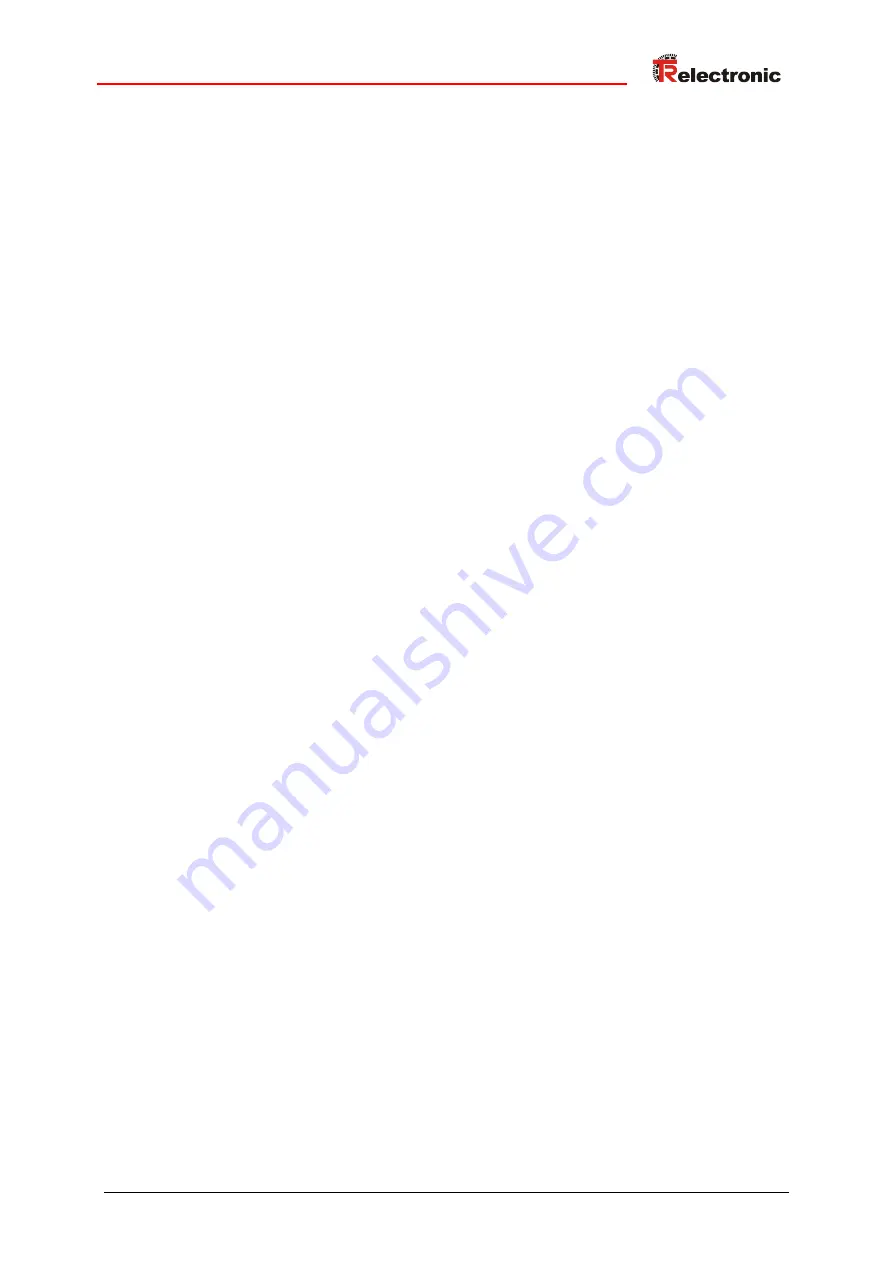
Printed in the Federal Republic of Germany
TR-Electronic GmbH 2012, All Rights Reserved
05/30/2018
TR - ECE - BA - GB - 0095 - 19
Page 47 of 56
7.4 Generating the safety program
Define the program structure, access protection via password allocation
Create modules for the program call, Diagnosis, Data, Program, Functions,
Periphery, System etc., can partly performed also automatically
Edit modules for the program call, operator acknowledgment of the safety-
oriented periphery
Define program sequence
Define cycle time for the program call of the safety program
Generate safety program
Load safety program into the control unit
Perform a complete functional test of the safety program according to the
automation task
Perform an acceptance test of the safety system by an independent expert
7.5 Access to the safety-oriented data channel
The safety-oriented data channel in the safety module of the measuring system may
only be accessed from the safety program. A direct access is not permitted.
For this reason the registers
Safe-Control
and
Safe-Status
can be accessed
only indirectly about variables. The range of the variables and the way how the
variables can be addressed is control dependent. This information must be taken from
the system documentation provided by the control unit manufacturer.
The variables must be accessed in the following cases:
● during operator acknowledgment of the measuring system after communication
errors or after the start-up phase, is indicated via the status LED see page 29
● during execution of the preset adjustment function
● when analyzing whether passivated or cyclical data are output
● if the cyclical data of the safety module are to be passivated depending on defined
states of the safety program
7.5.1 Output of passivated data (substitute values) in case of error
The safety function requires that for passivation in the safety-oriented channel in the
safety module, the substitute values (0) are used in the following cases instead of the
cyclically output values. Dependent on the control, this condition is indicated over an
appropriate variable.
● at start-up of the safety-oriented system
● in the case of errors in the safety-oriented communication between control unit
and measuring system via the PROFIsafe protocol
● if the value set for the
Window increments
under the
iParameters
is
exceeded and/or the internally calculated PROFIsafe telegram is defective
● if the permissible ambient temperature range, as defined under the corresponding
article number, is fallen below or exceeded
● if the measuring system is supplied with >36 V DC for longer than 200 ms
● Hardware related errors in the measuring system
● Scanning system, double magnetic: if the electrically permissible speed has been
exceeded which is defined in the safety manual. Since up to this limit value a fault-
free operation is guaranteed, the real output of safe data is performed therefore
only explicitly above the given limit value