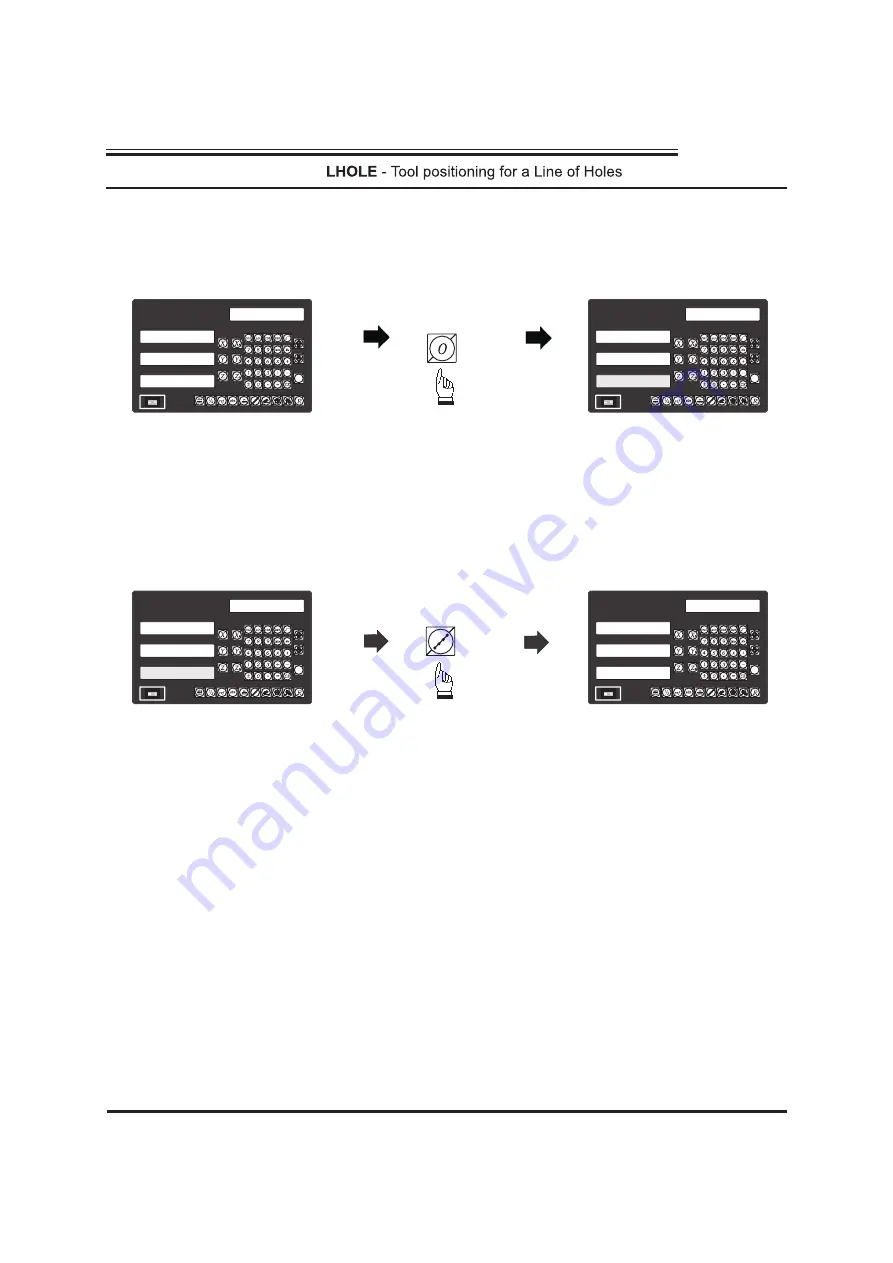
- 27 -
swap back
to LHOLE cycle to continue the Line Holes drilling operation
presently in the temporarily
XYZ coordinate display
return to
function cycle
LHOLE
After the Line Holes drilling operation is completed, and to leave the LHOLE function cycle,
follow the procedure below
presently in
function cycle
LHOLE
return back to normal
XYZ coordinate display
R
esson
Technologies
On
Off
RD-11M
R
esson
Technologies
ent
R
I
O
On
Off
RD-11M
R
esson
Technologies
ent
R
I
O
12.345
5.000
23.450
ABS
0.000
0.000
HOLE 1
swap back to
function cycle
LHOLE
On
Off
RD-11M
R
esson
Technologies
ent
R
I
O
On
Off
RD-11M
R
esson
Technologies
ent
R
I
O
0.000
0.000
HOLE 1
78.560
5.000
23.450
XYZ-ABS
Summary of Contents for RD-11M
Page 5: ...1 Basic Functions Resson Technologies On Off RD 11M Resson Technologies ent R I O...
Page 9: ...5 Resson Technologies...
Page 13: ...9 Resson Technologies...
Page 22: ...18 Resson Technologies On Off RD 11M Resson Technologies ent R I O...
Page 27: ...23 Resson Technologies...
Page 32: ...28 Resson Technologies...
Page 40: ...36 Resson Technologies...
Page 46: ...R R R 42 Resson Technologies...
Page 62: ...R R R 58 Resson Technologies...
Page 79: ...75 Resson Technologies...