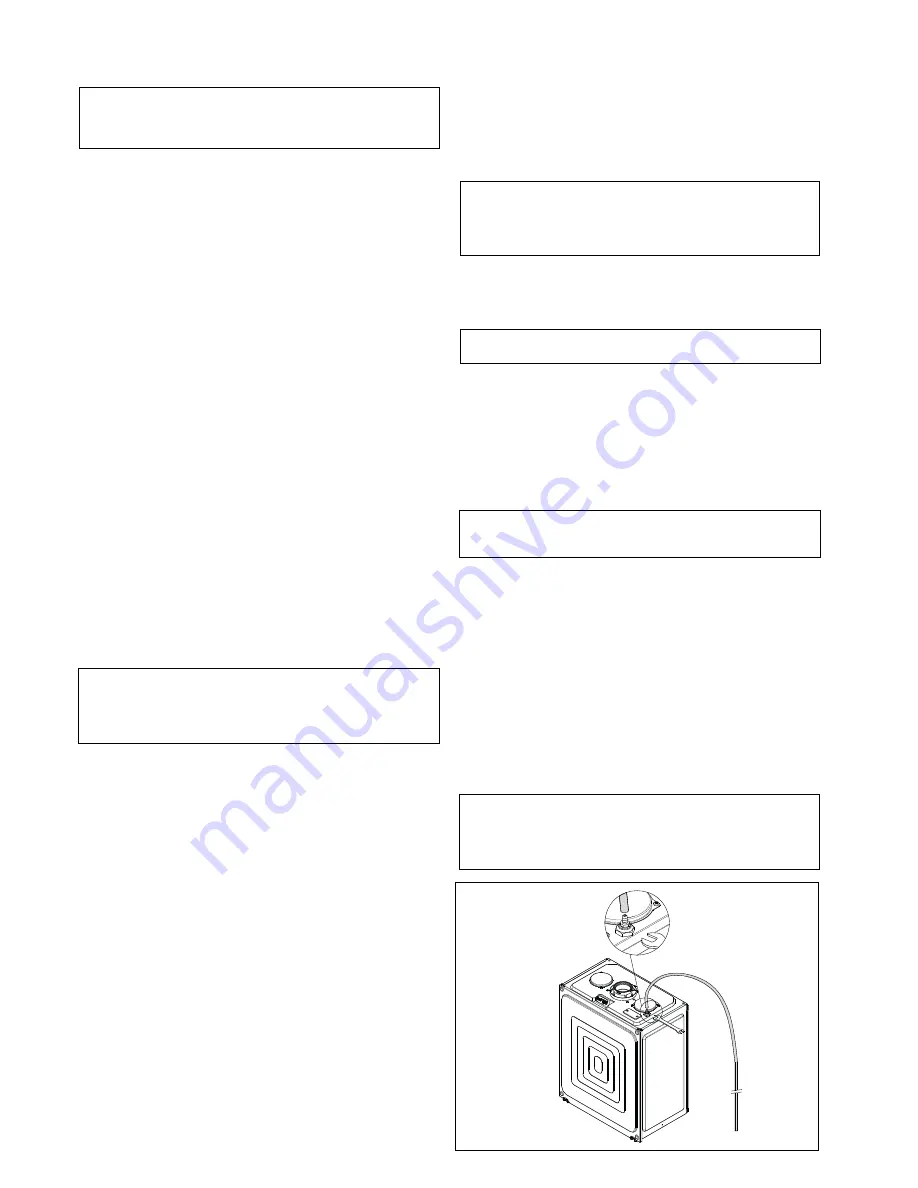
40
system the pressure gauge will begin to rise. Once the gauge
has reached 15 p.s.i. (1 bar) close both valves and begin venting
all manual air release valves, starting at the lowest first. It may be
necessary to go back and top-up the pressure until the entire
system has been filled. Inspect the system for water tightness,
fixing any leaks.
WARNING:
Eliminate all system leaks. Continual fresh make-
up water will reduce boiler life. Minerals can build up in the
heat exchanger, reducing heat transfer, overheating heat
exchanger, and causing heat exchanger failure.
5. The system may have residual substances that could affect
water chemistry. After the system has been filled and leak
tested, verify water pH and chlorine concentrations are
acceptable.
CAUTION:
It is important that you purge the system of air to
avoid damage to the heater.
5. PURGE AIR FROM BOILER
MANUAL AIR RELEASE (Fig. 42)
When the boiler has been filled for the first time or the system has
been drained and refilled, it will be necessary to release any air
that may have become trapped within the appliance heat
exchanger. Slacken the bleed screw using a 7/16” (11mm) open-
ended spanner until water is released and then close.
