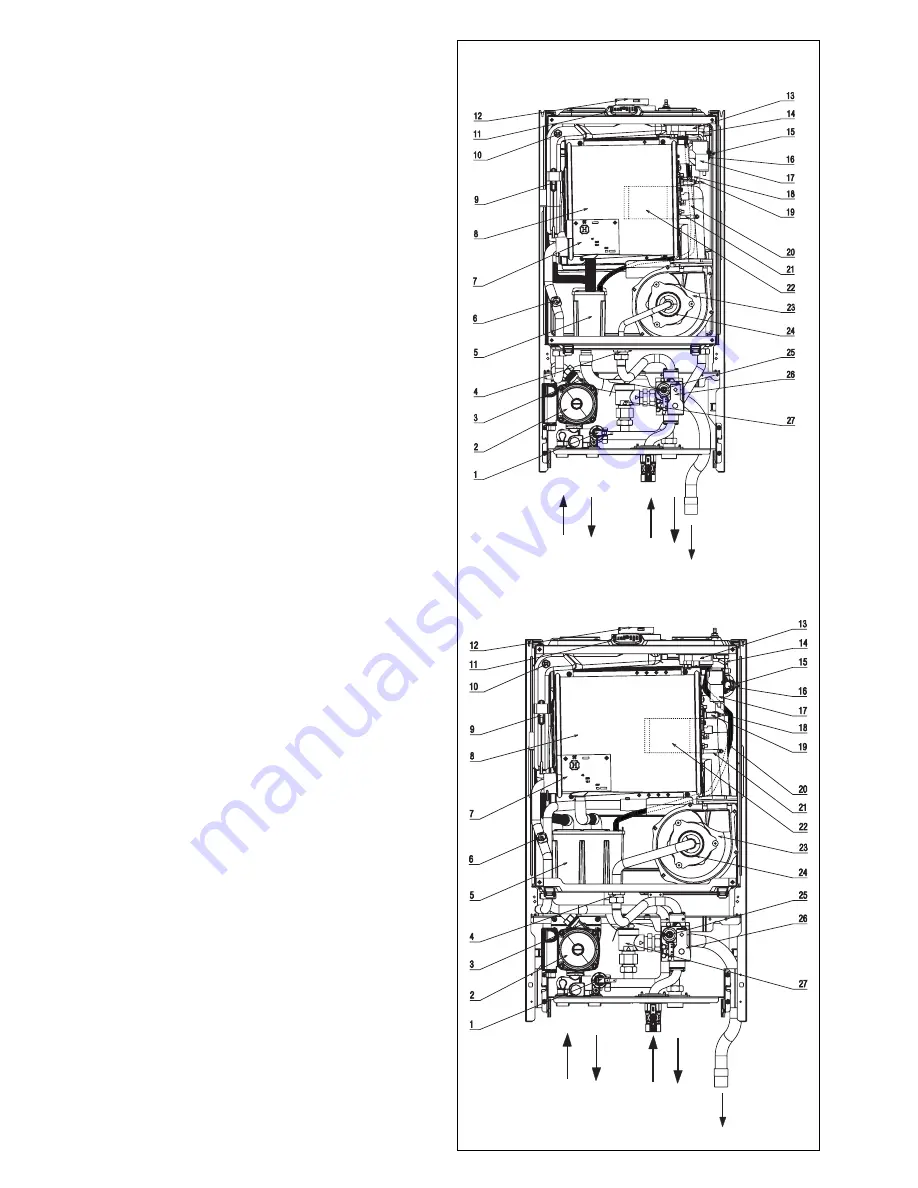
8
XPAK 85
Fig. 1
G
F
R
P
C
5 - INTRODUCTION
The
XPak
boiler is a wall hung, fan assisted, direct vent, heating
boiler only. These boilers – by design – incorporate electronic
ignition, circulating pump, pressure relief valve, pressure gauge,
and automatic bypass.
As supplied, the boiler will automatically modulate to provide
central heating outputs between 25,600 - 87,000 Btu/hr (7.5-25.5
kW) - XPak 85 and 27,300 - 119,500 Btu/hr (8-35 kW) XPak 120.
IMPORTANT
It is the law that all gas appliances are installed by a competent
person.
It is in your own interest and that of safety to ensure that the law is
complied with.
• The installation must conform to the requirements of the authority
having jurisdiction or, in the absence of such requirements, to
the National Fuel Gas Code, ANSI Z223.1/NFPA 54 Where
required by the authority having jurisdiction, the installation must
conform to the Standard for Controls and Safety Devices for
Automatically Fired Boilers, ANSI/ASME CSD-1.
• The installation should conform with CGA B149 INSTALLATION
CODE and/or local installation Code, plumbing or waste water
codes and other codes as applicable.
• Clearances from combustible material must be strictly adhered to.
• Manufacturers instructions must NOT be interpreted in anyway
as overriding statutory obligations.
The
XPak
family comprises a range of high-efficiency hot water
boilers with outputs ranging from 87,000 Btu/hr (25.5 kW) to
119,500 Btu/hr (35 kW). Each appliance is provided with a fan
powered flue outlet with an annular co-axial combustion air intake
that can be rotated – horizontally – through 360 degrees for
various horizontal or vertical applications. The XPak can also be
used with two pipe flue vent system. These appliances are
designed for use with a sealed system only; consequently they
are not intended for use on open vented systems.
This booklet is an integral part of the appliance. It is therefore
necessary to ensure that the booklet is handed to the person
responsible for the property in which the appliance is located/
installed. A replacement copy can be obtained from Raypak
customer services.
General layout (Fig. 1)
1
Water pressure switch
2
Pump
3
Bottom auto air vent (AAV)
4
Gas injector
5
Condense trap
6
Return sensor
7
H stamp main heat exchanger
8
Main heat exchanger
9
Flue thermostat
10
Flue sensor
11
Flue gas analysis test point
12
Flue outlet & air intake
13
Blocked flue switch
14
Top automatic air vent
15
Flow sensor
16
High limit thermostat
17
Ignition transformer
18
Sensing Electrode
19
Spark Electrode
20
Top automatic air vent drain pipe
21
Condensate level sensor
22
Cylindric Burner
23
Fan assembly
24
Mixer
25
Gas modulator coil
26
Gas valve
27
Pressure relief valve
R
Boiler IN connection
F
Boiler OUT connection
G
Gas connection
P
Pressure relief valve drain
C
Condensate drain pipe
XPAK 120
G
F
R
P
C
Summary of Contents for XPAK 120
Page 1: ......
Page 20: ...20 Fig 10 Fig 9...
Page 21: ...21 Fig 11 Fig 12...
Page 38: ...38 WIRING FUNCTIONAL DIAGRAM Fig 40...
Page 59: ...59 14 EXPLODED DIAGRAMS Drawing 1 5 7 9 3 12a 4 6 8 12a 1 10 2 11...
Page 60: ...60 Drawing 2 17 18 56a 56a 14 15 56b 13 16 12b 19...