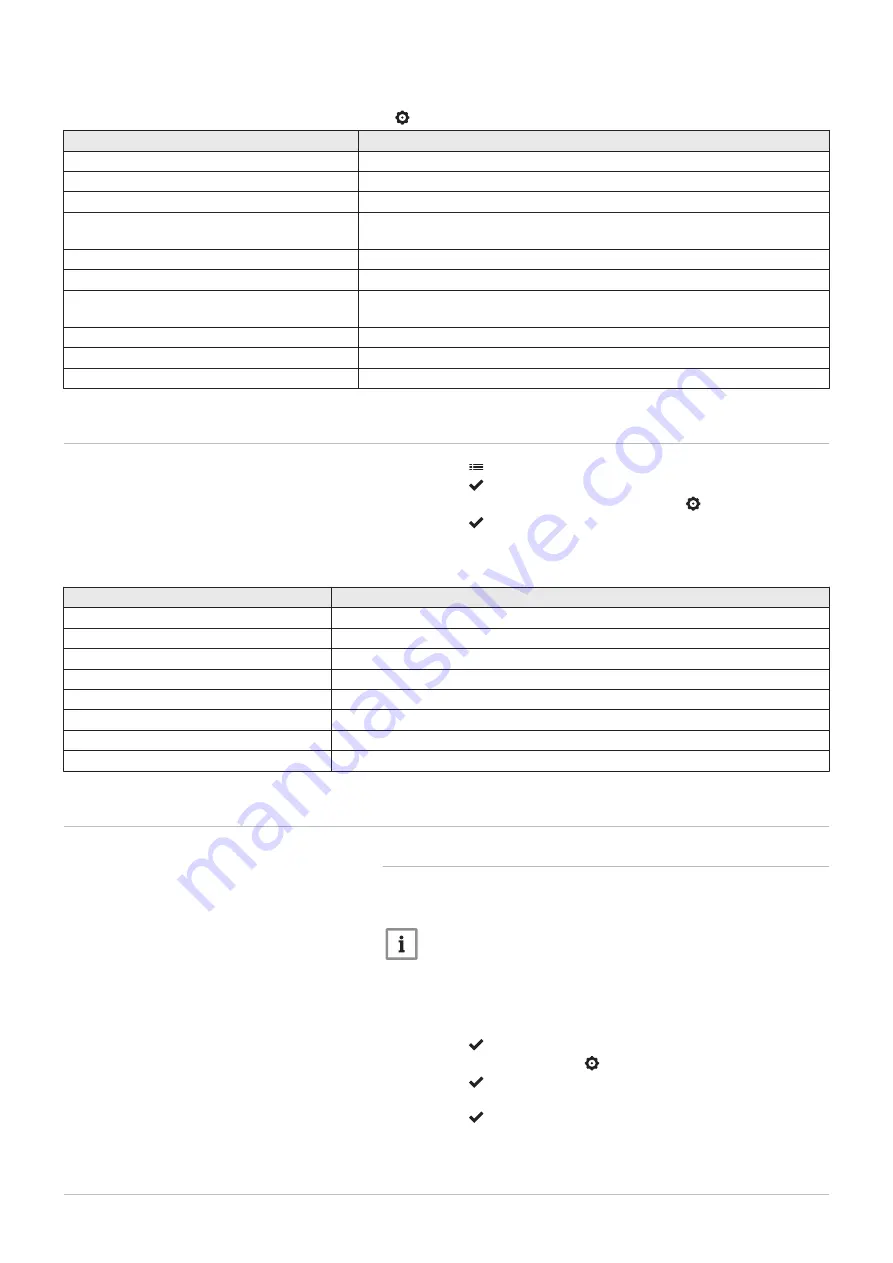
Tab.69 Extended menu to configure a heating circuit Zone configuration
Menu
Function
Short temperature change
Change the room temperature temporarily, if required
OperatingZoneMode
Select the heating operating mode: Scheduling, Manual or Antifrost
Manu ZoneRoomTempSet
Set the room temperature manually to a fixed setting
Heating Schedule
Create a timer program (up to 3 programs allowed). See: Creating a timer
Set Heating Activity Temperatures
Set the room temperature for each activity of the timer program
ZoneTimeProg Select
Select a timer program (3 options)
Holiday Mode
Set the start and end date of your holiday and the reduced temperature for
this zone
Zone friendly Name
Create or change the name of the heating circuit
Icon display zone
Select the icon of the heating circuit
OperatingZoneMode
Read the current operating mode of the heating circuit
11.4 Changing the display settings
1. Press the button.
2. Press the button to confirm the selection.
3. Use the rotary knob to select System Settings .
4. Press the button to confirm the selection.
5. Perform one of the operations described in the table below:
Tab.70 Display settings
System Settings menu
Settings
Set Date and Time
Set the current date and time
Select Country and Language
Select your country and language
Daylight Saving Time
Enable or disable daylight saving time
Installer Details
Read out the name and phone number of the installer
Set Heating Activity Names
Create the names for the activities of the timer program
Set Screen Brightness
Adjust the brightness of the screen
Set click sound
Enable or disable the click sound of the rotary knob
License Information
Read out detailed license information from the device platform application
11.5 Timer program to control the room temperature
11.5.1 Creating a timer program
A timer program allows you to vary the room temperature per hour and per
day. The room temperature is linked to the activity of the timer program.
Important
You can create up to three timer programs per zone. For example,
you can create a program for a week with normal working hours
and a programme for a week when you are at home most of the
time.
1. Select the tile of the zone you want to change.
2. Press the button to confirm the selection.
3. Use the rotary knob to select Zone configuration.
4. Press the button to confirm the selection.
5. Use the rotary knob to select Heating Schedule.
6. Press the button to confirm the selection.
7. Use the rotary knob to select the timer program you want to modify:
Schedule 1, Schedule 2 or Schedule 3.
11 User instructions
80
7734324 - v.03 - 29092020