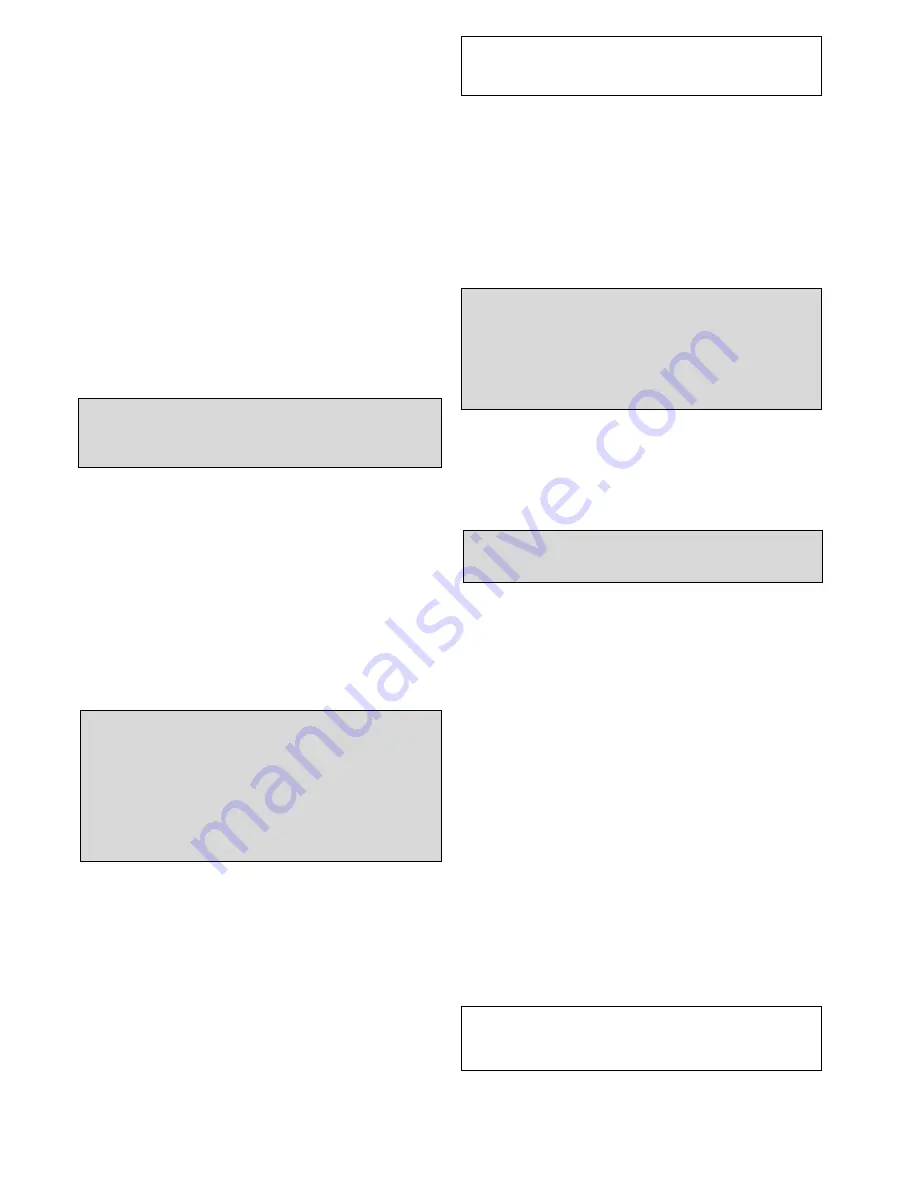
16
NOTICE:
To prevent combustion air contamination when
considering exhaust vent and intake air vent termination.
Intake and exhaust may be vented vertically through the roof
or out a side wall.
The intake and exhaust venting methods are detailed in the
Venting Section. Do not attempt to install the XPak Boiler using any
other means. Be sure to locate the boiler such that the air intake
and exhaust vent piping can be routed through the building and
properly terminated. The air intake and exhaust vent piping
lengths, routing and termination method must all comply with the
methods and limits given in the Venting section.
6. PREVENT COMBUSTION AIR CONTAMINATION
Install intake air piping for the XPak as described in the Venting
section. Do not terminate exhaust in locations that can allow
contamination of intake air.
WARNING:
You must pipe outside air to the boiler air intake
for sealed combustion operation. Ensure that the intake air
will not contain any of the contaminants below. Contaminated
air will damage the boiler, resulting in possible severe personal
injury, death or substantial property damage. For example, do
not pipe intake air vent near a swimming pool. Also avoid
areas subject to exhaust fumes from laundry facilities. These
areas may contain contaminants.
7. WHEN REMOVING AN EXISTING BOILER FROM AN
EXISTING COMMON VENT SYSTEM
Do not install the XPak boiler into a common vent with any other
appliance.
This will cause flue gas spillage or appliance malfunction, resulting
in possible severe personal injury, death or substantial property
damage.
WARNING:
Failure to follow all instructions can result in flue
gas spillage and carbon monoxide emissions, causing severe
personal injury or death.
