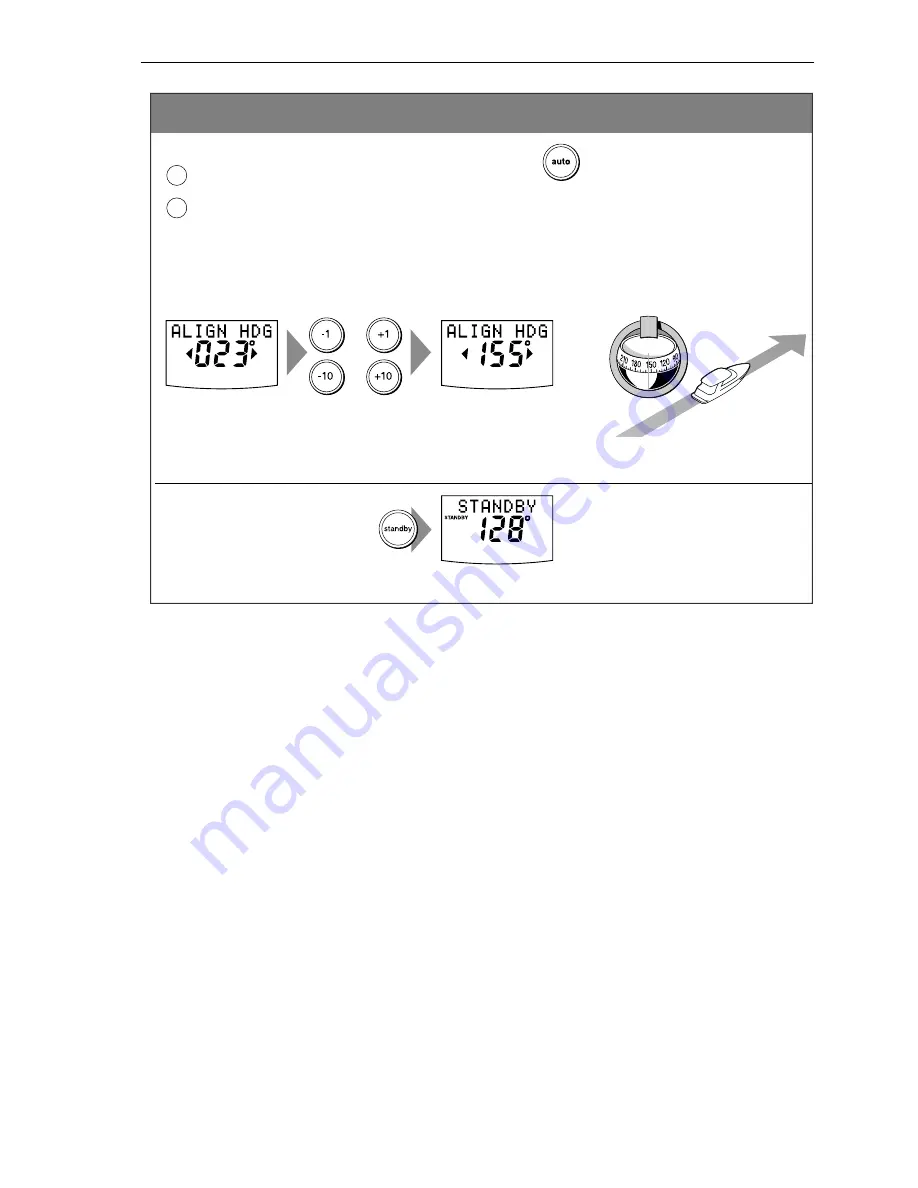
SmartPilot Verado Installation and Commissioning Guide
33
Adjusting the heading alignment
After completing the initial compass calibration, you can make further adjustments to the
alignment without having to swing the compass again.
Although the compass calibration removes most of the alignment error, small errors (a few
degrees) will probably remain.
Ideally, you should check the heading reading against a number of known headings, plot a
deviation curve, and determine the heading alignment value that will give the lowest average
alignment error. You can then enter this value on the Heading Alignment screen, as described
above.
If the average heading error is more than 5°, you should perform the compass deviation
correction procedure again, circling more slowly and in more favorable conditions.
2 sec
a
b
Save changes
To:
• save deviation correction
• save heading alignment
• return to STANDBY mode
Autopilot heading
Steering compass
=
Known
heading
or
or
Adjust the autopilot heading so it shows the same value as the boat's steering compass
Coarse adjustment:
If COG is available from GPS, press to set autopilot heading to
COG value, then fine tune manually (see below).
Fine adjustment:
If COG is not available (or after setting heading to COG),
align autopilot heading manually:
Align the autopilot heading
D8562-1
Summary of Contents for Verado
Page 8: ...vi SmartPilot Verado Installation and Commissioning Guide ...
Page 10: ...viii SmartPilot Verado Installation and Commissioning Guide ...
Page 24: ...14 SmartPilot Verado Installation and Commissioning Guide This page is intentionally blank ...
Page 66: ...56 SmartPilot Verado Installation and Commissioning Guide ...