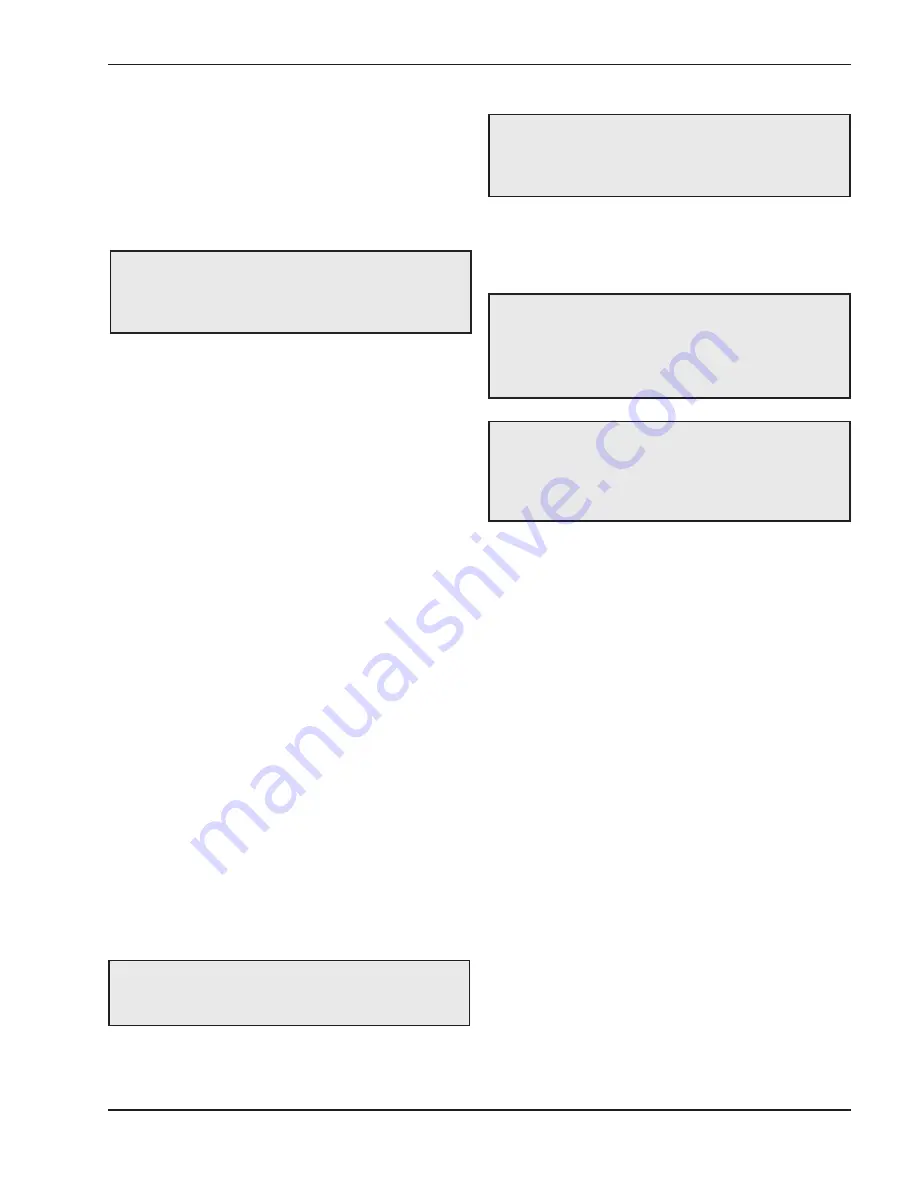
15
Canadian Installations
1. Ventilation of the space occupied by the boiler
shall be provided by an opening(s) for ventilation
air at the highest practical point communicating
with the outdoors. The total cross-sectional area of
such an opening(s) shall be at least 10% of the
area required in 2. and 3. (below), but in no case
shall the cross-sectional area be less than 10 in.2
(65 cm2).
2. For boilers using a barometric damper in the vent
system, there shall be a permanent air supply
opening(s) having a cross section area of not less
than 1 in.
