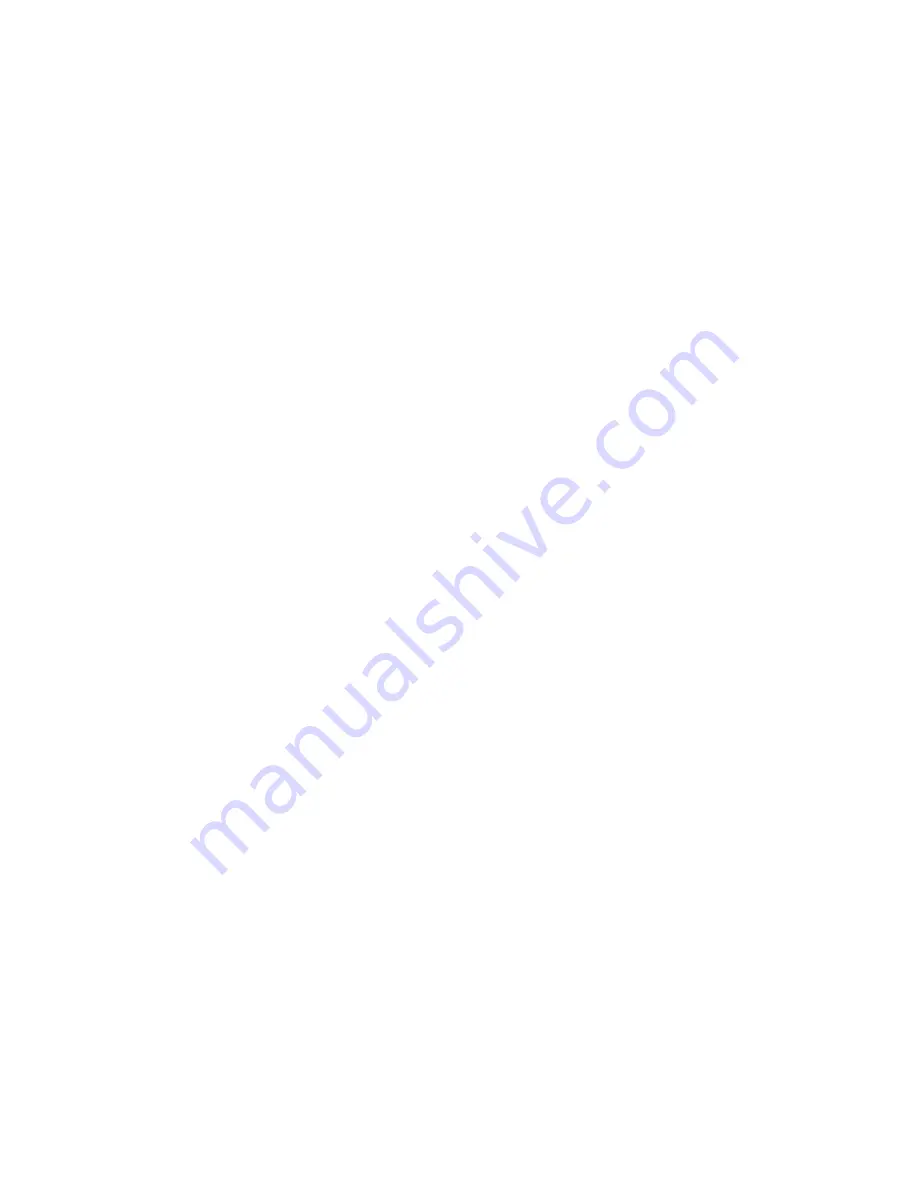
4
2. General Health & Safety Guidance
Ensure that you carefully read and fully understand the
instructions in this manual before assembly, installation and use
of this product. Keep these instructions in a safe place for
future reference.
WARNING:
for your own safety, do not attempt to operate this machine
until it is completely assembled and installed according to
these instructions.
WARNING:
When using any machine, basic safety precautions should
always be followed to reduce the risk of fire, electric shock and
personal injury.
Safe Operation
1. Use Personal Protective Equipment (PPE)
• The operation of any machine can result in foreign objects being thrown
into your eyes, which can result in severe eye damage. Protective eyewear
or other suitable eye protection or face shield should be used at all times.
Everyday spectacles only have impact resistant lenses. They are not
protective eyewear and do not give additional lateral protection.
• Use respiratory protective equipment (dust mask etc.) if the machining
operation creates dust. Exposure to high levels of dust created by
machining hardwoods, softwoods and man made composite boards can
result in serious health problems. Some imported hardwoods give off
highly irritating dust, which can cause a burning sensation. The use of
respiratory protective equipment should not be seen as an alternative to
controlling the risk of exposure at source by using adequate dust
extraction equipment.