At the time of removal of an existing boiler, the following steps shall
be followed with each appliance remaining connected to the
common venting system placed in operation, while the other
appliances remaining connected to the common venting system
are not in operation.
a. Seal any unused openings in the common venting system.
b. Visually inspect the venting system for proper size and horizontal
pitch and determine there is non blockage or restriction, leakage,
corrosion and other deficiencies which could cause an unsafe
condition.
c. Insofar as is practical, close all building doors and windows and
all doors between the space in which the appliances remaining
connected to the common venting system are located and other
spaces of the building. Turn on clothes dryers and any appliance
not connected to the common venting system. Turn on any
exhaust fans, such as range hoods and bathroom exhausts, so
they will operate at maximum speed. Do not operate a summer
exhaust fan. Close fireplace dampers.
d. Place in operation the appliance being inspected. Follow the
lighting instructions. Adjust thermostat so appliance will operate
continuously.
e. Any improper operation of the common venting system should
be corrected so the installation conforms with the National Fuel
Gas Code, ANSI Z223.1 — latest edition. Correct by resizing to
approach the minimum size as determined using the
appropriate tables in Table 13 of ANSI Z223.1 2006 of that
code. Canadian installations must comply with B149 Installation
Code.
PREPARE XPAK
CAUTION:
CAUTION:
CAUTION:
CAUTION:
CAUTION:
Cold weather handling — If boiler has been
stored in a very cold location (below 0°F (-18°C)) before
installation, handle with care until the plastic components
come to room temperature.
1. REMOVE XPAK BOILER FROM BOX
1. XPak is heavy and awkward to lift.
Care must be taken to place it in a safe location prior to installation
on the wall to prevent damage to the bottom mechanical
connections.
6 - INSTALLATION
PREPARE XPAK LOCATION
1. INSTALLATIONS MUST COMPLY WITH:
- Local, state, provincial, and national codes, laws, regulations
and ordinances.
- National Fuel Gas Code, ANSI Z223.1 – latest edition.
- National Electrical Code.
- For Canada only: B149 Installation Code, CSA C22.1 Canadian
Electrical Code Part 1 and any local codes.
NOTICE:
The XPak boiler gas manifold and controls meet safe
lighting and other performance criteria as specified in ANSI
Z21.13b 2007 – CSA 4.9b 2007
2. BEFORE LOCATING THE XPAK BOILER
1. Check for nearby connection to:
- System water piping
- Venting connections
- Gas supply piping
- Electrical power
2. Check area around boiler. Remove any combustible materials,
gasoline and other flammable liquids.
WARNING:
Failure to keep boiler area clear and free of
combustible materials, gasoline and other flammable liquids
and vapors can result in severe personal injury, death or
substantial property damage.
3. The XPak must be installed so that gas control system
components are protected from dripping or spraying water or
rain during operation or service.
4. If the new XPak is to replace an existing boiler, check for and
correct any existing system problems such as:
- System leaks.
- Incorrectly-sized expansion tank.
- Lack of freeze protection in heating water causing system and
boiler to freeze and leak.
- Excessive glycol which will affect the boiler system operation.
3. CLEARANCES FOR SERVICE ACCESS
1. See figure for recommended service clearances. If you do not
provide minimum clearances shown, it might not be possible to
service the boiler without removing it from the space.
WARNING:
The space must be provided with combustion/
ventilation air openings correctly sized for all other
appliances located in the same space as the XPak boiler.
The boiler internal front cover must be securely fastened to
the boiler to prevent boiler from drawing air from inside the
boiler room in the case of sealed combustion operation.
This is particularly important if the boiler is located in the
same room as other appliances. Failure to comply with the
above warnings could result in severe personal injury, death
or substantial property damage.
4. RESIDENTIAL GARAGE INSTALLATION
Precautions
Take the following special precautions when installing the XPak
in a residential garage. If the boiler is located in a residential
garage, per ANSI Z223.1, paragraph 5.1.9:
- Mount the boiler with a minimum of 18 inches above the floor
of the garage to the bottom of the boiler to ensure the burner
and ignition devices will be no less than 18 inches above the
floor.
- Locate or protect the boiler so it cannot be damaged by a
moving vehicle.
5. EXHAUST VENT AND INTAKE AIR VENT
XPaks are rated ANSI Z21.13b 2007 – CSA 4.9b 2007 – Fired low
pressure steam and hot water boilers. Category IV.(pressurized
vent, likely to condense in the vent). Also installations with air
dependent operation are allowed providing proper openings in
the room are provided.
Summary of Contents for XPAK 120
Page 1: ......
Page 20: ...20 Fig 10 Fig 9...
Page 21: ...21 Fig 11 Fig 12...
Page 38: ...38 WIRING FUNCTIONAL DIAGRAM Fig 40...
Page 59: ...59 14 EXPLODED DIAGRAMS Drawing 1 5 7 9 3 12a 4 6 8 12a 1 10 2 11...
Page 60: ...60 Drawing 2 17 18 56a 56a 14 15 56b 13 16 12b 19...