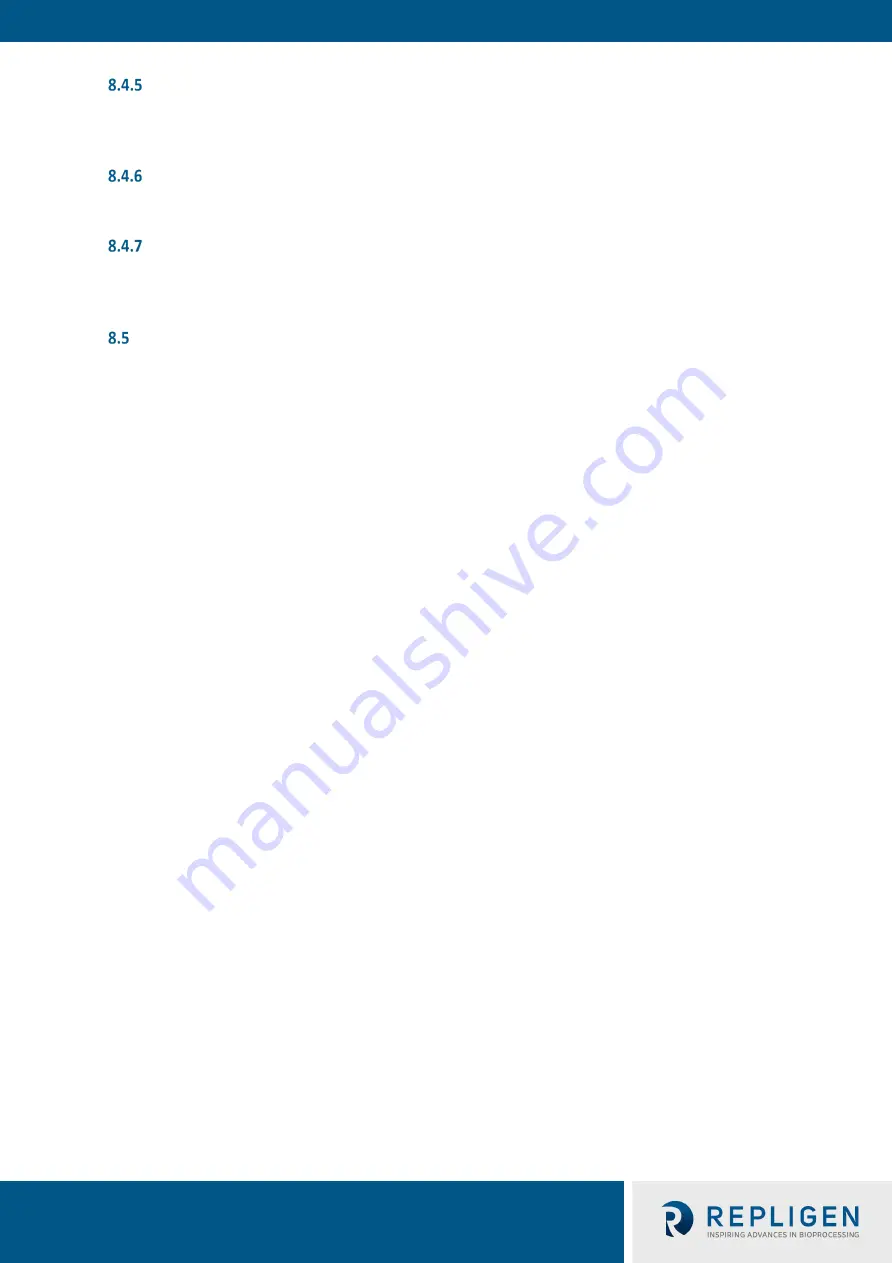
KrosFlo® TFDF™ Lab System
User Guide
38
repligen.com IF.UG.023 R1
Setting the maximum magnetic levitating recirculation/feed pump (P-01) speed
Select the
blue
box under Pump (P-01) Maximum Speed and enter a value. 2500 rpm is
recommended for most applications.
Setting pressure units
Select the button box under pressure units to toggle between psi or mBar.
Setting the Permeate Side Hold-up Volume
Select the
blue
box under Permeate Side Hold-up Volume and enter a value.
PID loop settings
The
proportional–integral–derivative controller
(
PID controller
or
three-term controller
) is a
control loop mechanism employing feedback between the systems pump and its sensors. A PID
controller continuously calculates an
error value
as the difference between a desired setpoint (SP)
and a measured process variable (PV) and applies a correction based on proportional, integral, and
derivative terms (denoted
P
,
I
, and
D
respectively).
The distinguishing feature of the PID controller is the ability to use the three
control terms
of
proportional, integral and derivative influence on the controller output to apply accurate and
optimal control. The controller attempts to minimize the error over time by adjustment of a
control
variable
, such as the speed of a pump, to a new value determined by a weighted sum of the control
terms.
In this model:
1.
Term P
is proportional to the current value of the SP
-
PV error
e(t)
. For example, if the error
is large and positive, the control output will be proportionately large and positive, taking
into account the gain factor "K". Using proportional control alone will result in an error
between the setpoint and the actual process value, because it requires an error to generate
the proportional response. If there is no error, there is no corrective response.
2.
Term I
accounts for past values of the SP
-
PV error and integrates them over time to
produce the
I
term. For example, if there is a residual SP
-
PV error after the application of
proportional control, the integral term seeks to eliminate the residual error by adding a
control effect due to the historic cumulative value of the error. When the error is eliminated,
the integral term will cease to grow. This will result in the proportional effect diminishing as
the error decreases, but this is compensated for by the growing integral effect.
3.
Term D
is a best estimate of
the future trend of the SP
-
PV error, based on its current rate of
change. It is sometimes called "anticipatory control", as it is effectively seeking to reduce the
effect of the SP
-
PV error by exerting a control influence generated by the rate of error
change. The more rapid the change, the greater the controlling or dampening effect.
4.
Tuning
- The balance of these effects is achieved by loop tuning to produce the optimal
control function. The tuning constants are shown below as "K" and must be derived for each
control application, as they depend on the response characteristics of the complete loop
external to the controller. These are dependent on the behavior of the measuring sensor,
the final control element (such as a control valve), any control signal delays and the process
itself. Approximate values of constants can usually be initially entered knowing the type of