• The use of ear plugs or ear defenders is recommended when the machine
is in use, particularly if the noise level exceeds 85 dB.
• Wear suitable protective gloves when handling cutting tools or blades.
Gloves should NOT be worn when using the machine as they can be
caught in moving parts of the machine.
• Non-slip safety footwear is recommended when using the machine and
handling large work pieces.
2. Dress appropriately
• Do not wear loose clothing, neckties or jewellery; they can be caught in
moving parts of the machine.
• Roll up long sleeves above the elbow.
• Wear protective hair covering to contain long hair.
3. Safety warnings
• Find and read any warning labels on the machine.
• It is important that any labels bearing health and safety warnings are
not removed, defaced or covered. Replacement labels can be obtained by
contacting our Customer Service Department.
4. Familiarise yourself with the machine
• If you are not thoroughly familiar with the operation of this machine,
obtain advice from your supervisor, instructor, or other qualified person or
contact your retailer for information on training courses. Do not use this
machine until adequate training has been undertaken.
5. Take care when moving or positioning the machine
• Some machines can be very heavy. Ensure the floor of the area in which
the machine is to be used is capable of supporting the machine.
• The machine and its various components can be heavy.
Always adopt a safe lifting technique and seek assistance when lifting
heavy components. In some cases it may be necessary to use mechanical
handling equipment to position the machine within the work area.
• Some machines have optional wheel kits available to allow them to be
manoeuvred around the workshop as required. Care should be taken to
install these according to the instructions provided.
• Due to the nature of the design of some machines the centre of gravity
will be high making them unstable when moved. Extreme care should be
taken when moving any machine.
• If transportation of the machine is required then all precautions relating
to the installation and handling of the machine apply. In addition, ensure
that any vehicles or manual handling equipment used for transportation
are of adequate specification.
6. The machine should be level and stable at all times
• When using a leg stand or cabinet base that is designed to be fitted to
the machine, always ensure that it is securely fastened to the machine
using the fixings provided.
• If the machine is suitable to be used on a workbench, ensure that the
workbench is well constructed and capable of withstanding the weight
of the machine. The machine should always be securely fastened to the
workbench with appropriate fixings.
• Where possible, floor standing machines should always be secured to the
floor with fixings appropriate to the structure of the floor.
• The floor surface should be sound and level. All of the feet of the machine
should make contact with the floor surface. If they do not, either re-locate
the machine to a more suitable position or use packing shims between
the feet and the floor surface to ensure the machine is stable.
7. Remove adjusting keys and wrenches
• Ensure that all adjusting wrenches and keys are removed before
switching the machine ‘ON’. There is a risk of severe personal injury or
damage to the machine from airborne objects.
8. Before switching the machine ‘ON’
• Clear the machine table of all objects (tools, scrap pieces etc.)
• Make sure there is no debris between the work piece and the
table / work support.
• Ensure that the work piece is not pressed against, or touching the saw
blade or cutting tool.
• Check all clamps, work holding devices and fences to ensure that they are
secure and cannot move during machining operations.
• Plan the way that you will hold and feed the work piece for the entire
machining operation.
9. Whilst machining
• Before starting work, watch the machine while it runs. If it makes
an unfamiliar noise or vibrates excessively, switch the machine ‘OFF’
immediately and disconnect it from the power supply. Do not restart until
finding and correcting the source of the problem.
10. Keep the work area clear
• Working clearances can be thought of as the distances between machines
and obstacles that allow safe operation of every machine without
limitation. Consider existing and anticipated machine needs, size of
material to be processed through each machine and space for auxiliary
stands and/or work tables. Also consider the relative position of each
machine to one another for efficient material handling. Be sure to allow
yourself sufficient room to safely operate your machines in any
foreseeable operation.
• Cluttered work areas and benches create the risk of accidents. Keep
benches clear and tidy away tools that are not in use.
• Ensure that the floor area is kept clean and clear of any dust and debris
that may create trip or slip hazards.
11. Consider the work area environment
• Do not expose the machine to rain or damp conditions.
• Keep the work area well lit and ensure that there is artificial lighting
available when there is insufficient natural light to effectively light the
work area. Lighting should be bright enough to eliminate shadow and
prevent eye strain.
• Do not use the machine in explosive environments eg. in the presence of
flammable liquids, gases or dust.
• The presence of high levels of dust created by machining wood can
present a risk of fire or explosion. Always use dust extraction equipment
to minimise the risk.
12. Keep other persons away (and pets)
• The machine is designed to be used by one person only.
• Do not let persons, especially children, touch the machine or extension
cable (if used) and keep visitors away from the work area.
• Never leave the machine running unattended. Turn the power supply off
and do not leave the machine unattended until it comes to a
complete stop.
Summary of Contents for DML305
Page 24: ...24 16 Parts Diagram List ...
Page 27: ...27 ...