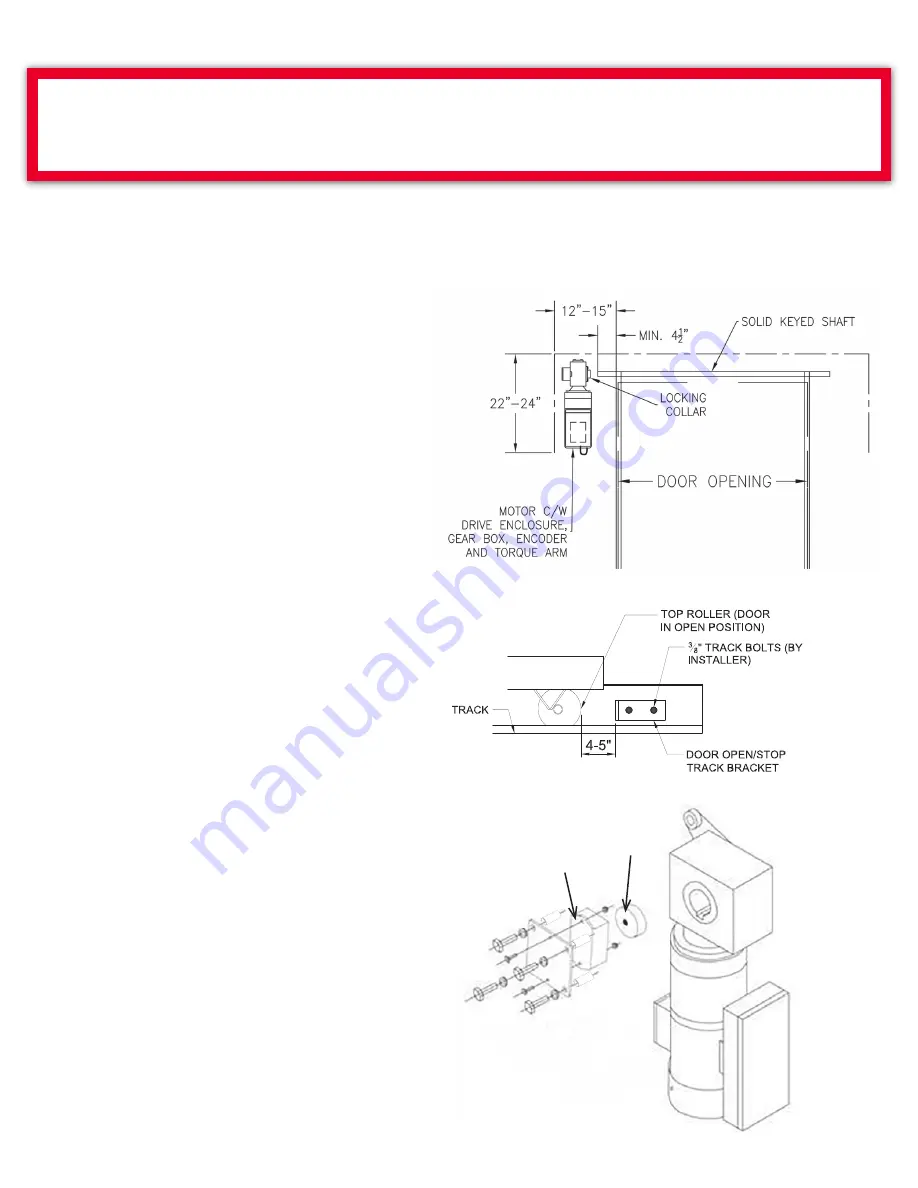
4
5
PRE-INSTALLATION ASSEMBLY REQUIREMENTS
BEFORE INSTALLATION, ENSURE THAT YOUR DOOR IS PROPERLY BALANCED AND RUNNING
SMOOTHLY. ALSO ENSURE THAT THE LIMIT BRACKETS (SUPPLIED) ARE INSTALLED AND
SECURED PROPERLY. BUMPER/PUSHER SPRINGS MAY BE USED IN PLACE OF, OR IN ADDITION TO
LIMIT BRACKETS FOR DYNA-HOIST OPERATORS, BUT MUST BE INSTALLED PRIOR TO OPERATION.
Operator Mounting Requirements
Dyna-Hoist operators are mounted directly on the door shaft. Before installing the operator, please ensure follow-
ing criteria is met:
The door is well balanced, is tested for smooth
functioning without any unusual noise.
Provided Limit Brackets must be installed
4"-5" past door's desired open position (and within
allowable maximum cable height) to prevent the
doors from over-travel. (See Fig. 1A)
The door has a solid keyed shaft with a minimum
exposed length of 4.5” on the operator side.
Clearance of at least 12” horizontally from the
side of the door (or 9” from end of shaft), and
24” vertically below the shaft. There is adequate
structural support surface to securely install the
torque arm mounting bracket, the torque arm and
the junction box. For more details, see mounting
installation instructions
Fig: 1 & 7.
Mounting space for the operator Control Panel
(Min. 5 ft. from ground level, within clear sight of the
door but far enough away as to prevent users from
contacting moving parts).
Left Hand Mounting:
The factory default mounting as shown
(Shown in Fig: 2) is for left-hand side of the
door, hence no modification is required.
FIGURE: 1
FIGURE: 2
Magnet on
this side
Encoder
FIGURE: 1A
Summary of Contents for DYNA-HOIST DC Series
Page 7: ...7 TORQUE ARM POSITION IN RELATION TO OPERATOR ...
Page 13: ...13 WIRING DIAGRAMS ...
Page 14: ...14 ...
Page 15: ...15 ...
Page 16: ...16 ...
Page 17: ...17 ...
Page 26: ...26 DYNA HOIST OPERATOR COMPONENTS ...
Page 31: ...31 NOTES ...