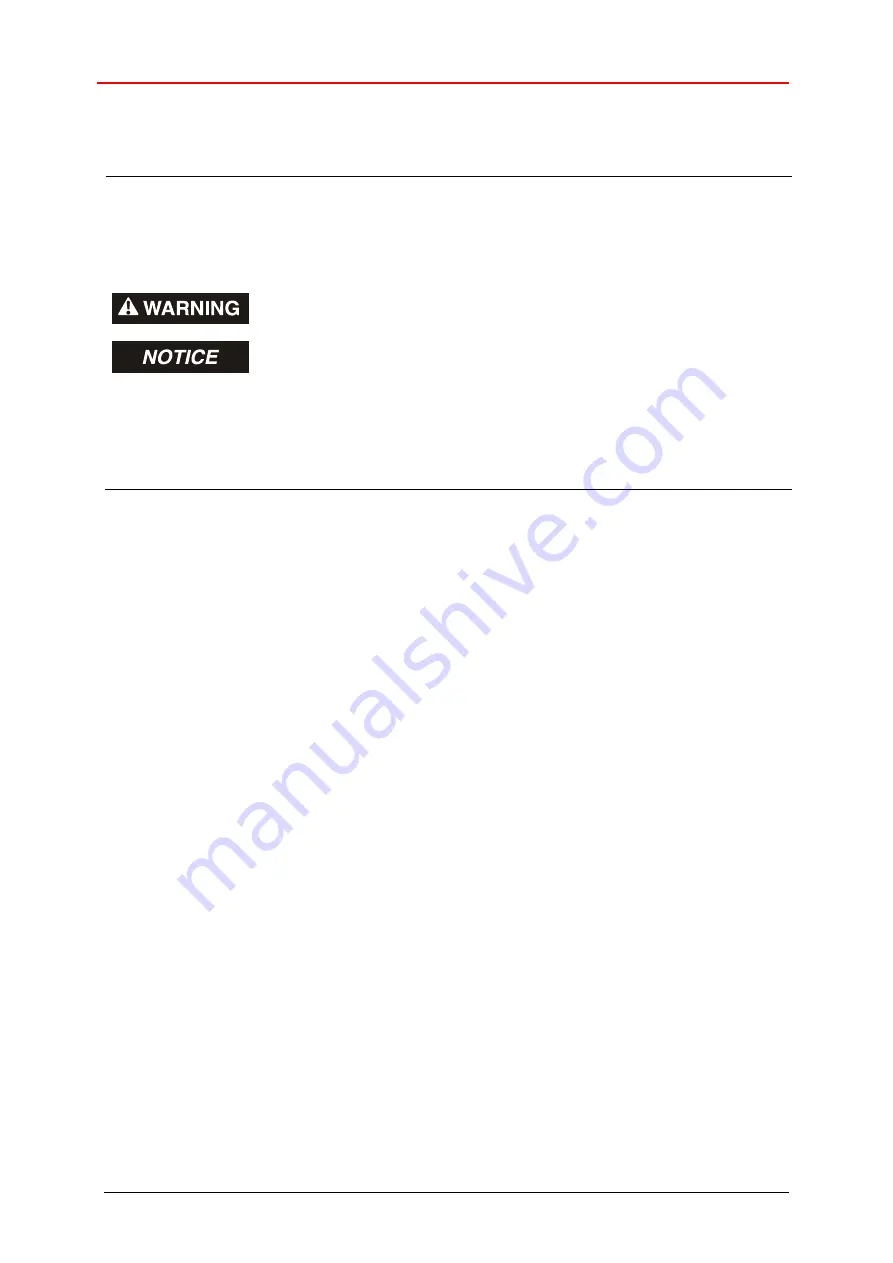
Preset Adjustment Function
TR-Electronic GmbH 2012, All Rights Reserved
Printed in the Federal Republic of Germany
Page 48 of 56
TR - ECE - BA - GB - 0095 - 19
05/30/2018
8 Preset Adjustment Function
●
Danger of death, serious physical injury and/or damage to property
due to uncontrolled start-up of the drive system during execution of
the preset adjustment function!
Execute preset function only in the standstill, see chapter “Idleness
The relevant drive systems must be locked to prevent automatic start-
up
It is advisable to protect the preset triggering via the F-Host by means
of additional protective measures, such as e.g. key-operated switch,
password etc.
The operational sequence described below is to be kept mandatorily.
In particular the status bits are to be evaluated by the F-host, in order
to check the successful and/or incorrect execution.
The new position must be checked after execution of the preset
function
The preset adjustment function is used to set the currently output position value to any
position value within the measuring range. The displayed position can thus be set to a
machine reference position purely electronically.
8.1 Procedure
Prerequisite: The measuring system is in cyclical data exchange.
Write the
Preset Multi-Turn
and
Preset Single-Turn
registers in the
output data of the safety module with the desired preset value.
The F-Host must set the variable associated to the control bit 2
0
iPar_EN
to 1.
With the rising edge, the measuring system is now switched ready to receive.
With the rising edge of Bit 2
0
Preset_Request
in the
TR-Control1
register,
the preset value is accepted. The receipt of the preset value is acknowledged in
the
TR-Status
register by setting Bit 2
0
Preset_Status
.
After receipt of the preset value, the measuring system checks that all
prerequisites for execution of the preset adjustment function are fulfilled. If so, the
preset value is written as the new position value. In case of error, the execution is
rejected and an error message is output via the
TR-Status
register by setting
Bit 2
15
Error
.
After execution of the preset adjustment function, the measuring system sets the
variable associated to the status bit 2
0
iPar_OK
to 1 and thus indicates to the F-
Host that the preset execution is complete.
The F-Host must now reset the variable associated to the control bit 2
0
iPar_EN
to 0. The variable associated to the status bit 2
0
iPar_OK
and Bit 2
0
Preset_Status
in the
TR-Status
register are thus also reset with the falling
edge. Bit 2
0
Preset_Request
in the
TR-Control1
register must be reset
manually again.
Finally, the F-Host must check that the new position corresponds to the new
nominal position.