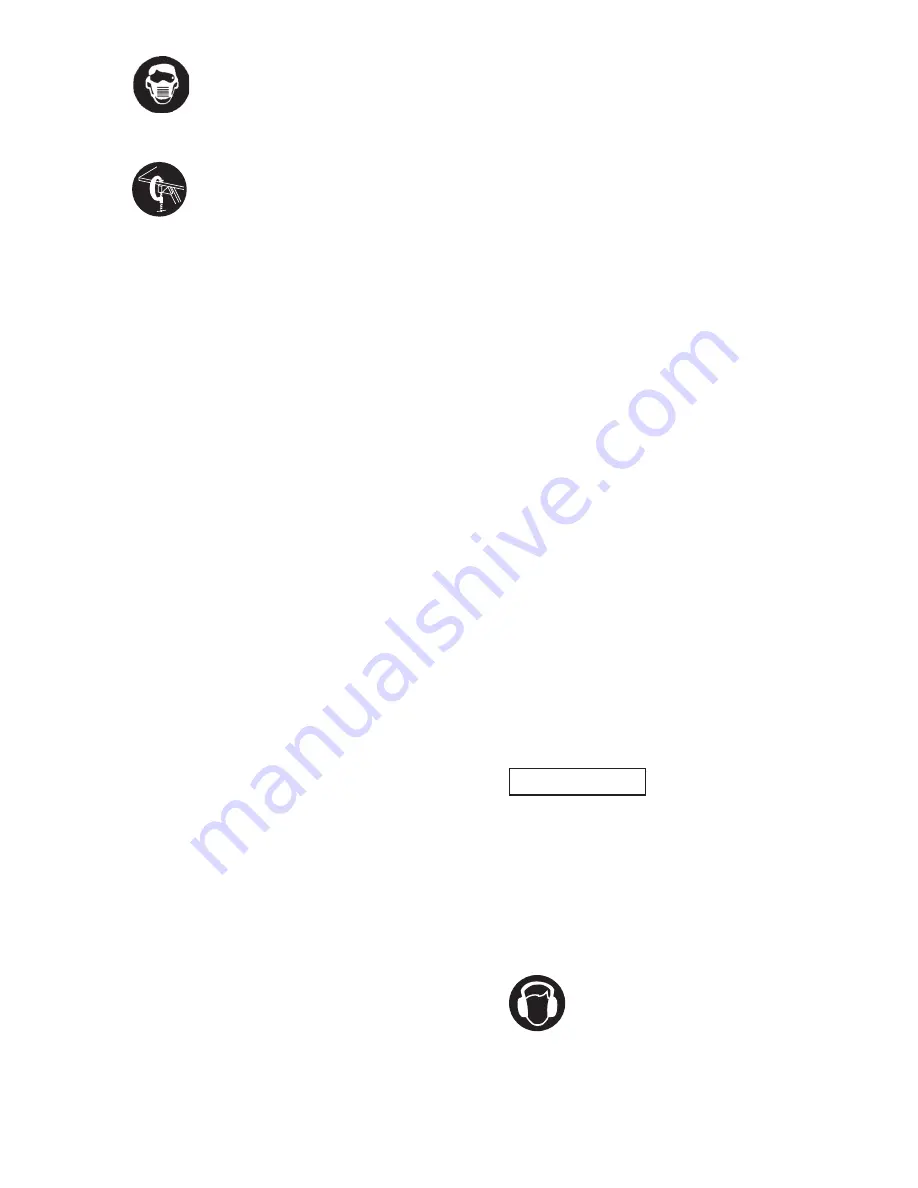
4
5
4
5
20.
NEVER LEAVE THE TOOL
RUNNING UNATTENDED. TURN
THE POWER “OFF”.
Do not walk
away from a running tool until the
blade comes to a complete stop
and the tool is unplugged from the
power source.
21.
DO NOT OVERREACH
. Keep
proper footing and balance at all
times.
22.
MAINTAIN TOOLS WITH CARE
.
Keep tools sharp and clean for best
and safest performance. Follow
instructions for lubricating and
changing accessories.
23.
DO NOT
use power tool in
presence of flammable liquids or
gases.
24.
DO NOT
operate the tool if you are
under the influence of any drugs,
alcohol or medicationn that could
affect your ability to use the tool
properly.
25.
WARNING
: Dust generated from
certain materials can be hazardous
to your health. Always operate saw
in well-ventilated area and provide
for proper dust removal.
26.
People with
electronic devices,
such as pacemakers, should
consult their physician(s) before
using this product. Operation
of electrical equipment in close
proximity to a heart pacemaker
could cause interference or failure
of the pacemaker.
27.
WEAR HEARING
PROTECTION
to reduce
the risk of induced hearing
loss.
13.
WEAR A FACE MASK
OR DUST MASK
. Sawing
operation produces dust.
14.
SECURE WORK
. Use clamps or
a vise to hold work when
practical. It is safer than
using your hand and it frees
both hands to operate the
tool.
15.
DISCONNECT TOOLS FROM
POWER SOURCE
before servicing,
and when changing accessories
such as blades, bits and cutters.
16.
REDUCE THE RISK OF
UNINTENTIONAL STARTING
.
Make sure switch is in the OFF
position before plugging the tool in.
17.
USE RECOMMENDED
ACCESSORIES
. Consult this
Instruction Manual for recommended
accessories. The use of improper
accessories may cause risk of injury
to yourself or others.
18.
NEVER STAND ON THE TOOL
.
Serious injury could occur if the
tool is tipped or if the cutting tool is
unintentionally contacted.
19.
CHECK FOR DAMAGED PARTS
.
Before further use of the tool, a
guard or other part that is damaged
should be carefully checked to
determine that it will operate
properly and perform its intended
function – check for alignment of
moving parts, binding of moving
parts, breakage of parts, mounting
and any other conditions that may
affect its operation. A guard or
other part that is damaged should
be properly repaired or replaced.
DANGER
!