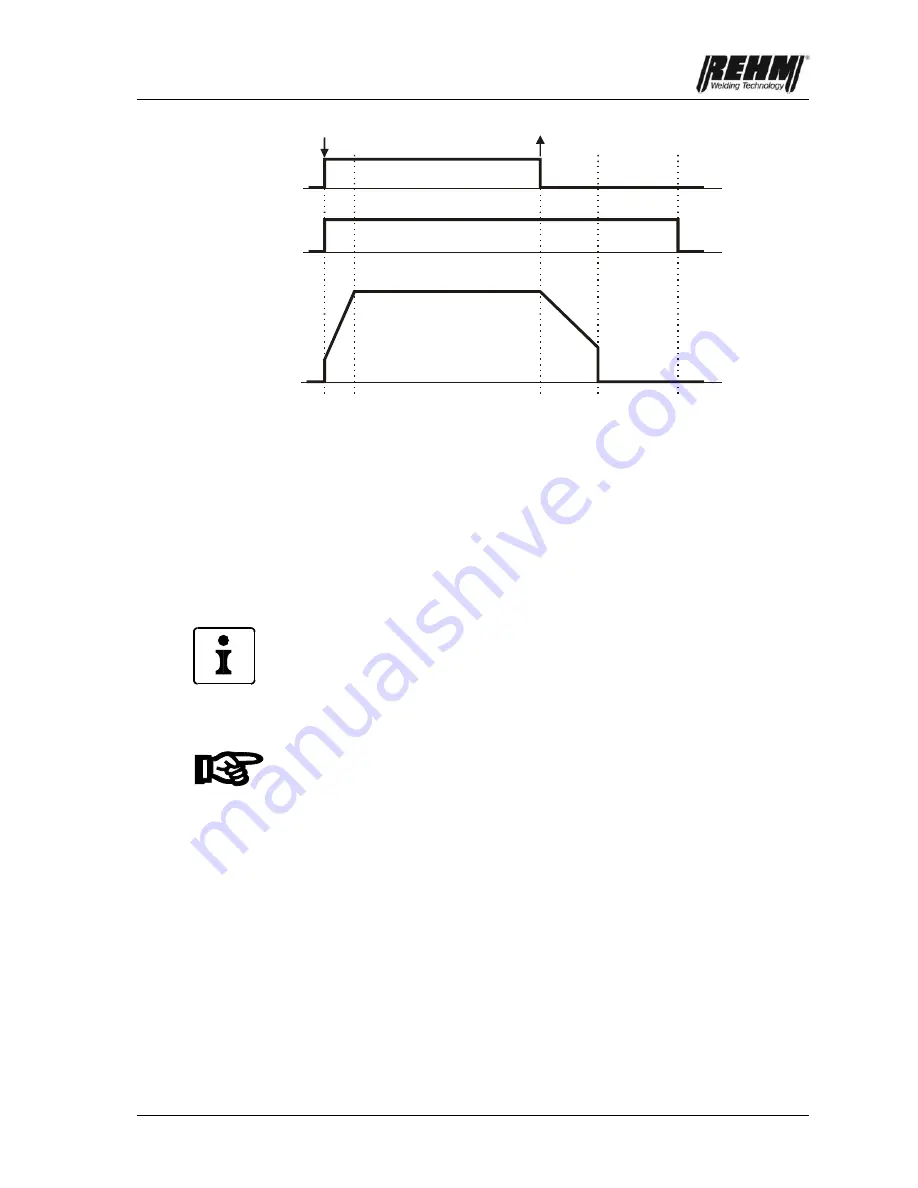
Description of function
25
Fig. 3.6 The current cycle diagram for non-latched trigger operation (2 step).
Special note:
to step 2
If the torch trigger is depressed during the downslope then the
welding current jumps back up to the I1 value. This torch operation
enables manual pulsing to be achieved. (see Chapter 3.2.6)
3.3.13 TIG welding with high voltage ignition
The setting for HF ignition is performed as described in section 3.1. The Tiger is
equipped with a high voltage ignition unit as standard. When the stick-electrode
welding mode is selected, the high frequency ignition unit is automatically
disconnected.
The high voltage ignition unit pre-ionises the gas surrounding the tip of the
electrode. This enables contact free ignition to take place between the electrode
and the workpiece in both the AC and the DC welding modes. Contact free
ignition eliminates tungsten inclusions that result in faulty welds. In both modes of
operation the high voltage generator is automatically switched off after the arc
has struck. Chapter 3.3.10 describes the re-ignition process when AC welding,
this is achieved without a high voltage generator.
This results in a significant reduction in the electrical radiation emitted by the high
voltage generator. Furthermore the AC welding process can then be completely
HF free, as has been the case for DC welding for some time now. (See chapter
3.3.14)
3.3.14
TIG welding without high voltage ignition, (Lift Arc)
The setting for Lift Arc is performed as described in section 3.1. When welding
with DC contact arc ignition (Lift Arc) ignition
can be carried out. “HF
-
Off” is
selected, microprocessor controlled contact ignition takes place to strike the arc.
In order to ignite the welding arc, the tip of the electrode must be placed on the
workpiece and the torch button depressed. The processor control system
reduces the ignition current so that the tip of the electrode does not heat up. The
electrode is then gradually lifted away from the workpiece, this action ignites the
arc under the system processor control, this results in arc ignition without HF and
also minimum wear on the tungsten electrode. This process is essential when
welding in areas where sensitive electronic equipment is in operation (e.g. repair
welds on CNC-controlled machines in hospitals etc.) and where there may be a
risk of damage caused by high-voltage.
Solenoid valve
Welding current
Torch trigger 1
t
t
t