IMPORTANT, THERE ARE NO OTHER MANUAL AIR RELEASE
VALVES LOCATED ON THE APPLIANCE.
WARNING:
Never open the Manual Air Vent while the boiler
is hot. Allow boiler to cool to room temperature to avoid
scalding while purging.
Fill the system and watch that system pressure rises to correct
cold-fill pressure.
After the system has operated for a while, eliminate any residual air.
6. SYSTEM DRAIN (Fig. 42a)
Use a open-ended wrench (dimensions 7/16” (11 mm)) to drain
the water inside the boiler:
- attach the rubber pipe supplied to the drain valve (A)
- locate the wrench hole under the boiler
- fit the wrench to the valve
- gently rotate the wrench counterclockwise
- drain the boiler
- close the valve rotating the wrench clockwise
- remove the rubber pipe from the valve once the valve as been
closed
DANGER:
The system water temperature could be very hot,
be sure when the valve is opening that the rubber pipe is
well attached.
Frontal water flushing can occur and cause instant severe
burns or death from scalds.
Fig. 42
9 - COMMISSIONING
1. CHECK/CONTROL WATER CHEMISTRY
WARNING:
Do not use petroleum-based cleaning or sealing
compounds in heater system. Damage to elastomer seals
and gaskets in system could occur, resulting in substantial
property damage.
Water pH between 6.0 and 8.0
1. Maintain heater water pH between 6.0 and 8.0. Check with
litmus paper or have chemically analyzed by water treatment
company.
2. If pH differs from above, consult local water treatment company
for treatment needed.
Hardness less than 7 grains.
1. Consult local water treatment companies for unusually hard
water areas (above 7 grains hardness).
Chlorine concentration less than 200 ppm
1. Filling with chlorinated fresh water should be acceptable since
drinking water chlorine levels are typically less than 5 ppm.
2. Do not use the heater to directly heat swimming pool or spa
water.
3. Do not fill heater or operate with water containing chlorine in
excess of 200 ppm.
Clean system to remove sediment
1. You must thoroughly flush the system (without heater
connected) to remove sediment. The high-efficiency heat
exchanger can be damaged by buildup or corrosion due to
sediment.
2. Flush system until water runs clean and you are sure piping is
free of sediment.
Test/replace freeze protection fluid
1. For systems using freeze protection fluids, follow fluid
manufacturer’s instructions to verify inhibitor level and that
other fluid characteristics are satisfactory.
2. Freeze protection fluid must be replaced periodically due to
degradation of inhibitors over time. Follow all fluid
manufacturer’s instructions.
2. FREEZE PROTECTION (WHEN USED)
WARNING:
NEVER use automotive or standard glycol
antifreeze, even ethylene glycol made for hydronic systems.
Use only freeze-prevention fluids certified by fluid
manufacturer as suitable for use with aluminum heaters,
verified in fluid manufacturer’s literature.
Throroughly clean and flush any system that has used glycol
before installing the new XPak Boiler. Provide XPak boiler owner
with a material safety data sheet (MSDS) on the fluid used (if
requested).
1. Determine freeze protection fluid quantity using total system
water content, following fluid manufacturer’s instructions.
Remember to include expansion tank water content.
2. Local codes may require back flow preventer or actual
disconnect from city water supply.
3. When using freeze protection fluid with automatic fill, install a
water meter to monitor water makeup. Freeze protection fluid
may leak before the water begins to leak, causing concentration
to drop, reducing the freeze protection level.
3. THE HEATING SYSTEM
The appliance contains components that may become damaged
or rendered inoperable by oils and/or debris that are residual
from the installation of the system, consequently it is essential
that the system be flushed in accordance with the following
instructions.
4. INITIAL FILLING OF THE SYSTEM
Ensure both flow and return service valves are open, remove
appliance casing as described, identify the automatic air release
valves (AAV) and loosen the dust cap/s by turning the cap
counterclockwise one full turn. Ensure all manual air release
valves located on the heating system are closed. Fill the system
via proper filling method (field supplied). As water enters the
Summary of Contents for XPAK 120
Page 1: ......
Page 20: ...20 Fig 10 Fig 9...
Page 21: ...21 Fig 11 Fig 12...
Page 38: ...38 WIRING FUNCTIONAL DIAGRAM Fig 40...
Page 59: ...59 14 EXPLODED DIAGRAMS Drawing 1 5 7 9 3 12a 4 6 8 12a 1 10 2 11...
Page 60: ...60 Drawing 2 17 18 56a 56a 14 15 56b 13 16 12b 19...