2
per 7,000 BTUH (320 mm
2
per kW) up
to and including 1 million BTUH, plus 1 in.
2
per
14,000 BTUH (160 mm
2
per kW) in excess of 1
million BTUH. This opening(s) shall be either
located at or ducted to a point not more than 18 in.
(450 mm) nor less than 6 in. (152 mm) above the
floor level. The duct can also “goose neck” through
the roof. The duct is preferred to be straight down
and terminated 18 in. (450 mm) from the floor, but
not near piping. This air supply opening require-
ment shall be in addition to the air opening for
ventilation air required in 1. (above).
3. For heaters when air supply is provided by natural
air flow from outdoors for a power burner and
there is no draft regulator, drafthood or similar flue
gas dilution device installed in the same space, in
addition to the opening for ventilation air required
in 1., there shall be a permanent air supply open-
ing(s) having a total cross-sectional area of not
less than 1 in.
2
for each 30,000 BTUH (74 mm
2
per
kW) of total rated input of the burner(s), and the
location of the opening(s) shall not interfere with
the intended purpose of the opening(s) for ventila-
tion air referred to in 1. This opening(s) can be
ducted to a point not more than 18 in. (450 mm)
nor less than 6 in. (152 mm) above the floor level.
The duct can also “goose neck” through the roof.
The duct is preferred to be straight down 18 in.
(450 mm) from the floor, but not near piping.
4. Refer to the B149 Installation Code for additional
information.
CAUTION:
All combustion air must be drawn from
the air outside of the building; the mechanical equip-
ment room must communicate directly with the
outdoors.
Water Piping
General
The boiler should be located so that any water leaks
will not cause damage to the adjacent area or struc-
tures.
Relief Valve Installation and Piping
The boiler is supplied with a Section IV “H” stamped
relief valve sized for the full input of the unit. Relief
valve discharge piping shall provide no less than the
cross-sectional area of the relief valve outlet and must
be routed to a safe point of discharge. Installation must
comply with all national, state and local codes.
Temperature & Pressure Gauge
The temperature and pressure gauge is shipped loose
for field installation and must be installed within 12
inches of the boiler outlet (if possible) in an easily
readable location. Installation must comply with ASME
Section IV as well as all applicable national, state and
local codes.
Hydrostatic Test
Unlike many types of heaters, this boiler does not re-
quire hydrostatic testing prior to being placed in oper-
ation. The heat exchanger is ASME certified for 80 PSI
maximum working pressure. However, Raypak does
recommend hydrostatic testing of the piping connec-
tions to the unit and the rest of the system prior to
operation. This is particularly true for hydronic sys-
tems using expensive glycol-based anti-freeze.
Raypak recommends conducting the hydrostatic test
before connecting gas piping or electrical supply.
WARNING:
Care must be taken to ensure that the
equipment room is not under negative pressure
conditions.
NOTE:
Refer to the VERSA IC
®
Applications Guide
(Catalog #5000.72) for detailed instructions regard-
ing the various applications supported by the
VERSA IC control system.
WARNING:
Pressure relief valve discharge piping
must be piped near the floor and close to a drain to
eliminate the potential of severe burns. Do not pipe
to any area where freezing could occur. Refer to
local codes.
CAUTION:
This boiler requires forced water
circulation when the burner is operating. See Table H
for minimum and maximum flow rates. The pump
must be interlocked with the boiler to prevent heater
operation without water circulation.
Summary of Contents for 88AR-398A
Page 18: ...18 Fig 13 MODE 1 Single Boiler Primary Secondary Piping...
Page 19: ...19 Fig 14 MODE 2 Single Boiler Primary Secondary Piping with Indirect DHW on System Loop...
Page 20: ...20 Fig 15 MODE 3 Single Boiler Primary Secondary Piping with Indirect DHW on Boiler Loop...
Page 47: ...47 WIRING DIAGRAM Fig 46 Wiring Diagram...
Page 54: ...54 Fig 55 Boiler Lighting Shut Off Instructions...
Page 65: ...65 ILLUSTRATED PARTS LIST...
Page 66: ...66...
Page 67: ...67...