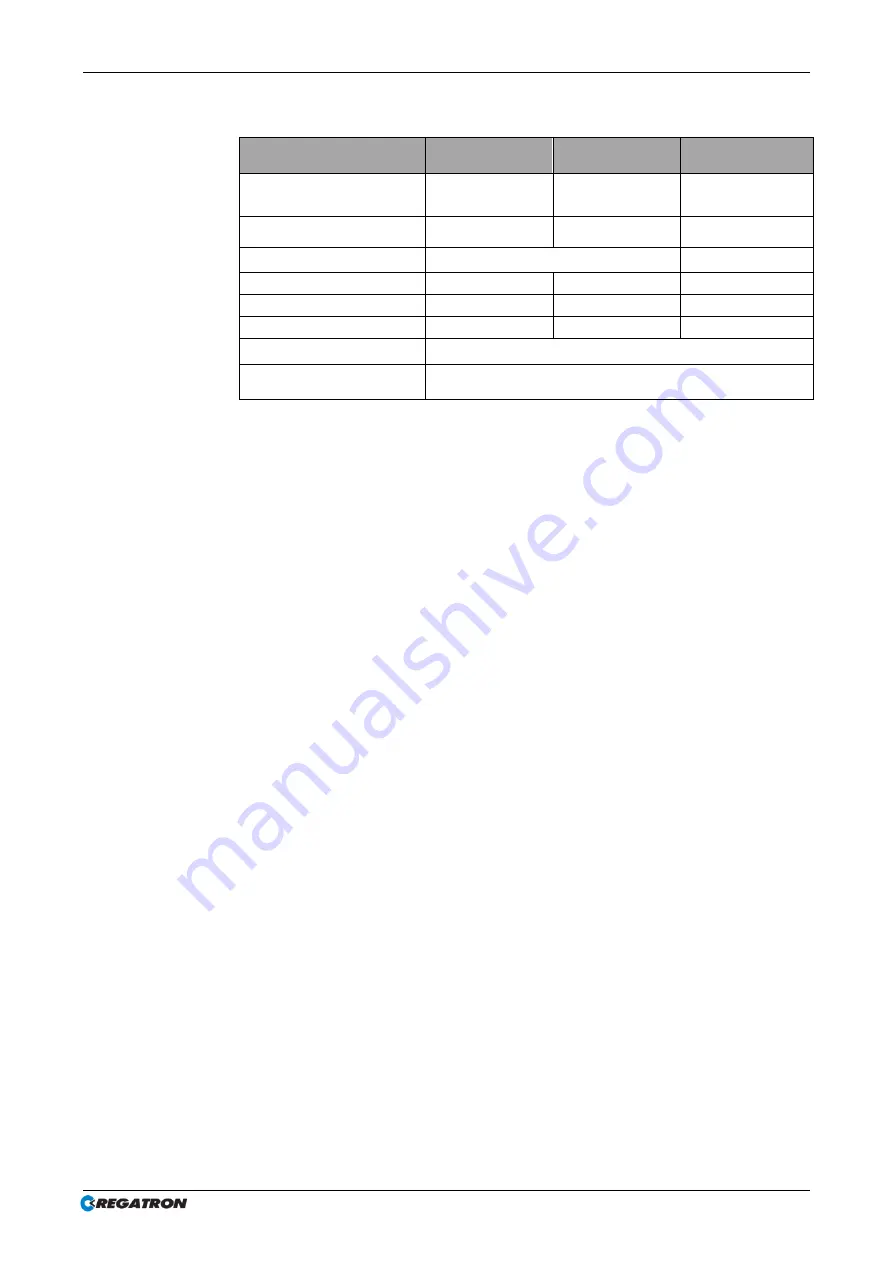
Manual
– TopCon TC.LAE
Appendix
54 / 56
2016-06-08
9.4.2.
Mains connection
Mains connection
TC.LAE.5.400
TC.LAE.5.230
TC.LAE.5.24
Line voltage
380
– 480 V
AC
100
– 240 V
AC
24 V
DC
Voltage tolerance
± 10 %
± 10 %
-10 %/ +0 %
Line frequency
48
– 62 Hz
---
Input power
200 VA
200 VA
200 W
Mains connection type
2*L + PE
L + N + PE
DC +, DC-, PE
Power factor
0.98
0.98
1
Current
0.5 A
Leakage current
L to PE
< 10 mA
Tab. 17
Mains connection
– TC.LAE devices