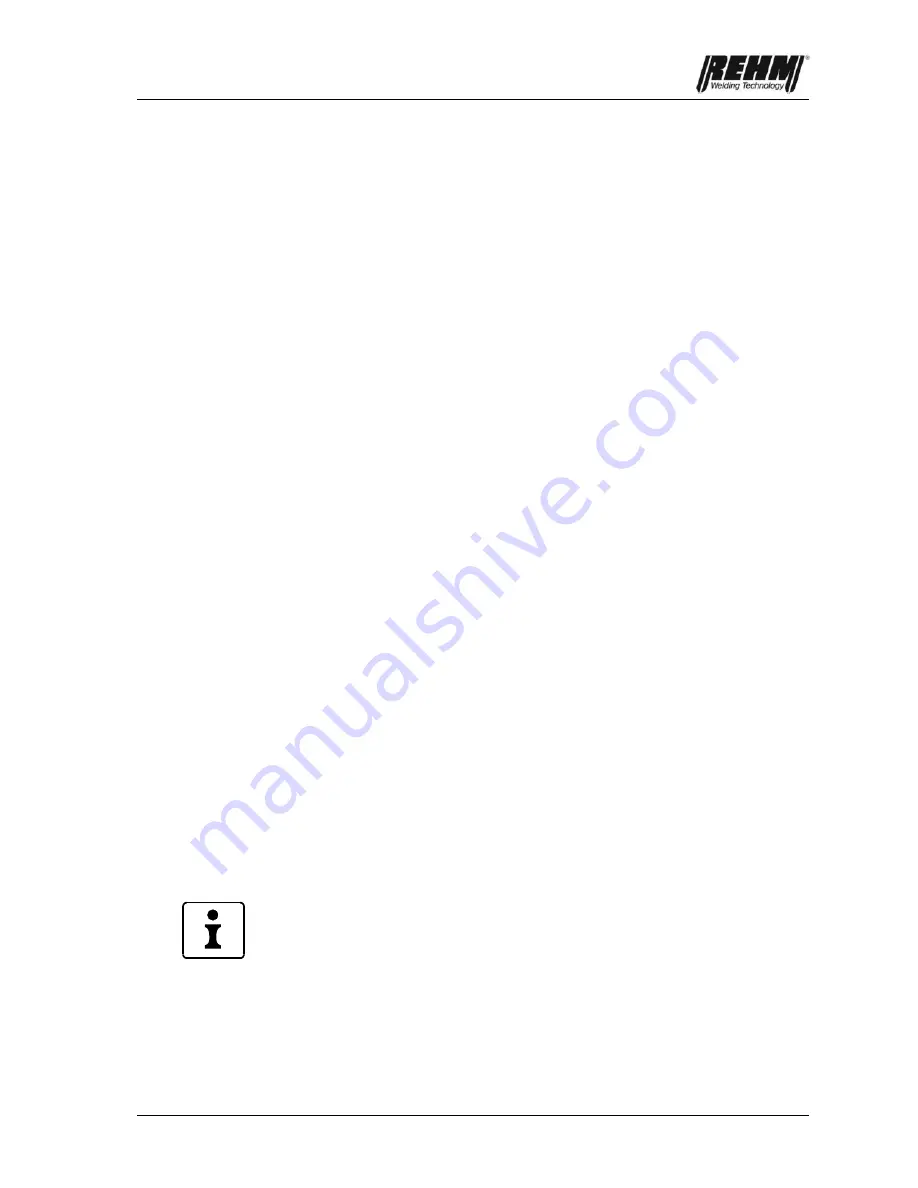
Description of function
33
prevents the electrode from overheating and burning out. The operator
terminates the short circuit simply by removing the contact between the electrode
and the workpiece.
3.5
INTIG-Energy
The highly intelligent processor ensures that the ideal ignition energy is
automatically chosen depending upon the actual weld current setting; this applies
not only for HF, but also for the Lift-Arc ignition sequence.
When "HF-On", is selected the high-frequency ignition unit is ready for operation.
To ignite the arc, the electrode must be held about 3 to 5 mm above the
workpiece. When the torch button is pressed, the shielding gas is pre-ionised by
a high-voltage, the current flows between the end of the electrode and the
workpiece so that the main arc is established. The ignition of the arc without
contact between the tungsten electrode prevents tungsten inclusions in the weld.
Once the arc has successfully been ignited the high-frequency ignition unit is
switched off automatically during welding
When “HF
-
Off” is selected, microprocessor controlled contact ignition takes place
(Lift Arc) to strike the arc. In order to ignite the welding arc, the tip of the
electrode must be placed on the workpiece and the torch button depressed. The
processor control system reduces the ignition current so that the tip of the
electrode does not heat up.
The electrode is then gradually lifted away from the workpiece, this action ignites
the arc under the system processor control, this results in arc ignition without HF
and also minimum wear on the tungsten electrode. This process is essential
when welding in areas where sensitive electronic equipment is in operation (e.g.
repair welds on CNC-controlled machines in hospitals etc.) and where there may
be a risk of damage caused by high-voltage.
The electrode diameter depends on the welding current. A diameter of 1.6 mm is
recommended for welding currents up to 70 A and 2.4 mm for higher currents.
When stick-electrode welding in either the Booster or Fuse-hold mode is
selected, then the HF-ignition is automatically switched off.
During stick-electrode welding the INTIG-Energy is always determines the
correct setting of the Hot-start current. The ignition process is carefully controlled
by the processor and ensures that the output for a soft and safe start is realised.
Even the re-starting of difficult electrodes (e.g. Basic coated) can be achieved as
the power is controlled when the electrode makes contact with the workpiece
(similar to the Lift-Arc process during TIG welding).
3.6
EPC: Continuous Mains voltage monitoring
The EPC (Electronic Power Control) system continually monitors the mains
supply voltage. As soon as an over voltage is detected, the EPC unit disconnects
the machine electronics from the mains supply. The separation is via electrical
components that due to the fault condition become overheated, and thereby alter
their electrical resistance. Thereby it is essential that when the over voltage fault
has been corrected, that sufficient time is allowed to enable these components to
reach their required operating temperature again, which can depending upon the
ambient and machine temperature be more than a few minutes.
If the Tiger is switched on and off several times in succession then the EPC unit
operates as described above. This is a safety function that prevents the inverter
from becoming damaged from voltage or current surges.