diagrams.
•
The installer makes sure that a motor-protection circuit-breaker (MPCB) and other necessary
protections are used.
•
The installer must include not shown protections in the wiring diagrams.
•
Do not connect other electrical equipment (lamps, relays and such) directly to the connection
cables of the motor.
•
Isolate all poles, with a minimum contact separation of 3 mm per pole (EN 60335), from the
mains voltage.
40 mm
4.7.6
4.7.7
Use only applicable components and electrical material.
Always refer to the related information and manuals.
Ridder Drive Systems
T
+31 (0)341 416 854
F
+31 (0)341 416 611
I
www.ridder.com
22
Summary of Contents for RB50EPLUS
Page 36: ...www ridder com...