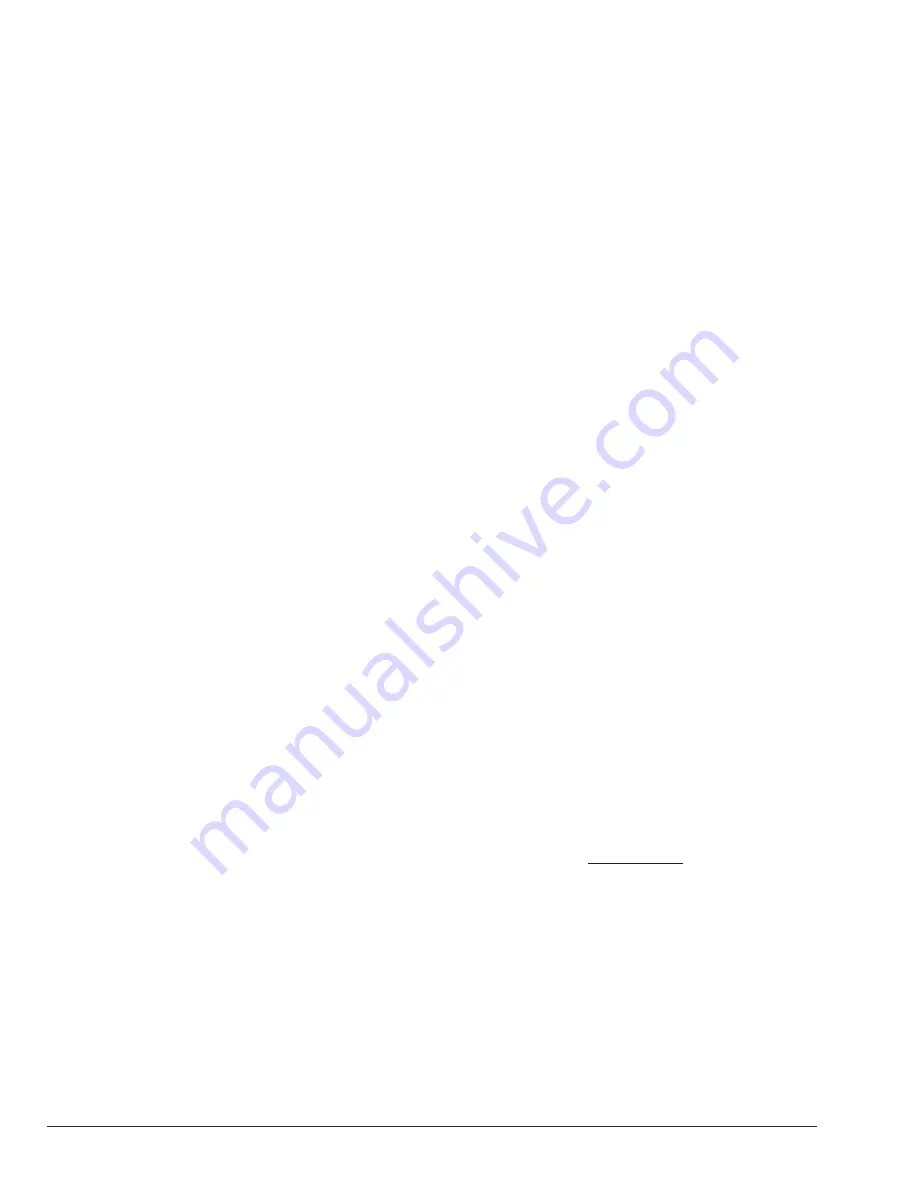
56
8.
Follow oil-lubricating instructions on pump (if
re-quired). Over-oiling will damage pump. Water-
lubricated circulators do not need oiling.
9. To avoid potential of severe burn, DO NOT REST
HANDS ON OR GRASP PIPES. Use a light touch;
return piping will heat up quickly.
10. 1Check blower and blower motor.
11. 1Check for piping leaks around pumps, relief valves
and other fittings. Repair, if found. DO NOT use
petroleum-based stop-leak.
9.1.4.
Periodically
1. Check relief valve. Refer to manufacturer’s
instructions on valve.
2. Test low water cut-off. Refer to manufacturer’s
instructions.
3. Check and clean strainer in y-strainer or suction
diffuser for debris, if equipped.
9.2.
Preventive Maintenance
Schedule
The following procedures are recommended and are
good practice for all XTherm installations.
9.2.1. Daily
1. Check gauges, monitors and indicators.
2. Check instrument and equipment settings. See
“Post Start-Up Check” on
page 51.
9.2.2. Weekly
For low-pressure heaters, test low-water cut-off device.
(With heater in pre-purge, depress the low water cut-off
test button. Appliance should shut-off and ignition fault
light should come on. Depress reset button on front of
junction box panel to reset).
9.2.3. Monthly
1. Check flue, vent, stack, or outlet dampers.
2. Test blower air pressure. See “Blower Check” on
page 49.
3. Test high and low gas pressure interlocks, if
equipped. See “Safety Inspection” on
page 50.
9.2.4. Semi-Annually
1. Recalibrate all indicating and recording gauges.
2. Check flame failure detection system components.
3. Check firing rate control by checking the manifold
pressure. See “Manifold Check” on
page 49.
4. Check piping and wiring of all interlocks and shut-off
valves.
5. Check air filter and replace as necessary.
9.2.5. Annually
1. Test flame failure detection system and pilot
turndown.
2. Test high limit and operating temperature. See “Post
Start-Up Check” on
page 51.
3. Check flame sensor.
4. Conduct a combustion test at full fire. Carbon dioxide
should be 9.0% ± 0.4% at full fire for natural gas, and
10.3% ± 0.4% for propane gas. Carbon monoxide
should be less than 100 ppm.
5. For Models H and WH only:
Check emission at
minimum fire and record CO and CO2 reading. CO
must be less than 100 ppm for all fuels. CO2 must
be between 7.5% and 9.5% for natural gas, 8.0% and
10.5% for propane gas. If CO and CO2 are not within
these ranges, stop running the unit and contact your
Raypak representative.
6. Check valve coil for 60-cycle hum or buzz. Check for
leaks at all valve fittings using a soapy water solution
(while heater is operating). Test other operating
parts of all safety shut-off and control valves and
increase or decrease settings (depending on the
type of control) until the safety circuit opens. Reset
to original setting after each device is tested.
7. Perform leakage test on gas valves. See
Figure 56.
8. Inspect and clean burner using shop air.
9. Drain heat exchanger and inspect the water side
visually for build up or debris by removing inlet stub
pipe or suction diffuser inspection cover.
9.2.6. As Required
1. Recondition or replace low water cut-off device.
2. Check sediment trap and gas strainers.
3. Check flame failure detection system. See “Post
Start-Up Check” on
page 51.
4. Check igniter. Resistance reading should be 40-75
ohms at 77
°
F (25
°
C).
5.
Check flame signal strength. (Flame signal should
be greater than 1
microampere
as measured at the
2 pins on the bottom of the PIM).
6. Check firing rate control by checking the manifold
pressure. See “Manifold Check” on
page 49.
7. Test safety/safety relief valves in accordance with
ASME Heater and Pressure Vessel Code Section IV.